A safety instrumented system is often the last line of defense before a hazardous event occurs at a plant or operation. A safety instrumented system is composed of logic solvers, sensors, and final elements. These systems detect “out of control” process conditions that could lead to an unwanted incident, and then automatically return the process to a safe state. But it’s important to remember that safety instrumented systems (SIS) are different from process control systems.
Safety systems are applied across many industries. Emergency shutdown systems and fire and gas detection are among the most common applications. But there are other areas where a SIS can help protect workers and operations such as:
- Burner management
- Turbomachinery control and protection
- High integrity pressure protection
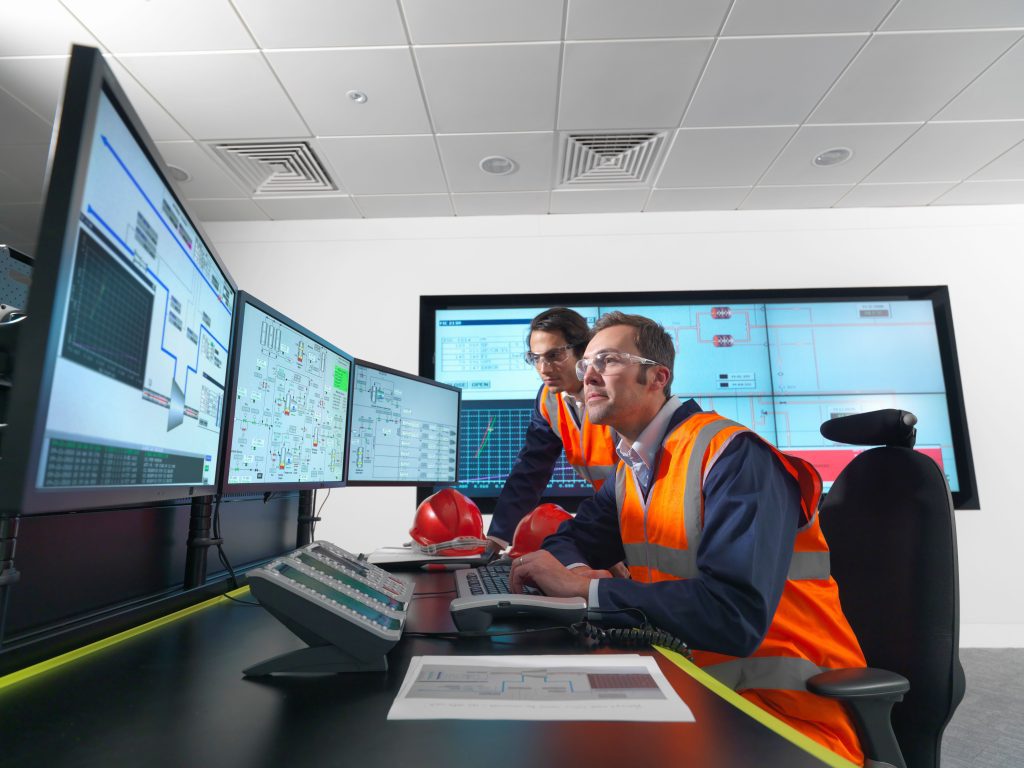
How does a safety instrumented system work?
Over the past 40 years, EcoStruxure Triconex Safety and Critical Control has become synonymous with safety and critical control. Our SIS uses a high availability, highly fault tolerant triple modular redundant (TMR) architecture. Through the decades, it has delivered over 1 billion safe operating hours without a known dangerous failure on demand. Incorporating a TÜV Rheinland-certified SIS into a plant will lower operational risk and help enable continuous safe operation.
A SIS considers the integrity of a safety loop (known as a safety instrumented function, or SIF), and consists of three major elements:
- Sensors – look for the initiating event that could lead to an event
- Logic solvers – decide how to deal with the hazard and then signal the final element(s)
- Final elements – return the process, or processes, to a safe state
Once a risk has been assessed, a SIS may implement one or more safety instrumented functions to address the specific hazardous event and help reduce the risk to an acceptable level.
Why do I need a safety instrumented system?
A safety instrumented system reduces the consequence of hazardous events to an acceptable level. This helps businesses reach their true potential by protecting their people, production, and the environment. For this to work properly, all EcoStruxure Triconex Safety Instrumented Systems follow IEC 61508 functional safety standards. This specific standard addresses functional safety in industrial process industries and covers the design, implementation, and management requirements for SIS from cradle to grave.
Meeting stringent international safety standards into EcoStruxure Triconex SIS is a must-have when it comes to best practices in process safety management.
What is a safety PLC?
A standard programmable logic controller (PLC) automates specific processes. When it comes to hazards or hazardous events, a standard PLC will not know there is a problem until it needs to take an action. Then the problem becomes self-evident. This is especially important for safety applications that often remain in the same operating state for long periods of time. Such applications only need to activate on demand if, or when, a hazardous situation arises (often referred to as “low demand”).
For example, an emergency shutdown system is usually normally energized, holds the outputs on for long periods of time, and will de-energize to trip and take the process to a safe state. If the system itself fails, then it will fail safe. So, a safety PLC operates with very specific and quantifiable failure modes. Essentially, a safety PLC is designed to work so that you can expect the equipment to work when it is needed to work.
A safety PLC is designed so that when a demand occurs, they do so with a level of certainty and within a specific probability that corresponds to safety integrity levels. This is achieved in a variety of ways, including incorporation of a high degree of internal diagnostics and automatic testing, hardware backup, and redundancy. As well as voting of independent signals within the PLC.
When it comes to the destiny and health of employees, plant operations, and the environment, it’s important to incorporate such safety instrumented systems – especially ones that are tested and verified by recognized certification bodies such as TÜV.
What is safety integrity level?
Safety integrity levels (SIL) define the tolerable failure rate of a specific safety function. The higher the SIL level, the lower the probability of a failure on demand. The SIL also defines that, in the event of a failure, to what extent can a process fail safely. Safety integrity levels range from 1 to 4, one being the lowest, 4 being the highest. These levels indicate the probability of failure on demand for a particular safety function.
A safety integrity level defines the amount of safety risk needed to mitigate a specific hazard. The level assignment is based on the amount of risk reduction that is necessary to reduce risk at an acceptable level.
EcoStruxure Triconex safety instrumented systems, like the safety PLCs and the Tricon CX “one versatile system,” have been certified by TÜV Rheinland to safety integrity level 3 so can be used for SIL 1, 2, and 3. This third-party verification uses international standards such as IEC 61508 and is put through rigorous test procedures.
Implementing a safety instrumented system in your operation
EcoStruxure Triconex safety instrumented systems bring superior uptime and high productivity to an operation. A SIS is an independent layer of protection that reduces the likelihood of an incident or event. That way, businesses can focus on driving efficiency and remaining competitive. Learn more about how our dedicated safety experts can assess, design, and implement trusted safety standards into your operations.
Add a comment