This audio was created using Microsoft Azure Speech Services
In today’s industrial landscape, facility managers juggle many challenges: uptime needs, spiraling energy costs, changing workforce demographics, and the urgent call for sustainable practices. Energy efficiency offers real solutions, but misconceptions often cloud the journey to value. This article dispels myths and highlights often-overlooked benefits for industrial operations.
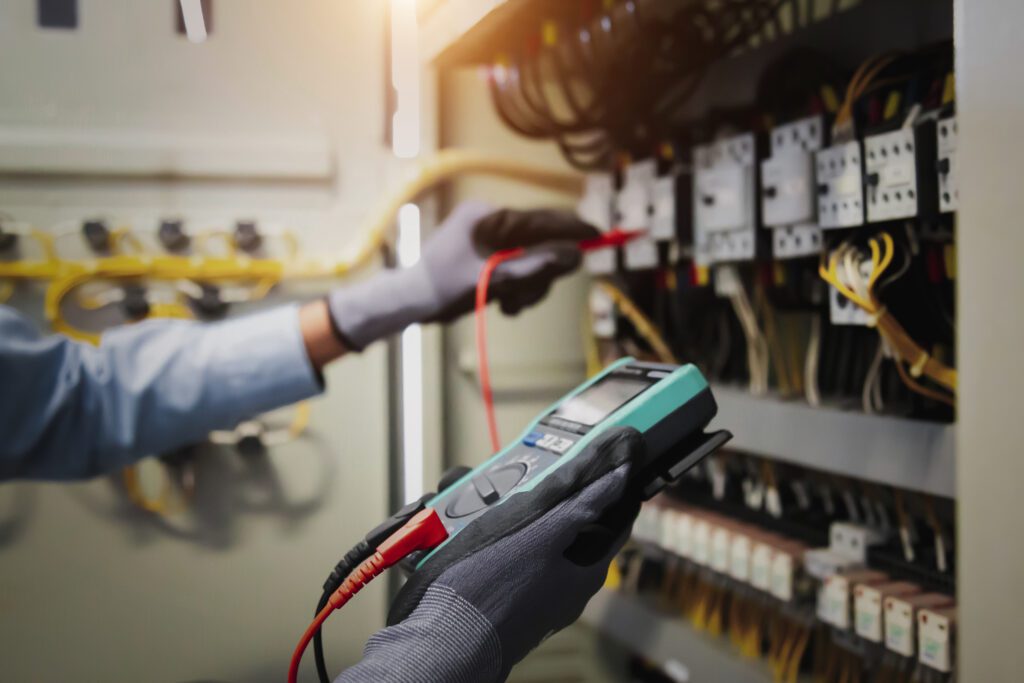
The Root Beer Analogy
Many people think energy efficiency means using less energy. That’s a worthy goal but only one of several possible benefits. The real objective of energy efficiency is to maximize the value of the energy you consume.
I like to use the analogy of a mug of root beer. Imagine you order a frosty one down at your local burger joint. Regardless of the size of the mug, you would probably be disappointed if it was fifty percent foam.
Now think of the mug’s capacity as the total energy consumed by your facility. The root beer is usable energy, and the foam is wasted energy. Everyone expects a little foam in their root beer, but nobody wants to pay extra for it. The same applies to wasted energy.
Energy efficiency aims to make the most of what you buy. Whether or not it reduces total consumption, it can save money, preserve your equipment, reduce downtime, and help you continually improve your operations.
Making the Connection Between Power Quality and Energy Efficiency
When seen in this broader sense, energy efficiency and power quality are inherently linked. Quality is more than availability. Just because the lights are on doesn’t mean you’ve got high-quality power.
To start with, the quality of power coming from the grid can vary significantly over time and location. Here, high quality equates to a consistent, clean, and reliable energy supply, which allows machinery to function optimally, enhancing the value of the energy you pay for.
Power quality can also be affected by the facility itself. Machinery and other electrical equipment can introduce disturbances into the power supply, known as “dirty power,” leading to unstable performance. Additionally, sending dirty power back to the grid typically results in fines called power-factor penalties.
Power disturbances can interfere with logic signals, triggering software glitches. Difficult-to-detect disruptions erode semiconductors, resulting in thermal runaway. These conditions can result in considerable expenses, including replacement parts, additional maintenance, and, most notably, operational downtime. A poor-quality power environment often causes nuisance breaker trips and equipment shutdowns – resulting in production disruptions, lost product, and safety issues.
The ROI of Energy Efficiency
Industrial companies often view energy efficiency measures as additional costs. However, in many cases, reductions in power-factor penalties alone quickly pay for the investment in power monitoring and quality remediation.
If you are experiencing downtime for unknown reasons, analyzing power quality can deliver even faster ROI. For example, we worked with a manufacturer plagued by frequent breaker trips and costly downtime. Using a portable metering system, we discovered significant power quality issues. That analysis helped clue us into the right solution. And, installing capacitor banks and other power factor correction solutions reduced their utility bill by over 30 percent and eliminated nuisance trips.
Beyond immediate savings, energy efficiency initiatives using modern digital tools enable you to understand and manage your power distribution system more effectively over the long term. With the insight you gain, you can prevent unexpected disruptions, prolong equipment life, and ensure uptime.
The High Cost of Doing Nothing
It’s important to understand the financial implications of energy efficiency projects to ensure value for your investment. Every project and every facility is different, so it pays to have an analysis conducted by an experienced partner with the technology and expertise to accurately diagnose issues and predict the outcome of any actions you might take.
One thing to consider is whether you are building a new facility (greenfield) or looking to retrofit an existing one (brownfield). Because greenfield projects can integrate power monitoring and energy efficiency into the design from the beginning, the cost is typically one-tenth that of brownfield projects.
However, don’t write off the retrofit scenario. That investment can still deliver significant energy savings and operational enhancements. In our experience, the cost of downtime due to system failures could be as much as ten times that of a brownfield retrofit. In other words, while retrofitting is certainly more expensive than integrating energy efficiency in new construction, the financial downside of disruption far outstrips both.
The Power of Co-Investment
Facility managers often lack the time, budget, or expertise to track down complex power quality issues that lead to inefficiency and high costs. And, the retirement of older workers and the tight market for technical skills mean that fewer industrial companies have dedicated energy management and electrical distribution professionals on staff.
Bringing in an outside consultant is often the best choice. They can thoroughly audit the facility, identifying opportunities to improve power quality, energy efficiency, and cost-effectiveness. Increasingly, leaders in the power management industry are offering a co-investment model. When they identify clear opportunities for improving efficiency, they subsidize equipment costs to share the resulting savings. This makes it easy for clients to get the benefits of clean, efficient power with less upfront investment.
The Future of Energy Efficiency
As we look ahead, the importance of energy efficiency will only grow. Technological advancements promise to make energy efficiency measures more accessible and cost-effective. Smart grids, Internet of Things (IoT) devices, machine learning algorithms for energy management, and other emerging technologies will help organizations optimize their energy usage like never before.
For most industrial companies, energy efficiency is a cost-effective way to gain significant operational and financial benefits. It’s not just another “nice to have” option – instead it is increasingly essential in a world of escalating energy costs and growing environmental concerns. By investing in energy efficiency, organizations can improve their bottom line, reduce their environmental impact, and build a sustainable future.
Learn more about how Schneider Electric can help you improve your power quality.
Add a comment