Many people have asked me how we have been managing our global supply chain during the COVID-19 pandemic and what steps have had the most positive impact. I would say that people, digitization and automation have been the three key factors that have enabled us navigate the crisis and stay on course to realize our mission of building the supply chain of tomorrow. Let me share with you some of the things that we did and the lessons that we’ve learned as a result.
Go digital early
Companies in the e-commerce sector that digitized early, such as Amazon and Alibaba, have been better placed to weather the crisis. We, at Schneider Electric, have also benefitted from early digitization focus in our supply chain. Having initiated the digital transformation of our supply chain more than three years ago, we were able to immediately leverage an array of digital tools that have allowed us to operate remotely right from the start of the outbreak. For example, we were able to very quickly offer our customers remote Factory Acceptance Tests (FAT) on our Engineered to Order solutions, as well as remote Assisted Field Services, enabling us to remain agile, pivot fast, and be resilient during the lockdown.
Some of the digital technologies and automation solutions that have facilitated remote work for our non-critical employees and helped those teams continue to collaborate effectively include:
1. Remote team meetings
Every morning in our Smart Factories and Smart Distribution Centers, employees would gather together for Short Interval Management (SIM) meetings to analyze their performance data, plan their work, and coordinate their teams. Overnight, we were no longer able to hold these meetings in person. However, by using standardized digital applications that were deployed at our sites before the outbreak, we were able to conduct these SIM meetings remotely. The applications we use automatically connect relevant performance information and trigger action workflows so that we could maintain our manufacturing performance levels while still ensuring the physical distancing necessary to protect the health of our employees.
2. Remote collaboration for predictive maintenance
Another example is the use of EcoStruxure Machine Advisor. It can detect issues that generate predictive maintenance alerts so service staff can monitor the performance of our machines from home and remedy problems before they cause a failure. This cloud-based application provided crucial support for our engineering team in Singapore so they could collaborate effectively with a partner in Europe to remotely deploy predictive maintenance on a production line in our Cavite Smart Factory in the Philippines.
3. Business continuity with remote Factory Acceptance Tests (FAT)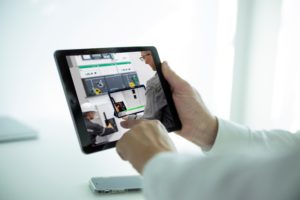
FATs are required for a large percentage of engineered solutions and are normally conducted onsite at a plant. Before installing the new solutions at a customer’s site, the FAT provides an opportunity to confirm that the solution meets all the necessary standards and customer requirements. During the initial lockdown, we were still able to conduct over 90% of our Factory Acceptance Tests remotely as we had previously equipped all of our Smart Factories with remote FAT capabilities. Watch the video to learn more.
Automation initiatives to succeed in the new normal
4. A culture of continuous improvement
Automation is at the center of everything we need to do in a world where social distancing and remote working are the new normal. We want to accelerate the pace of our digital transformation and have been investing in remote expertise. We are exploring quick-win digital solutions to build more resilience and visibility into our supply chain. This is enabled by large scale connected equipment, which is the path to site benchmarking and predictive maintenance, improving at scale the Mean Time Between Failure of our critical lines, and thus improving our service levels and performance.
5. Enhancing visibility into our operations
During the recovery phase, it has been critical to improve visibility into our operations. We have built manufacturing data dashboards that bring information directly from the shop floor, facilitating operational decision-making on resource allocation and prioritization. We are also deploying automated analytics, powered by machine learning, that will help us to identify the areas we should examine more closely.
6. Accelerating the pace of our digital transformation
Implementing new, automated technologies in our supply chain operations is important to help us face future disruptions and lockdowns with minimum impact. Here, too, EcoStruxure Machine Advisor has been key. It enables machine builders to provide new services to machine operators for each installed machine at any production site anywhere in the world. The way we are using this solution in our Smart Factories in Asia is to benchmark the performance of our machines in Indonesia, the Philippines, Thailand and India. It allows us to see where we are operating most efficiently and replicate the conditions across the network – thus accelerating our digitization efforts.
To learn more about how deploy EcoStruxure in our Smart Factories and Smart Distribution Centers, or take a virtual tour of one of our Smart Factories, click here.