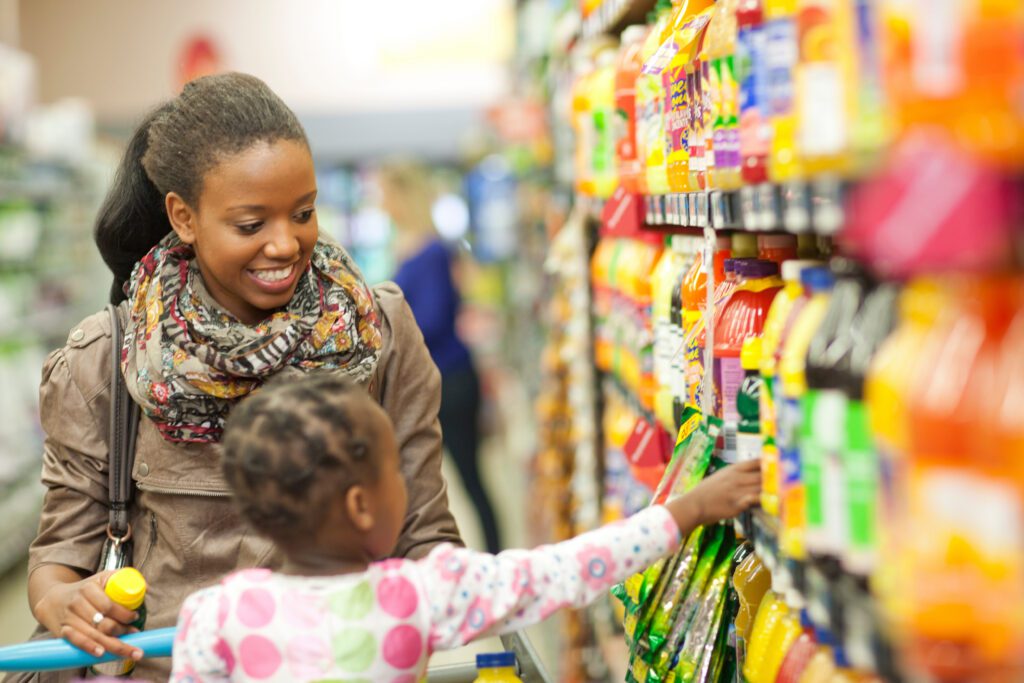
Recent research by Accenture calls for companies to see consumers through the context of their own lives, rather than as ‘walking wallets’. In our post-pandemic world customers’ lives are impacted by so many different factors and needs are changing fast. Influences such as climate change, war, inflation, and social justice awareness combine to drive changing and often paradoxical buying decisions. This places pressure on industrial companies to use more flexible production techniques which in turn drives the need for more agile machine builders.
The long-term trend for customization has already pushed companies to expand their product offerings and increase manufacturing flexibility, especially within the Consumer Packaged Goods industries. Agility is now more important than ever. Agility in products to meet rapidly changing customer demands, agility in the design and manufacturing processes to build them, and even agility in their business models.
How can machine builders help manufacturers bring the flexibility required to truly meet customer and market needs? There are two aspects to consider:
- A production line that allows for greater flexibility in the manufacturing process
- Machines that allow for faster time to market in the design phase
How multi-carrier systems can help increase agility and efficiency in the manufacturing process
One of the main differences between a multi-carrier system and a standard fixed-speed conveyor system is standard conveyor systems move products in one direction, at one speed only, while multicarrier systems can move the products independently, in different directions and speeds. The implications are multi-level. Check out this online demo to see a visual demonstration.
- Throughput is increased because product flow can be adjusted to take production operations with faster and slower cycle times into account. For example, if one operation takes longer to complete, other products can continue to move at their own pace.
- Instead of having separate, dedicated stations for different processes, they can be arranged to run simultaneously, regardless of how long it takes to complete each one. In some cases, this can save floor space and increase production efficiency, as various processes can occur at the same time, instead of one by one. You could call it multi-tasking!
These gains in manufacturing efficiency are possible because the material handling system is so closely linked to the overall process control system, allowing speeds to be dynamically changed to meet process needs in real-time, rather than staying at one speed no matter what. Another important advantage this brings is changeovers, which can happen with the click of a button, without downtime. This makes far smaller batch sizes possible, allowing manufacturers to respond to the market, increase their competitive advantage, and offer products that more closely match customer demand.
Add in the digital twin and you’ve got the possibility of virtually testing new product lines without stopping current processes. On top of this, industrial companies can change or update designs during operation in response to production requirements.
Machines can be designed and assembled faster with digital twin technology
Beyond the manufacturing process, digital twin technology is set to revolutionize the machine development process. Using what is essentially a virtual model of the machine, machine builders can test control logic and even digitally commission the system, with or without hardware. This significantly reduces design errors and streamlines the machine-building processes. It also allows machine builders to identify areas where efficiencies can be gained virtually, avoiding problems and downtime before they ever happen in the real world.
During the sales and design process, machine builders can use the digital twin to visually demonstrate the proposed machine to potential clients in 3D before it’s built. This helps set up realistic expectations and means that the sales simulation essentially becomes the first step in the design process. From a business development perspective, it potentially streamlines the sales and design process, reducing any miscommunication or errors along the way, and in turn, helping increase sales for the machine builder. Digital twin can also broaden business models by supporting remote condition monitoring as part of a long-term maintenance contract as the plant continues to operate.
All this allows machine builders to bring more flexible, advanced machines with optimal design specifications to market faster. This in turn allows manufacturers and businesses to innovate more quickly to meet the rapidly changing needs of their customers.
To learn more about how multi-carrier systems and digital twin work together to redefine machine design and manufacturing, access our free Frost & Sullivan whitepaper.
Want to hear from a machine builder who uses this solution? Watch our video.
Add a comment