This blog post was co-authored with Fanny Loussararian, EcoCare Launch Leader at Schneider Electric, and Victor Marina, Digital Services Offer Manager
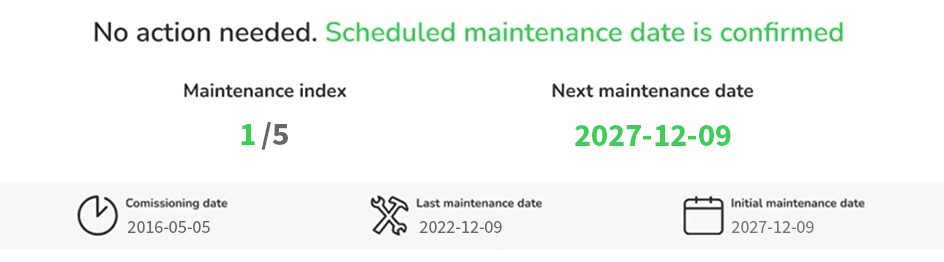
Maintaining electrical distribution, power management, critical power, and cooling systems is challenging but of the utmost importance. Like the human body, these infrastructures need regular health assessments to sustain operations and ensure safety, efficiency, and sustainability. The stakes are high in industries where even a brief interruption can lead to significant financial losses, operational downtime, compromised product quality, and even risk to human lives.
A global survey showed that unplanned downtime costs $1.25 billion to $2.5 billion annually. For many organizations, an hour of downtime costs between $50,000 and $100,000. Not accounting for potential regulatory fines or the intangible damage to brand reputation. Traditional maintenance strategies, often calendar-based and reactive, fall short in addressing these challenges. These strategies fail because they can’t identify the causes of developing failures. Nor can they optimize maintenance schedules based on the condition of assets.
Another factor leading to unexpected downtime is the assumption that electrical equipment is maintenance-free. But just like the human body is affected by environmental factors, operational stress, and age, so too can the most reliable electrical systems degrade over time. Facilities are vulnerable to unexpected failures and inefficient maintenance practices. All because they’re unaware of real-time equipment conditions.
Digital transformation and condition-based maintenance
Nowadays everything can be digitalized—even maintenance strategies. Internet of Things (IoT) technologies and advanced analytics help companies implement condition-based maintenance. These approaches focus on real-time monitoring, data analysis, and predictive insights to optimize maintenance schedules, extend equipment lifespan, and significantly reduce operational costs.
To illustrate this shift, we can look at the Nestlé Nescafé plant in Toluca, Mexico. The world’s largest soluble coffee factory embarked on a digital transformation journey. Before their digital transformation, frequent unplanned stoppages jeopardized production reliability and product quality. The plant partnered with Schneider Electric to transition to a condition-based maintenance approach. The Maintenance Index helped the plant maximize uptime, realizing substantial cost savings and operational efficiency gains.
What is the Maintenance Index?
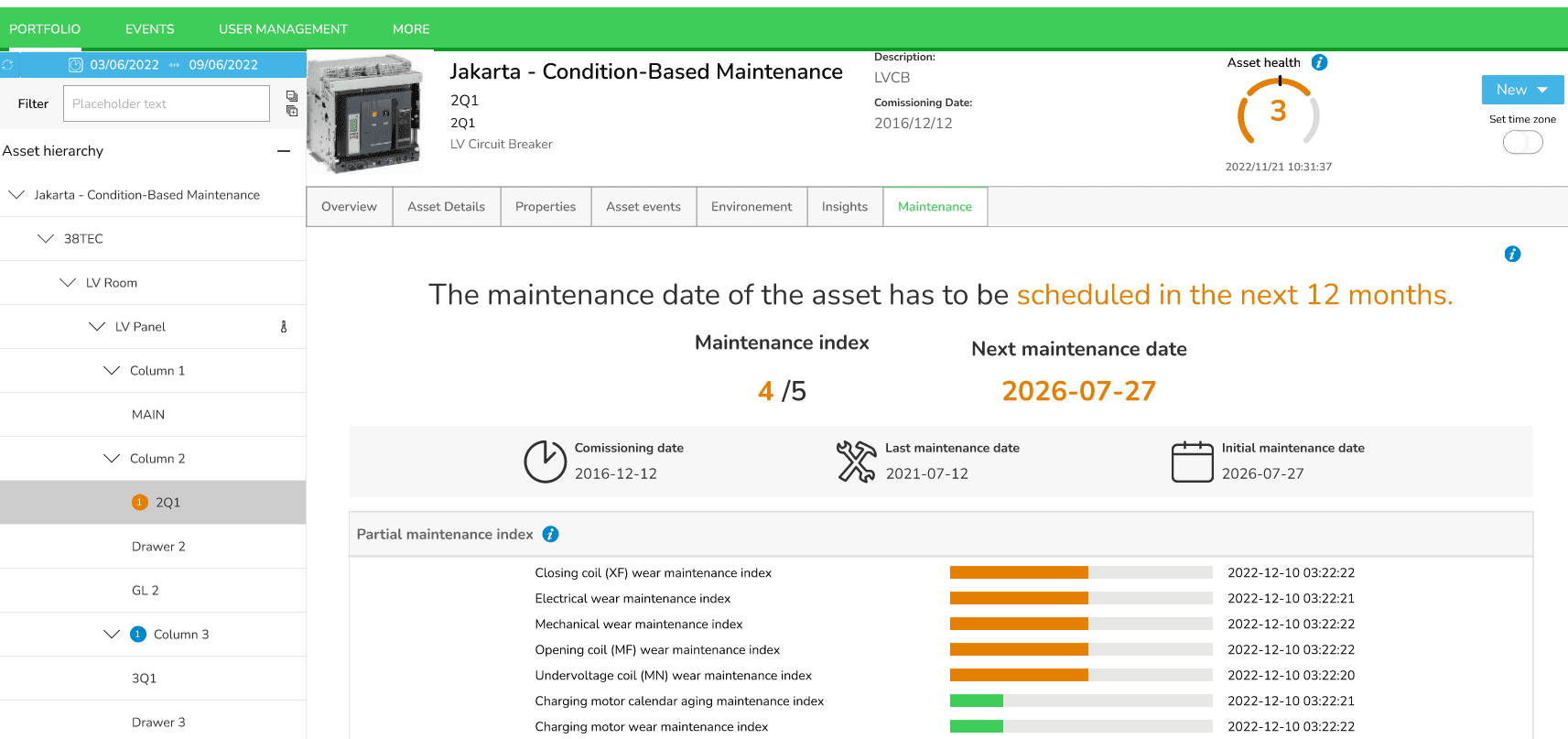
Maintenance Index elevated (4/5). Maintenance urgency increased, the next maintenance date should be scheduled earlier than originally planned.
Like a routine health checkup assesses vital signs to gauge a person’s physical state, the Maintenance Index is a dynamic, analytics-driven tool that evaluates the health and need for maintenance of electrical equipment daily. in real-time. Just as doctors use various tests to analyze bodily functions—considering factors like blood pressure, heart rate, and past health records—the Maintenance Index employs a sophisticated algorithm to analyze current operational data, environmental conditions, and the historical performance of each asset. These digital capabilities enhance the efficacy and efficiency of maintenance operations across industries.
Victor Marina, an expert on digital services at Schneider Electric, describes the Maintenance Index as:
“a decision-making tool, helping companies decide when is the best time to maintain their electrical equipment. With the Maintenance Index, as a customer, you can be reassured that if anything happens that makes maintenance urgent before failure happens, a remote expert will proactively propose earlier maintenance.”
This reflects a doctor’s personalized care plan after a health evaluation tailored to individual needs based on their health data.
The Maintenance Index provides a daily assessment of equipment health. It enables companies to move beyond rigid calendar-based schedules. This strategic approach precisely times maintenance activities based on actual asset conditions. Much like a doctor scheduling treatment based on a patient’s ongoing health assessment rather than a pre-set timetable. This method reduces planned shutdowns for deep inspections and focuses resources where they are most needed. It enhances efficiency and reduces both capital and operational expenditures.
By continuously monitoring and triggering proactive maintenance, the Maintenance Index helps extend the operational life of electrical distribution equipment. It addresses minor issues before they escalate into major failures. By identifying potential problems early, the Maintenance Index plays a crucial role in risk management. This is similar to how early detection in medical screenings can prevent severe health issues. It mitigates the risk of electrical failure, preserves the company’s reputation, and ensures that maintenance decisions are proactive and data-driven. Helping to cut the likelihood of costly unplanned downtime.
How the Maintenance Index works
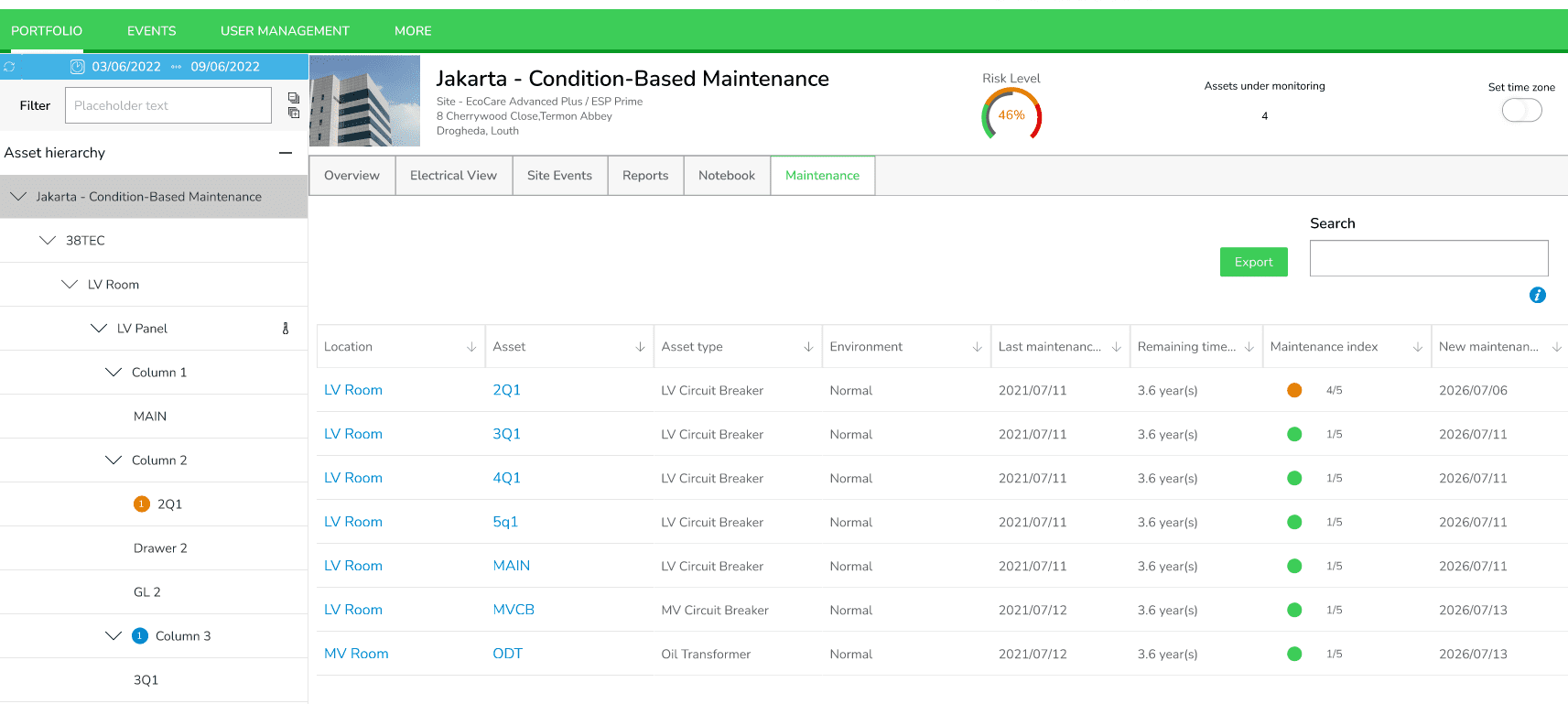
Maintenance Index – Overall Table
The Maintenance Index monitors parameters influencing the condition and performance of electrical assets. These include, but are not limited to, load capacities, operating temperatures, humidity levels, mechanical wear indicators and last maintenance inspections with their dates. Through IoT-connected sensors embedded within the equipment, data is gathered and transmitted by a gateway to a cloud-based analytics platform, which is processed and analyzed.
“The goal of the maintenance index is to adopt remote monitoring of assets. Maintenance is done not based on the manufacturer’s calendar recommendation but intelligently based on the condition of the digitally monitored site. It’s about mitigating the risk of downtime.” – Fanny Loussararian, EcoCare Launch Leader at Schneider Electric.
Understanding the Maintenance Index: A simple scale for prioritizing asset health
The Maintenance Index converts data into a scale that ranges from 1 to 5. Each number is a clear indication of the asset’s health and the urgency of maintenance needs:
- 1: no immediate action is required, affirming the equipment operates within optimal parameters.
- 2: a review of the maintenance plan might be necessary soon.
- 3 to 5: increasing levels of maintenance urgency. With 5 indicating that maintenance should be done immediately to prevent potential failures.
This straightforward index allows maintenance teams to prioritize their efforts effectively. It lets them focus on assets that need immediate attention, optimizes the scheduling of routine maintenance activities, and makes prioritizing those assets that need maintenance easier.
Proactive monitoring and support from our remote experts
To support your business operations and help our EcoCare* members get the most from their data and infrastructure, we have a dedicated and highly skilled team of experts from our Connected Services Hub available remotely 24/7. They proactively monitor, diagnose, analyze, troubleshoot, and advise on your critical electrical assets performance by leveraging our innovative digital platform. If the Maintenance Index indicates a potential issue, they will proactively contact you to recommend preventative maintenance and explain the underlying reasons, helping you avoid costly downtime.

Schneider Electric Remote agents monitor the Maintenance Index and, if it increases, promptly contact the customer to recommend earlier maintenance and provide detailed explanations.
Conclusion
Adopting the Maintenance Index for managing electrical systems is like enrolling in a proactive health program for critical infrastructure. Regular health checkups can prevent severe illnesses by catching symptoms early. With the Maintenance Index, companies can perform maintenance before costly failures occur. This strategic tool enhances the reliability and efficiency of electrical systems and transforms traditional maintenance methods into intelligent, data-driven tailored strategies.
Real-time data and analytics help companies secure uptime and optimize maintenance schedules. This reduces the risk of electrical failure and associated costs. As a doctor’s visit assesses various health metrics to provide personalized care, the Maintenance Index evaluates the health of electrical assets to customize maintenance interventions. Maintenance scheduling is now based on the actual condition of the equipment being monitored, rather than a set schedule. Mirroring the tailored approach of modern preventative healthcare.
As we continue to evolve in the digital age, the Maintenance Index stands out as a crucial tool. By adopting this innovative approach, companies can ensure that their maintenance strategies are cost-effective and integral to long-term operational stability. In the competitive landscape of industrial operations, where downtime can equate to significant financial loss, the Maintenance Index is indispensable for maintaining continuous, efficient, and safe operations.
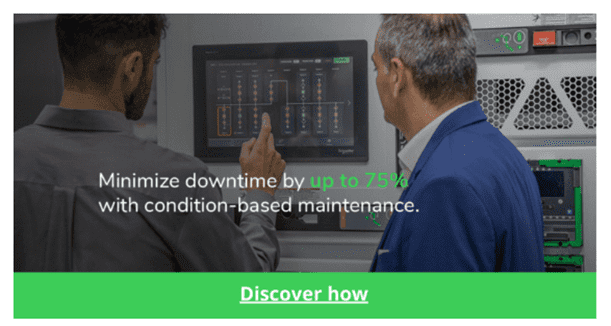
Ready to enhance your maintenance strategy?
The Maintenance Index is part of our EcoCare* membership. Discover how it can transform your approach to equipment maintenance and significantly reduce downtime risks.
Reach out to your Schneider Electric sales representative today to explore how you can start benefiting from smarter maintenance solutions tailored to your needs. Optimize your operations with the power of advanced analytics.
* Please verify the availability of EcoCare in your region through a local services sales representative. If EcoCare is not yet available, you can start leveraging EcoStruxure Service Plan.
Add a comment