This audio was created using Microsoft Azure Speech Services
In a recent article, we discussed how new digitization at the medium voltage switchgear and circuit breaker level can help you increase operational efficiency and uptime. In this article, we’ll explore how this digitization can help you reduce electrical risks, such as exposure to arc flash incidents. Arc flashes are often the result of foreign material in live areas, such as dust and moisture buildup from hands and tools reaching into the area to perform electrical equipment inspections or maintenance. Other causes include an abrupt energy spike or an undiagnosed loose electrical connection. The National Fire Protection Association® (NFPA) estimates that five to 10 arc flash incidents occur every day, and nearly 2,000 people are exposed to the harmful effects each year.
One way to protect your facility workers and maintenance staff from arc flashes is to reduce their direct exposure to live areas. First, let’s look at how new digitized switchgear can help you minimize your employees’ risk. We’ll also look at how new electrical system designs are reducing electrical risks.
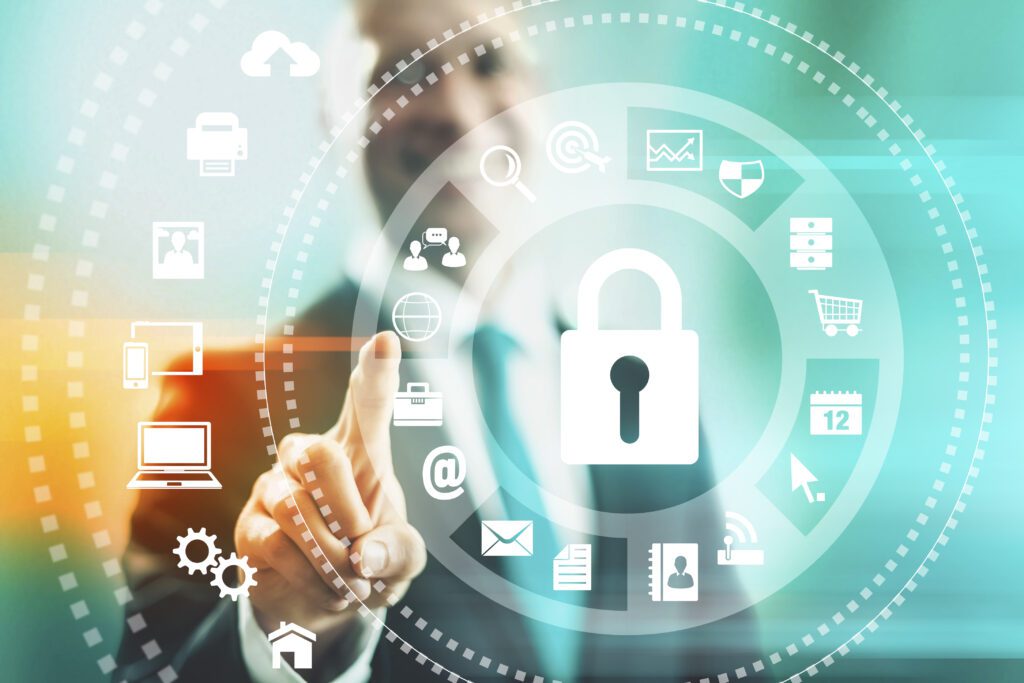
How switchgear digitization minimizes direct exposure to electrical equipment
With a digitized switchgear system, such as the new SureSeT™ medium voltage switchgear by Schneider Electric™, integrated with EvoPacT™ digital, medium-voltage circuit breakers, you can more easily access the status of your equipment components in real time. This allows you to switch to a condition-based maintenance process, potentially increasing the duration between maintenance cycles. This minimizes the need for your technicians to interact directly with the equipment, and reduces the likelihood of foreign material exposure to electrical components.
Reducing risks through remote control and monitoring
Additionally, embedded digital connectivity at the switchgear level allows local and remote control and monitoring. Connected products can be monitored within the facility but outside of the immediate arc flash zone. With remote monitoring, your technicians are less likely to be in front of the gear if an arc flash occurs.
Here’s how this works: EvoPacT’s digital sensors in the SureSeT switchgear system continuously monitor current, temperature, and vibration in components such as coils, motors, and vacuum interrupters. The sensors self-detect abnormal conditions, which trigger real-time alerts if you need to take immediate action to minimize electrical risks. This digitization also enables remote control, so your technicians can remotely open or close the breaker, as well as rack, in and out of the arc flash zone. This is an important benefit because arc flash incidents can occur when opening and closing the breaker. Digital connectivity enables remote operation without having to connect a remote operator switch.
These remote capabilities also include continuous thermal monitoring to help identify potential hot spots that are a primary cause of arc flash events.

How digital sensors enable continuous thermal monitoring
Before digital sensors were integrated into medium voltage switchgear systems, infrared thermography was often used for monitoring temperatures and identifying hotspots. While this type of thermal monitoring can help prevent conditions that can lead to an arc flash, it’s expensive and only provides a single moment-in-time view of the system. This traditional form of monitoring must be performed on energized equipment by qualified electrical workers who are required to wear bulky, personal protective equipment (PPE).
But SureSeT’s continuous thermal monitoring sensors provide a steady stream of data that can be accessed remotely on a smart device or in the cloud. With no direct contact needed, technicians can use the sensors at the switchgear level to eliminate a primary cause of arc flashes. This also increases overall system visibility.
For example, the thermal sensors continuously measure the cable side of the breaker and main bus bar. This type of monitoring is essential, as excessive heat may indicate increased resistance, poor contact, or excessive current flow. Any of these conditions can lead to equipment damage, electrical hazards, or even fire.

How new electrical systems designs are reducing risks
Digital integration at the medium voltage switchgear level is just one example of how new electrical system designs are helping to reduce electrical risks. SureSeT and EvoPacT are the latest examples of a 100-year history of Schneider designing electrical systems to reduce electrical hazards associated with facility equipment maintenance.
Now, with SureSeT and EvoPacT, you can add electrical distribution monitoring capabilities to further mitigate arc flash threats at your facility. With digital sensors integrated at the switchgear level, you can determine which components need maintenance before they pose a risk. Your technicians can remain at an appropriate working distance (outside of the arc flash zone) by using native wireless communications to operate equipment and gather data.
In addition to helping to protect your employees, this condition-based monitoring at the product level allows you to capture critical performance data, establish baselines, and identify long-term performance trends. This information can help you increase equipment longevity and reliability, reducing the likelihood of equipment failures that pose arc flash risks.
Visit the Schneider Electric website to learn more about how you can use EvoPacT and SureSeT to reduce your facility’s risk of arc flash events while improving operational efficiency.
Add a comment