Are you interested in pursuing a more sustainable lifestyle at home? Do you know that energy consumption is the aspect that most significantly impacts the carbon emissions emitted by our houses and apartments? But how can you make an impact? What are the methods to reduce energy consumption in homes and thereby lower the CO2 emissions from our homes?
In this series of innovation talks, we will provide some clues on how you can make a real impact on the planet, comfortably seated on your sofa.
Let’s start with the first one in the series and discuss the materials we use to power our homes. I had the pleasure of interviewing Bidisha Nagaraj, Vice President Marketing, Home & Distribution. Together with Bidisha, we’ll explore how discarded fishing nets gave birth to light switches. You will understand why it is such a challenge to use recycled content for electrical materials. And you will learn about the partnership which made this innovation possible as well as the other initiatives to replace traditional plastics with recycled options.
Host: Johanne Guigue, Home and Distribution Communications Leader, Schneider Electric
Speaker: Bidisha Nagaraj, Vice President Marketing, Home & Distribution, Schneider Electric
This talk covers:
- How discarded fishing nets become a light switch and the challenges of making this happen for electrical materials.
- The partnership that made this innovation possible.
- Other initiatives to replace traditional plastics with recycled options.
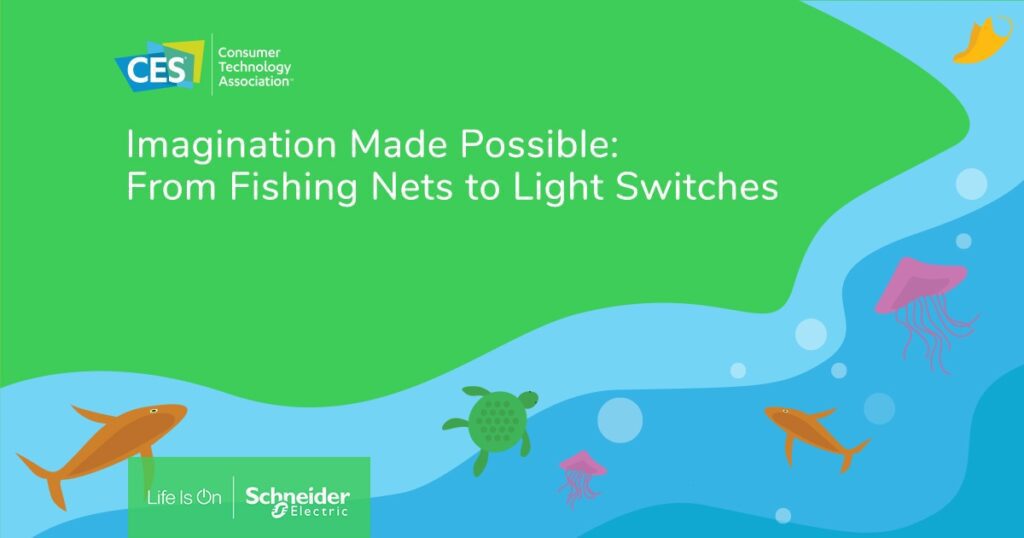
Johanne: In these talks, we will explore different routes to make our homes more sustainable while doing our part to save our planet. And one of these routes is quite extraordinary. It involves the transformation of fishing nets retrieved from the ocean into beautiful light switches for the home. Can you give me the backstory on this, Bidisha?
Bidisha: Well, as you know, Schneider Electric has great ambition when it comes to sustainability. We are the sustainability advisors for our customers, whether they’re factories, data centers, buildings, simple homes, large corporations, or individuals like all of us here. At Schneider, we believe if we talk the talk, we have to walk the walk. We have defined for ourselves seven commitments: climate, resources, trust for our employees and our suppliers, diversity, equity and inclusion, respect for all generations, and local impact on communities.
As part of our commitments, we have established two concrete objectives for homes in relation to the scarcity of resources:
- Make all packaging 100% green by 2025.
- Use 50% green materials in our products by 2025.
With these objectives in mind, we started to work with strategic suppliers to find ways to decarbonize our materials. One of them is Royal DSM, a global science-based company with a sustainable vision. One of their departments explores greener, lighter, and smarter materials. They are looking to help their customers transition their entire materials portfolio to alternatives that are bio-based, recycled-based, circular, and low-carbon. That’s how we came to discover their new material range made out of fishing nets!
Johanne: There are so many sustainability aspects to this story, as I understand it: DSM not only found a new material for their compound, they also created a local economy to collect, sort, and pre-process the fishing nets in India. We are very proud to be part of this remarkable endeavour! So tell me, Bidisha, how do these fishing nets become the light switches we use in our homes?
Bidisha: The fishing nets are made of 100% polyamide, which makes them an ideal candidate for technical plastics that fulfill critical criteria for light switch safety and durability.
After cleaning, DSM is able to strengthen the material with glass fiber. This is a complex process, enabling a solution that is unlike the virgin plastics compound used today. It’s very important to choose a compound that will maintain its integrity over time and be consistent from batch to batch. That’s the main challenge for plastics coming straight out of the ocean.
Johanne: I understand this was a challenging task from DSM’s perspective. Now how does this material meet the necessary requirements for customers like us? How did we manage to make this a reliable material for a light switch?
Bidisha: You are fully right; we cannot compare ocean plastics used for shoes or buckets with the ones used for a switch. That’s where our expertise comes in! Making a product that meets the strict safety and regulatory conditions across Europe is no easy feat, due to the specific requirements of electrical components. Particularly in switches and sockets, mechanical and electrical endurance are mandatory. This includes high-temperature resilience in case of overloads or short circuits. So when DSM presented us with their new material, called Akulon® RePurposed, we worked together to ensure we were in compliance.
The Schneider and DSM teams have worked closely over a number of months and were able to adjust the Akulon® RePurposed material for the requirements of electrical components. So we created the Merten switch and socket, made out of discarded fishing nets from the ocean. It’s the result of a partnership that we are extremely proud of.
Johanne: That is truly amazing! This is certainly our flagship initiative to make this planet greener. But I understand throughout our organization, we are piloting different initiatives to achieve our goal of 50% green materials in our products. Can you elaborate on these initiatives, Bidisha?
Bidisha: There are different paths we are exploring, all of them exciting.
The first is to make circular economy part of our practices. Up until now, our economy has been very linear: We take, we make, and then we discard, as has been the case for most electrical components for the last century. This needs to change.
With circular economy, the principle is to consume and produce in a responsible and sustainable way, very much mimicking nature. As a consequence, the circular-economy design principle impacts production by sourcing materials that are renewable and more durable, and then designing products that have a long life and are easier to repair, reuse, and repurpose.
It’s about doing good and doing well, core tenets of any sustainable practice.
From this perspective, we are very proud that our German-made Merten range of switches and sockets has been accredited with Silver Cradle-to-Cradle certification, which is the highest recognition for this category worldwide. We also received the Bronze Cradle-to-Cradle certification for three other ranges: Odace, Unica, and Ovalis, all of which you can discover in our booth. This is part of our sustainable roadmap, but not the end.
Johanne: For those who may not know, the Cradle-to-Cradle Products Innovation Institute certifies product innovations compliant with the circular economy, recognizing the efforts of brands that want to have a positive impact on people and the planet. Seeing our efforts recognized by this independent institute is such an honour. But as you said, this is the beginning and not the end. What else are we doing?
Bidisha: There are several initiatives we have launched recently. As you know, we are a multinational company with a presence all over the world. But we know we need to act locally to make a quick impact and take quick action. To this extent, in different geographies, we are piloting different sustainability initiatives for our different ranges and with different partner suppliers.
Let me start with Odace in France. Odace is one of the winning ranges of switches and sockets specially designed for the French market and produced in a net-zero factory in Spain. Just a quick mention of a figure we are proud of: Approximately one in three homes in France is equipped with Odace.
As our best-seller, Odace is also our prototype for more innovations. Hence, we introduced a new sub-range made out of 80% post-industrial waste. Every year, more than 54 million tonnes of waste is generated worldwide. So every time we choose “Odace Recyclé”, we’re taking action for a less polluted planet.
Johanne: Again, as we mentioned for the Merten product range, the material used for electrical components deserves special attention for its enhanced electrical safety. We have nothing but praise for the men and women engineers across our teams, as well as our suppliers, who help make all this possible. This speaks to their passion for enabling more sustainable living. Are there any other initiatives for which we had to meet special requirements?
Bidisha: Working with another partner, BASF, we’ve been able to introduce recycled plastics in our Resi9 product range. Resi9 is one of our electrical panel ranges that includes the breakers. As you can imagine, electrical safety is even more critical at the breaker level.
Why is it so critical? As you know, the breaker is your home’s line of defence against fire caused by short circuits and therefore needs to act fast under any conditions. The breaker automatically opens so the power is cut, meaning circuit breakers can be subjected to very high temperatures. That’s why the quality and density of the plastics used are very important.
Thanks to our engineers’ expertise and passion for sustainability in collaboration with our suppliers, we have been able to introduce new Resi9 Green breakers with 80% recycled plastics. This is another successful innovation that we will be able to roll out across different countries.
Johanne: You mentioned the packaging of our products as another example of Schneider’s commitment to sustainability.
Could you walk us through the Schneider initiatives to make our boxes more sustainable?
Bidisha: Of course. On top of all the initiatives we have already mentioned today, all our products now come in newly designed green packaging. For green packaging, we improved on two materials – cardboard and plastic.
Let’s start with the plastics. Put simply, we are gradually eliminating all single-use plastics.
As for the cardboard, we are changing all of it so we can:
- Use less cardboard first, and redesign it so we use only the minimum
- Use 70% recycled content
- Lastly, eliminate whitening chemicals wherever possible. The inks we use now are made from water and vegetable oil. And all of our cardboard consumes less virgin wood pulp, less water, and less energy. Again, it’s been a great collaboration with the packaging industry to make this happen. And we count on these partners to bring more volume online to make the transition faster.
Johanne: I want to add that this packaging initiative is not only for Schneider’s residential business. It spans the entire 200 million boxes that we ship out annually across our business units, and that makes a BIG difference.
As you can see, sustainability is not only our ambition at Schneider. It encompasses concrete actions that our engineers are driving every day for our planet. And that concludes this Innovation Talk. Thank you, Bidisha
Bidisha: Thank you, I hope our talk has conveyed the passion that we have for sustainability.
Listen to the complete talk here
Know more about what we can do together to achieve net zero homes
Add a comment