Manufacturing firms across the globe are increasingly being asked to demonstrate progress toward concrete sustainability and related circularity goals to maintain customer loyalty and investor confidence. Therefore, it should be no surprise that 90% of Fortune 500 companies now publish sustainability reports, with 20% formally committing to carbon neutrality. These days, the definition of sustainability is broadening. In addition to embracing renewable energy and reducing energy consumption, sustainable operations also involve the reduction of material waste through circular manufacturing.
In addition, the notion of “repairable” assets is also gaining traction. Repairable manufacturing implies investing in assets that can be easily repaired or refurbished at “end-of-life” rather than ripped out and replaced.
But achieving goals like carbon reduction, circularity, and repairability can be challenging, particularly in the manufacturing sector. For decades essential issues such as high energy consumption, growing levels of industrial waste, and the minimization of carbon emissions have been placed on the back burner.
Now, sustainability has emerged as a multi-dimensional issue, encompassing the reduction of CO2 emissions and the notion of much more aggressive resource conservation. As a result, migration to decarbonized, low-waste operations is a top business priority – but organizations must be adequately equipped to implement the necessary structural and process changes without significantly disrupting their production facilities.
A recent MIT Technology Review Insights paper illustrates how large global manufacturers such as Castrip, Doosan Bobcat, Renault Trucks, Nestlé, Johnson & Johnson, and Schneider Electric are some of the companies finding innovative and cost-saving ways to address sustainability challenges. In addition, the report highlights some of the best practices these organizations have implemented to achieve reduced emissions and circularity success.
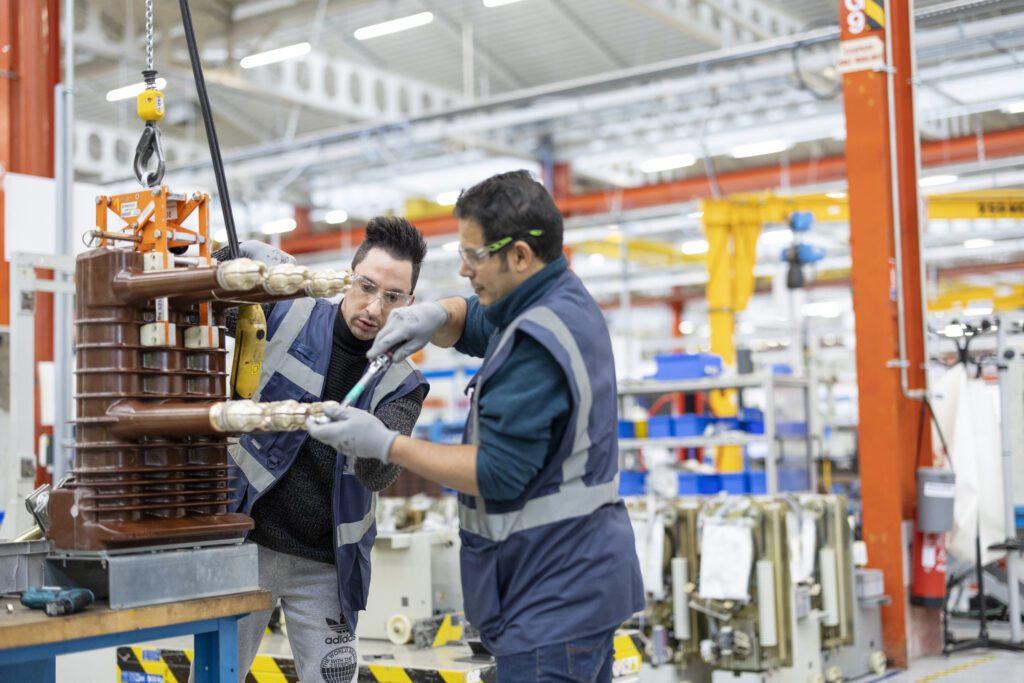
Repairable and circular manufacturing report findings
The leading manufacturers interviewed for the report deployed a variety of approaches to bolster the sustainability of their operations. These included:
- Diversification of energy sources away from fossil-fuel-based electricity
- Development of microgrids to produce their own green power
- Improvements in the efficiency of equipment maintenance and process optimization through improved data analytics and Internet of Things (IoT)-based sensors
- Modernization of production lines to reduce raw material consumption and increase existing machine performance
For example, steel processor Castrip has reported drastic reductions in CO2 emissions when they convert liquid steel into thin metal strips for industrial, automotive, and construction applications. Their unique processes reduce emissions by 80% to 85% compared to traditional methods using a “cold-rolled” process.
MIT Technology Review Insights reporters observed that visibility through data analytics and digitally connected supply chains were critical to overcoming traditional sustainable manufacturing hurdles. On the maintenance side, it was revealed that using software-based monitoring and management technologies, combined with sensors, helps assess equipment performance and proactively predict optimum repair and refurbishment cycles.
Such condition-based maintenance extends the lifespan of manufacturing assets and reduces failure and downtime. This drives greater operational and electrical efficiency while optimizing material usage and decreasing carbon footprint.
The Johnson & Johnson consumer goods business, another MIT Technology Review Insights subject, used sensors to help manage solar panels and implement wastewater reduction. As a result, stakeholders slashed average energy costs in their modernized production line by 20% to 25%. Deployment of such technologies represents the first step in the circular economy journey.
The long-term goal of manufacturers working toward carbon neutrality requires achieving two shared goals: increasing the visibility of the carbon content across a firm’s entire supply chain and reorienting their business model based on circular economy principles. Measuring and management are also key strategies for maximizing the lifespan of products and equipment used in operations.
Schneider Electric’s value add: EcoFit circularity and repairability services
Companies like Schneider Electric support manufacturers committed to enforcing circularity, repairability, and decarbonization best practices through multiple service offerings. These include:
- Retrofit services: Circularity-focused EcoFit service centers design pre-engineered retrofit solutions that adapt modern digital components to existing end-user installations. In many cases, the in-field installation of these components can be implemented in less than two hours without requiring a complete installation shutdown. This minimizes the impact of ongoing operations. In addition, the ability of these retrofit solutions to connect and communicate adds more business value since the equipment can now be monitored in real time.
- Refurbishment services: Rather than “rip and replace” systems running for 20-30 years, essential infrastructure products can now be affordably refurbished at the manufacturer’s quality standards to meet current marketplace performance standards. Energy infrastructure like switchgear, for example, can be taken back and provided with a second life. This minimizes waste and maximizes efficiency. In addition, these older units are configured with sensors, which allow users to take advantage of predictive maintenance service plans and enable 24/7 remote monitoring.
- Repair services: When components are built to be easy to repair instead of easy to throw away, raw materials are conserved and experience an extended useful life. Historically, without spare parts readily available, industrial equipment requiring simple repairs has been replaced by expensive new equipment. Such an approach results in unnecessary material waste and higher costs. Repair solutions that embrace innovative spare parts strategies offer a much more affordable alternative for companies while contributing to circularity.
- Recycling services – If a holder of electrical equipment, such as switchgear, containing SF6 gas does not properly dispose of it, that organization will be liable to fines and legal proceedings. SF6 is a greenhouse gas with an atmospheric life span of 3,200 years, and with 23,500 times more impact on global warming than CO2. Turn-key services, that process obsolete electrical equipment and closed-process SF6 recycling and/or safe disposal are now available. These services help organizations comply with regulatory standards and achieve greater sustainability.
Together these circularity services are embedded into Schneider Electric’s EcoFit approach. This total value proposal is applied across the life cycle of Schneider Electric products and aims to eliminate waste by up to 90%. Our goal is to help manufacturers make the most out of their existing assets so that we can collectively reduce our impact on resources, materials, and carbon emissions-driven climate change.
For more information To learn more, visit our EcoFit web page or download the MIT Technology Review Insights paper “Equipment management and sustainability.”
Add a comment