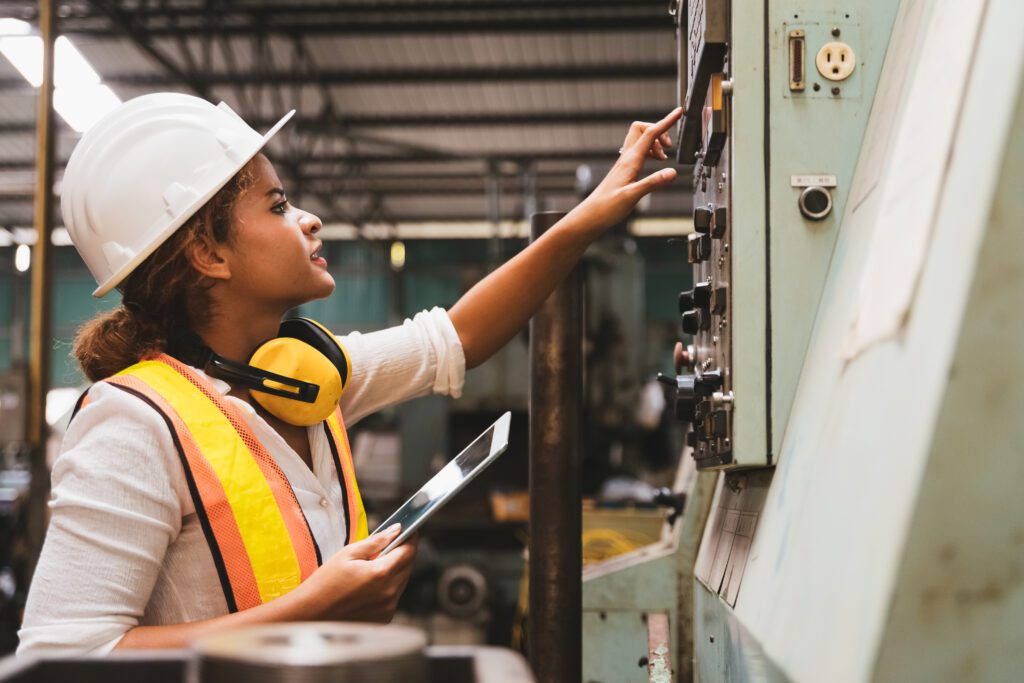
Over the last few years, the world has experienced unprecedented events which have also had unprecedented impacts on business. With so many factors out of our control, it’s even more important to be on top of the things that are. One of the best places to start is asset management. With so much capital invested in plant assets, they must operate at high levels of performance, be flexible, and deliver maximum return on investment.
Simply put, and especially given today’s business climate, every dollar spent must count.
Yet, many companies still aren’t managing their plant assets effectively. In this Forbes article, it’s surprising to hear that so many companies are still taking a reactive maintenance approach, fixing an asset once it’s broken, rather than employing preventative or predictive maintenance strategies. As they say, prevention is usually better than cure. What’s more, maintenance conducted in this way will cost more overall than preventative or predictive maintenance.
So, what are the best practices when it comes to asset management, and how can digital technology help? In fact, asset performance should really be thought of as an integral part of the overall management of a business. We think of it in terms of three increasingly advanced approaches.
1) Reduce downtime and improve uptime with asset reliability
The first thing to consider for plant asset performance is asset reliability. This is about improving the reliability of an asset, reducing downtime, and improving uptime. No one wants a situation where production comes to a standstill because one critical asset has failed. It’s not good for anyone. Downtime costs businesses in some industries up to $22000 per minute1. So, the number one priority is to ensure that plant assets are always available when needed and doing their job. It’s also important to make more efficient use of operational expenditure and maintenance budgets — as I mentioned above, efficient maintenance and high availability systems improve the value businesses get from both their CapEx and OpEx.
Downtime reduction can involve using high-availability asset control systems with intuitive diagnostics built-in, periodic asset maintenance and inspection, and manual management of spare parts stock.
EcoStruxure Plant can help with a wide range of redundant offers — controllers/networks/power supplies. It also makes it possible to access insights and diagnostics on the plant floor, helping to determine root cause/corrective action and standardize maintenance and diagnostics with control system libraries.
2) Optimizing maintenance activities with assisted uptime
Assisted uptime is about supporting maintenance activities and staff with focused strategies, planning, and tools. It involves taking advantage of the right data, systems, and technologies to guide, support, and optimize asset maintenance. At this level, stocking spare parts, scheduling, and assignment of maintenance activities, etc. are managed automatically. It also involves prescriptive maintenance techniques and monitoring asset KPIs to proactively avoid downtime. EcoStruxure Plant can enable easy linkage between plant processes and business systems to guide procurement, work schedules, etc. based on maintenance or spare parts needs.
An important aspect of assisted uptime is empowering staff to improve asset productivity. Digital technologies such as augmented reality (AR) can help guide them — not only when it comes to maintenance but also with onboarding and training. For example, it can allow them to practice high-risk procedures in AR environments so there is less real-world risk. These technologies can also help fill the labor gap I mentioned earlier.
3) Create an asset performance ecosystem with maintenance excellence
The ultimate factor in asset performance is maintenance excellence, where plant asset management is completely integrated across the business systems and departments of an enterprise. Asset productivity is key to achieving financial performance goals and multiple departments, such as HR, procurement and operations, all contribute to asset productivity. Advanced digital tools can be used to optimize maintenance performance and spare parts inventories. Artificial Intelligence (AI), for example, could analyze operating data and suggest proactive maintenance activities with greater efficiencies and precision than ever before. It can use past causes of downtime and solutions to propose corrective actions, helping staff to get things up and running in far less time. It can even analyze spare parts supply and demand to make sure the right part is always available without tying up too much business capital.
To illustrate, at this level of advancement, predictive maintenance is the norm. Assets can tell workers when maintenance is required (before they break!) and workflows can be automatically created and managed. Thanks to all business systems being linked, work is booked in the production schedule, spare parts are ordered, and maintenance tasks are assigned based on worker skills — all automatically.
With so much capital invested in assets, their management of them must be a critical part of any industrial company’s business management strategy. By creating an ‘asset management ecosystem’ where its functions are closely linked with all relevant departments and business systems, companies can become more profitable, more resilient, more sustainable, and more human-centric — for the long haul.
To learn more about asset performance management, download our free whitepaper.
Add a comment