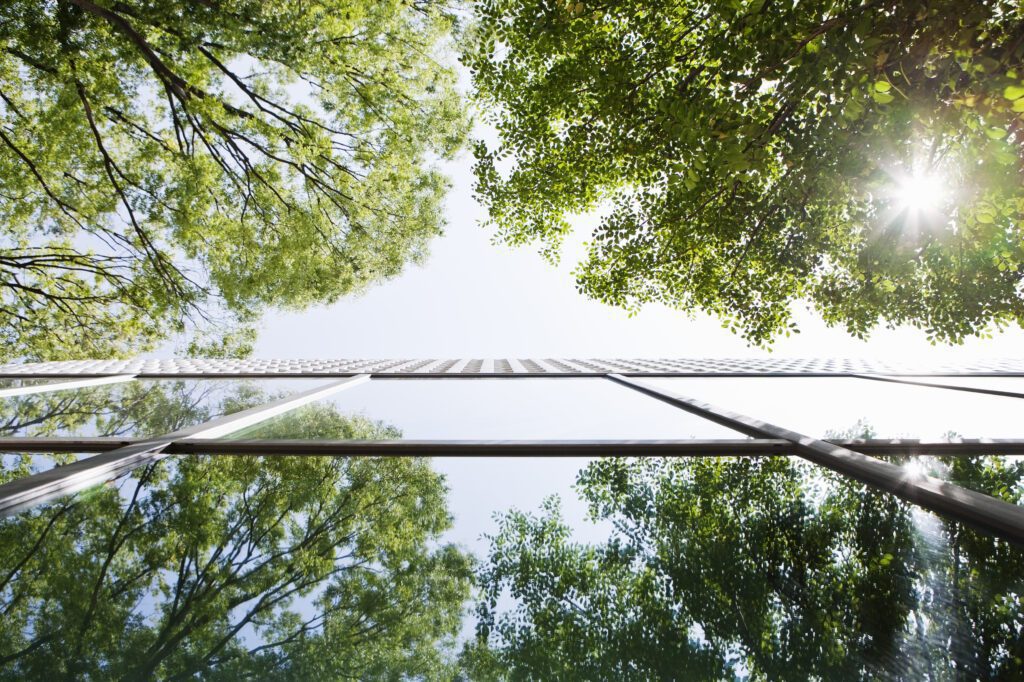
Our purpose is to empower all to make the most of our energy and resources, bridging progress and sustainability for all. At Schneider Electric we call this ‘Life Is On’. Furthermore, we say that electricity is the most efficient and best vector for decarbonization; and when combined with a circular economy approach and solutions, we will achieve a sustainable impact as part of the United Nations’ Sustainable Development goals. Our contributions to creating a sustainable glass industry start with our ‘Green Glass’ initiative, the one I am part of. When Dave Fordham from Glass Worldwide asked me if I would like to contribute an article, of course I said “yes”. We at Schneider Electric are highly motivated and fully engaged to help industries of the future achieve their decarbonization goals, today and tomorrow.
Our past
Let’s first look back to understand where the glass industry came from, starting with one of the biggest game changers ever: the regenerative furnace. The world’s first commercially successful regenerative furnace was built for a small glass-making company at Rotherham, South Yorkshire, in 1860.1 Since that day, the industry has dedicated a lot of R&D money and effort to keep on increasing the energy efficiency of fossil fuel-fired glass furnaces, and progress continued until the start of the third millennium. Further energy improvements have now almost come to a stop, which leads to the conclusion that the traditional regenerative furnaces are no longer improvable without the introduction of additional, mostly expensive add-ons such as batch preheaters or waste heat recovery systems. We still need to consider these but they will not provide the solution.
It is interesting to note that in 1859, almost at the same time, John Tyndall – Irish physicist, Fellow of the Royal Society, and a spectacular Victorian-era beard-with-no-mustache kind of guy – added detail to Fourier’s concept of the warming atmosphere. In particular, he found evidence showing that it was water vapor and carbon dioxide that trapped heat in the atmosphere.2
Our present
Today, the glass industry has come to a point in time in which, instead of using fossil fuels, it has started to consider alternative, renewable heat sources to run energy-intensive melting, fining, and conditioning processes. One goal is a reduced carbon footprint in order to maintain a social license to operate. The obvious choices seem to be electrical energy or the use of hydrogen. Both have pros and cons, and they share availability, cost price, and infrastructure problems. Many initiatives are investigating the use of both, separately and together in hybrid solutions, which is good. The glass industry needs to know its options. But knowing that electrical energy for direct heating is far more energy-efficient than producing and then burning hydrogen, and greatly reduces NOx and SOx emissions, it’s already safe to say that electrical energy will play a major role in future glass manufacturing.
Our electric future
For float and container manufacturing, we must look at the amount of installed power; for the furnace alone this will reach from 12MW up to 50MW. When the focus shifts from combustion systems towards electrical boosting installations, not only will furnace designs start to look different but electrical utility systems around the furnaces will also change.
With hybrid furnaces, we even would need to consider both combustion and electrical heating systems. Perhaps even consider on-site electrolysis which will put another burden on the amount of installed power required. Systems will move from low and medium voltage up to high voltage equipment, and ensuring those systems are as energy efficient as possible is an absolute must. More space will be required and figuring out how and where to position those systems will be unavoidable.
It ultimately changes the energy mix of glass sites: electricity being a major power; a significant portion being fully reliable; and all electric supply being produced from sustainable sources.
How can Schneider Electric contribute?
In most cases, however, we need to answer the question of how to get the required electrical power into the plant first. Will the grid accommodate it? What will it cost and how will the price per MWh develop? In most regions, this alone will be a challenge. Our Energy and Sustainability Services team possesses the knowledge to assist you in overcoming those problems.
The requirement for more electrical boosting power will also lead to more and bigger electrodes running higher currents. Size and number of electrodes are limited but nevertheless, power control systems will need to move up in current and input voltage. To keep capital spending and operational costs down and evaluate the space required, Schneider Electric uses sophisticated systems design tools; systems, transformers, and power control will change and we are finding clever ways of controlling those systems at the same time.
Safety and maintenance of electrodes will become increasingly important. The way we look at electrical furnace boosting is changing dramatically, and we also have our analytics and AI teams, together with our partners, focusing on these complex problems as well.
Once the furnace is in operation and becomes part of the value chain, we must make sure it is also as energy-flexible as possible to accommodate the utilities to get us the best electrical power tariffs in return. Schneider Electric Green Glass together with our partner CelSian are working on tying modeling, control, and EcoStruxure Microgrid Advisor together to get the most out of furnace designs.
Schneider envisions a process transformation and a complete plant design in which Power & Process are closely integrated from the early design phase to long-term operations and energy management.
Conclusion
Considering the power requirements for hybrid furnaces and fully-electrical boosting is key to preparing for the evolving energy mix that is necessary to achieving decarbonization goals.
Although the glass community is facing extremely complex problems, these are exciting times in which the industry will come back on top and will find new technologies having an impact similar to what the regenerative furnace had 160 years ago. Let’s do what we need to do together!
In the spirit of John Tyndall: “Experimental facts alone cannot satisfy the mind: we desire to know the cause of the fact; we search after the principle by the operation of which the phenomena are produced.”
Find out more about Schneider Green Glass solutions on this handout.
This article was previously published in Glass Worldwide (pages 76-77).
To learn more about green glass, watch this video on Greening the Glass Industry: