Planned shutdowns of electrical power systems are the ideal opportunity to begin managing them more efficiently.
At certain times of year, many industries naturally shift to a slower pace of production as staff take time off to rest and unwind. But that doesn’t mean less is being done. With usual schedules on hold, businesses often use the opportunity of seasonal shutdowns to carry out important maintenance work.
But are you making the most of your planned shutdown this year? Done well, they can be about much more than just routine upkeep, becoming a chance to improve efficiency, upgrade technology, and make sure your facility is operating at its peak. With the right approaches, you can seize the opportunity of a seasonal pause to turn planned downtime to your strategic advantage. But how?
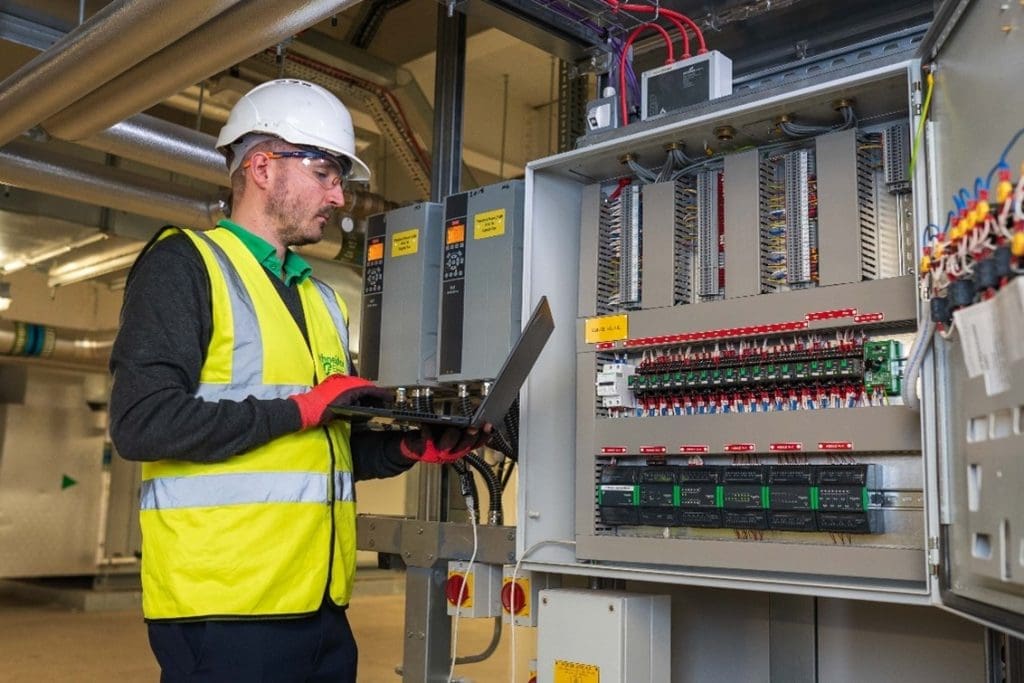
Super-charge your efficiency with a holistic view
On a day-to-day basis, it can be easy to take a plant’s electrical power system for granted. Most of the time, things don’t go drastically wrong – and regular maintenance schedules help to keep equipment functioning adequately. When there are so many other things to think about, this mentality is understandable. But it’s far from ideal. Maintaining your power infrastructure in a more proactive and discerning way can reduce costs, improve productivity and enhance safety. And ultimately, it can help you avoid expensive unplanned downtime and serious accidents. Seasonal shutdowns offer a perfect opportunity to modernize your systems to support this change – allowing your plant to move from inefficient calendar-based schedules to maintenance tailored to get the very best out of your equipment.
At Schneider Electric, we’re experienced in supporting companies to do this, using technologies that work together to provide a more in-depth understanding of power systems. At its heart, our approach is based on connecting electrical systems to the cloud – whether through new equipment with this capacity, or by adding IoT-connected sensors to older equipment. This connectivity provides ongoing readings for environmental variables such as temperature and humidity, as well as detecting wear and tear or abnormal usage. It allows us to remotely monitor the condition of the components, and its surroundings, without the need for shutdowns or in-person inspections. The information can deliver valuable early indications of emerging faults. Data from our sensors, for instance, allowed a global food and drink manufacturer to quickly identify a dangerously overheating transformer – meaning it could avoid a costly shutdown of a large factory in Latin America.
In addition, our next-generation service plans, such as EcoCare*, apply AI-powered analytics to inputs from electrical components to develop a continuous, in-depth picture of their status. As well as detailed breakdowns, this includes at-a-glance index readings on the health of equipment, and accurate assessments of when it needs maintenance. By combining IoT technology with digital analytics in this way, we can help businesses adopt a more targeted approach to looking after their systems. They can carry out work when it’s actually necessary, and avoid spending valuable time and resources when it’s not. Rather than shutting down a whole plant for three-days, for instance, it may be possible to just close down part of it for a few hours to do the necessary work. Because potential problems can be anticipated in advance, there is often less work involved. And our asset management experts can also highlight overlooked inefficiencies – where your equipment isn’t collapsing, but could be working a lot harder for you. Knowing which parts of your equipment would benefit most from modernization can allow you to significantly extend its lifetime. For some medium voltage switchgear, for example, replacing the protection relay and circuit breaker could extend the lifespan by ten to 15 years.
With Schneider Electric’s services, maintenance schedules can be based on actual data rather than theoretical assumptions. As well as significantly reducing the need for unplanned downtime, in this way our customers can also increase the length of time between planned maintenance shutdowns – typically from three to five years – and reduce the amount of work needed within these. The overall result is that these businesses have more time and resources available – both for managing their operations, and investing in a more effective power infrastructure to support them.
Not sure where to start? How a power system audit can help
So, modernizing your systems offers a lot of advantages. But actually doing it can be a daunting prospect. How do you decide what aspects need most attention and where to install sensors? And which components should you think about upgrading first?
When you’re focused on daily operations, it can be difficult to know where to start. This is where EcoConsult, Schneider Electric’s audit services, can really help, by providing a solid foundation for modernization. Our experts really understand how electrical distribution systems work. Deploying a range of techniques, they can visit your site to carry out a thorough review of the system’s health – assessing its resilience, safety and efficiency, and pinpointing where improvements will have the biggest effect.
Their findings can be surprising. In an analysis of power system audits at 400 sites, we found that electrical safety risks were identified at virtually all of them (98%). As well as direct risks such as accessible live parts, a lack of protective equipment and corroded cables, our teams also identified indirect risks, including many sites with an outdated single-line diagram (SLD), or none at all. Providing a simplified representation of how a power system functions, an up-to-date SLD is crucial for managing sites safely and reliably – but in the audits we examined, 89% did not have an adequate one. What’s more, one in eight (79%) systems we assessed included obsolete electrical equipment which is no longer available or serviceable – increasing the risk of inefficiencies, as well as accidents and unplanned downtime.
Peace of mind
These figures demonstrate how concentrating on immediate productivity challenges can distract you from looking after the systems your industrial processes depend on. It’s a bit like driving an old car. It may still get you where you need to go. But in the years or decades you’ve owned it, you haven’t realised how much the brakes and tyres are wearing out, grasped the lack of a satnav, or noticed the worrying sounds coming from the engine.
The vehicle has gradually become inefficient, unreliable and unsafe. But if you take it for servicing, mechanics can advise you on how to tackle these issues – whether that’s by installing a GPS system, replacing components, or perhaps even getting a new car. For this upfront spending, you’ll not only gain peace of mind through greater safety and reliability. Over time, the savings you make in time, energy and effort will free up resources to invest in further upgrades.
In the same way, when we carry out an audit of your electrical power infrastructure, we’ll study it comprehensively to identify the main priorities for improvement. And within a few weeks or less, we’ll provide a dependable roadmap to guide your modernization process. With this support in place, your seasonal downtime is no longer just a chance to catch up on necessary tasks. It becomes an opportunity to take strategic action to make sure your power systems – as well as you – emerge renewed, refreshed and ready for future challenges.
Explore our EcoFit™ modernization solutions and EcoCare* next-generation service plans, or schedule an audit now.
* Please verify the availability of EcoCare in your region through a local services sales representative. If EcoCare is not yet available, you can start leveraging EcoStruxure Service Plan.
Add a comment