From data centers to gigafactories, today’s critical industries will need to find new ways of managing their power systems if they are to succeed.
As efforts to decarbonize ramp up, it’s clear that electricity will be a big part of the world’s future. In the International Energy Agency’s roadmap to net zero, electricity accounts for about 50% of global energy use by 2050. That means a big increase in electric power generation – to more than two and a half times current levels. At the same time, the growth of renewable energy is making the supply of electric power more complex, variable and weather-dependent.
So the challenge of securing reliable electric power is becoming increasingly important – particularly for growing parts of the economy such as data centers, semiconductor fabrication and gigafactories. At data centers, for example, power disruptions are often a factor behind high-cost outages. In a recent survey, more than half (54%) of data center owners and operators said their most recent significant outage cost more than $100,000, with 16% reporting an impact of more than $1m. Power distribution issues continue to be the most common reason for these incidents – accounting for about half (52%).
When the costs of disruption are this substantial, operators have to make sure their electrical assets are as dependable as possible to keep unplanned downtime to a minimum. At the same time, data centers need to improve their energy efficiency to align with net zero goals. In Europe, major operators and trade associations have committed to reaching a power usage effectiveness ratio of 1.3 by 2030 under the Climate Neutral Data Center Pact – compared to the current industry average of 1.6.
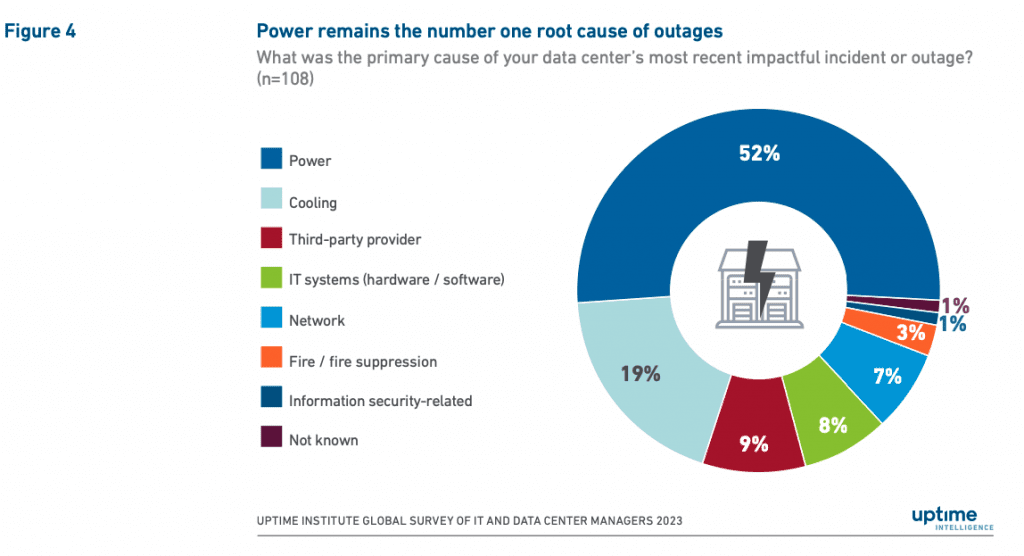
Similar challenges are being faced by the gigafactory and semiconductor sectors. Every hour lost in a semiconductor factory costs an average of $10m. And shutdowns of large gigafactories, even for a few days, can lead to losses of hundreds of millions of dollars. When we consider other factors – such as the current shortage of electrical engineers and the long design and build timeframes for new sites – there can be no doubt about how critical reliable, efficient electrical power is to industries like these.
A new approach to electrical asset management
As they face this test, many businesses in these sectors and others are modifying their power systems – to increase capacity, integrate more assets, or incorporate microgrids, for example. The result is that as electrical assets become ever more critical, the infrastructure they form part of is becoming increasingly complex. And as this process accelerates, it’s clear that it’s no longer feasible for businesses to manage these assets in the way they’ve always done. If they do, they run the risk of outages, inefficiencies and expensive repairs. As well as affecting revenue, setbacks like these can also damage a company’s reputation – weakening customers’ trust and falling short of industry standards and sustainability goals.
This is a daunting situation. But it also presents a real opportunity for organisations to adopt a more strategic way of working. And at Schneider Electric, that’s what we’re helping our customers to achieve – combining renewable electric power with digital technology at scale, in an approach we call electricity 4.0. This includes supporting a more proactive approach to electrical asset management. By installing IoT sensors on equipment, we can monitor its condition and usage remotely. But the real benefit comes from applying our AI-powered analytics to data from these sensors. This means we can accurately and continuously model the health of the hardware, to predict when it needs maintenance or repairs. It gives our customers a deeper understanding of their electrical power systems, making it possible for them to run them in more sophisticated and effective ways.
A gigafactory, for instance, may have traditionally had a schedule of shutting down operations for maintenance every few years. But by using our sensors and analytics, it could get a precise, ongoing picture of the state of each piece of equipment. This allows it to target its efforts more efficiently, carrying out more focused and less frequent interventions based on the condition of components rather than fixed timelines. By using our service plans, our customers can typically extend the periods between routine maintenance shutdowns from three to five years.
Our services offer access to the world’s largest network of electrical experts, who can assist you with monitoring and maintaining electrical equipment twenty-four hours a day, seven days a week. And as well as optimizing day-to-day operations, we can also help you to take a step back to plan a better overall strategy for electrical asset management. Schneider Electric’s teams can use insights from our analytics to design a robust infrastructure that’s ready for the demands of electricity 4.0, and develop clear policies and procedures for managing the equipment within it. We can advise you on how to prioritize investment to make the most out of your resources, and minimize waste through circular approaches – blending repairs and refurbishments with recycling and repurposing.
Boosting reliability for high-tech businesses
These capacities have the potential to benefit businesses in many different sectors. As the telecoms operator China Unicom grows its cloud computing offer, for instance, we’re supporting them through a substantial professional services team of Schneider Electric experts at two huge data centers. We provide 24/7 on-site services to manage infrastructure at these key facilities – operating and maintaining electrical equipment, while evaluating and optimizing its performance. This has helped the company greatly improve reliability and efficiency at the sites – achieving zero interruption to users’ key workloads, and saving up to 30% of operating costs through lower energy consumption. Through these improvements, the business can maintain its competitive edge while meeting the rapidly growing demand for connectivity.
Within industry, meanwhile, we’ve worked with customers such as the electronics business, Zilia (formerly SMART Modular Technologies). The firm produces specialist technology – involving semiconductors and memory modules – for purposes such as computers, smartphones, and the IoT. Zilia wanted to boost its performance and reliability. So we worked with the business to install new equipment, featuring thermal monitoring sensors, at its 15,000 square metre facility in Atibaia, Brazil. This means we can now monitor the condition of the plant’s assets continuously, using our sensor data and AI-powered analytics. The improved visibility allows the company to address inefficiencies and potential problems as they emerge, and assess the health of components that would be dangerous for engineers to access physically. On top of this, it has access to Schneider experts 24/7, to advise on and help carry out any necessary interventions.
Our partnership with Zilia has resulted in more uptime, better efficiency, and improved safety – as well as moving the facility closer to its sustainability targets. And our services can transform electrical asset management for many other businesses in similar ways. As well as cutting on-site maintenance and planned downtime costs by as much as 40%, we can work with customers to lower electrical failure risk (with its associated unplanned downtime costs) by 75%, and reduce waste by up to 90%. To find out more about what we offer, please get in touch.
To learn more about approaches for managing electrical assets efficiently, download our white paper, A Downtime-Free Future in Industry: Strategic Initiatives for Enhanced Reliability.
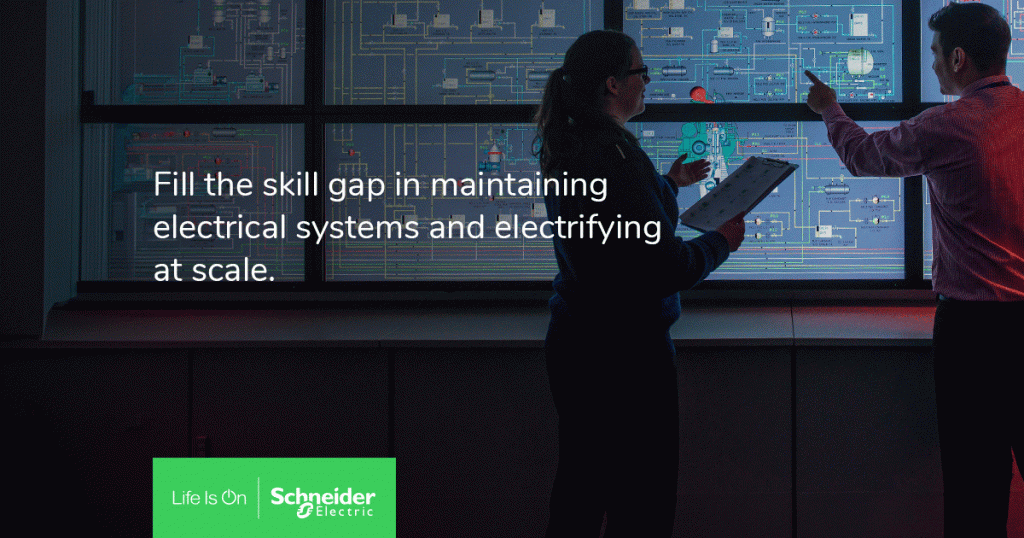
Add a comment