A summer internship that became something bigger
I started my career at Schneider Electric with a summer internship in the end of the 90’s before I was officially employed in 2001. Gradually I worked my way up in the logistics world through various positions until I became Operations Manager in 2015. At that time, I was given control of both the Central Eastern European Regional Logistics Centre and the local adaptation centre. The next milestone was the year of 2020, when I was appointed as Customer Satisfaction and Quality Manager.
On an average working day my tasks can be divided into two parts. I deal with quality related tasks and issues that arise in the day-to-day operations. We are responsible for the stock in the logistics centre so if any factory has a stock blocking request or claims (surplus, missing, damages etc.) we must react immediately, and coordinating these processes is also my responsibility. The second main part is managing longer term projects like customer visits or reporting activities.

Why sustainable supply chain?
The supply chain is like a stream that flows through organizations all around the world. The logistics centre is one of the last stakeholders that works on the products before they are delivered to the customers. You could say that we put the cherry on top which is a huge responsibility but an opportunity as well. Being on this side of logistics allows us to meet all the actors of the supply chain.
We have the chance to network and learn from others.
I recommend this area to those who want:
- to get to know the different actors of the market,
- to understand their needs,
- to deal with complex tasks and challenges while being able to notice how rapidly supply chain is evolving through digitalization and technological innovations.
Sustainability runs through the veins of logistics
If we approach Schneider Electric’s sustainability efforts from a quality perspective, one of the most important parts is packaging. The company strives to reduce the use of film in packaging as much as possible. We have eliminated a large percentage of these materials. This is also beneficial for customers since they don’t have to deal with the unnecessary wastes. In addition, the quality of packaging is also an essential point. If the quality of packaging is poor, products have to be recalled or scrapped which means more transport and an increase in emissions. Therefore, Schneider Electric aims to use high quality packaging materials that protect products throughout our sustainable supply chain.
Our innovation hubs present different sustainable technologies to customers. Energy efficiency defines our work across the company and the same applies in logistics. To illustrate, we can talk about the system EcoStruxure that provides a lot of solutions to help us use energy more efficiently. For instance, our logistics centre has a smart LED lighting system that intelligently regulates itself by detecting the movement of workers in the hall and senses the external light intensity. The resources freed up thanks to technology can be invested in further developments.
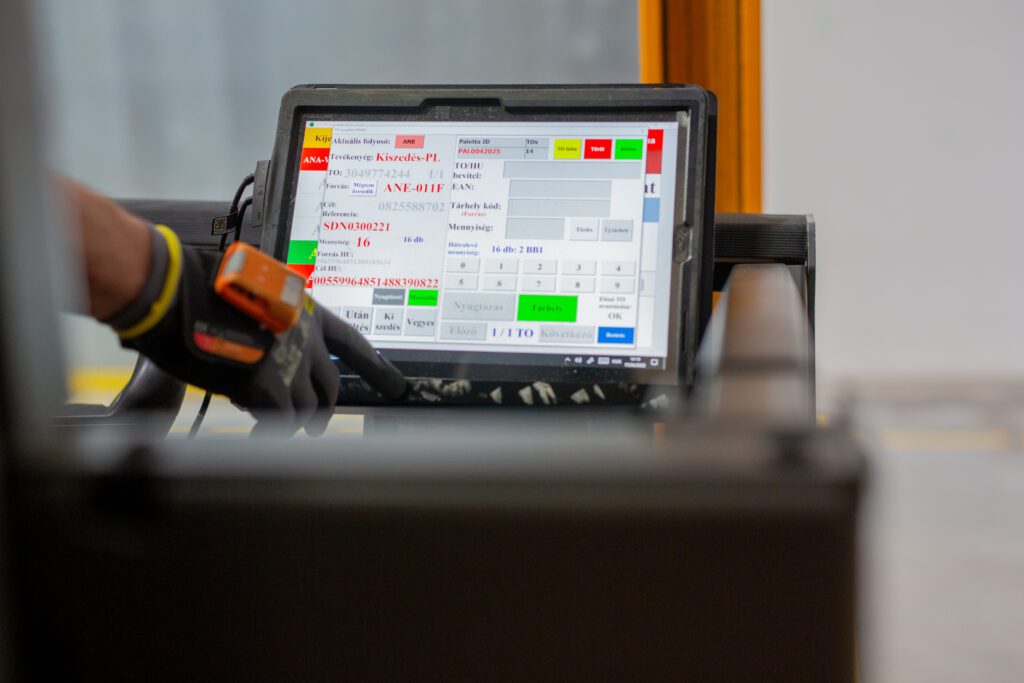
“Schneider Electric is constantly creating opportunities”
I’m proud to work for a company that supports our professions, our careers, and our learning developments.
I have been able to participate in several interesting and impactful projects in recent years.
For example, we built a time registration system for the automatic digital monitoring of work processes and for the monthly payroll of the entire logistics area. This real-time automated queue management tool visually maps the tasks of each area, for a more efficient and transparent work organization.
I can also mention Schneider Electric’s medium-voltage circuit breaker called RM6 which is also a great sustainability success story. For this high-value product, we designed a special cardboard packaging that is plastic-free, it’s easy to place and it protects the product from damage during transport. Since using this packaging, we have seen a big drop in customer claims.
We were able to do these things because Schneider Electric is constantly creating opportunities. Opportunities to learn and grow and to broaden your horizons.
In the following years, I would like to stay close to our customers, and explore more digital solutions created and promoted by the company.
And one thing I know for sure: it will be right by Schneider Electric side.
Are you interested in a career at Schneider Electric like Péter? Check out our website for more information and for available positions to take your career journey to the next level. www.se.com/careers
About the Author
Péter Berényi is customer satisfaction and quality assurance manager in Szigetszentmiklós (Hungary). In recent years, he has managed various teams in logistics. Processes, customer satisfaction and reliability are also some of the areas he has expertise in.
His objective is to develop processes that ensure we protect and enhance quality assurance at Schneider Electric.
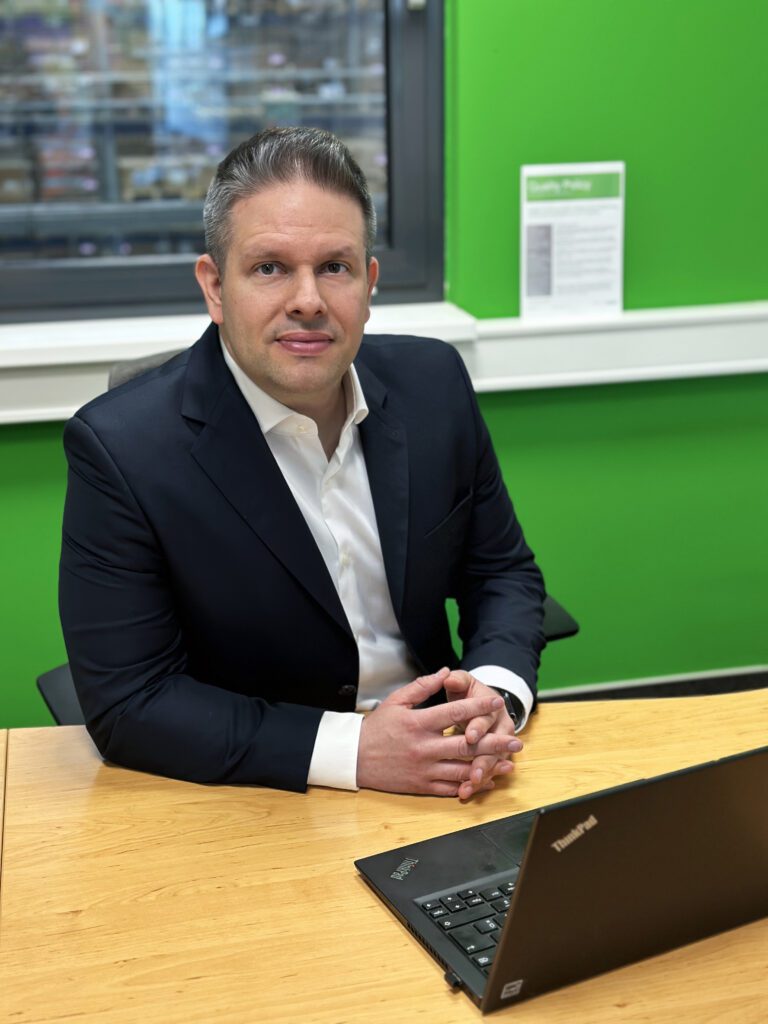
Add a comment