This audio was created using Microsoft Azure Speech Services
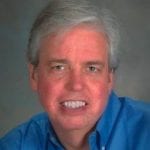
We are pleased to host Greg Hale, chief editor of ISSSource, as our guest blogger in the Oil & Gas section as he shares the outcome of interviewing several Schneider Electric experts on the topic of safety and reliability:
Author’s remarks…When one major oil and gas company talked about automated testing on their boilers, they reduced startup time by 85 percent and gained four extra days of production, which meant they were able to add $60 million in revenue they never would have seen if they did things the “traditional” way.
By eschewing the old ways, while keeping safety in mind, another O&G major saved over 200 man days on their factory acceptance test.
Yes, safety systems keep plants up and running and, well, safe, but there can be so much more, like using safety to enable a more profitable manufacturing process.
“Safety, good business, good practice, and reducing downtime, directly links to profitability,” said Steve Elliott, Senior Director at Schneider Electric.
Just look at increases in productivity because of less downtime, less business interruption, reduction in production costs, reduction in maintenance costs because you are designing and operating the appropriate amount of safety, not over engineered and under engineered, but the appropriate amount.
Safety has always been done one way and that is the way it will always be done. But that way of thinking is changing.
the following addresses …..
Mindset Changing on Safety and Profitability
Safety systems continue working silently in the background, chugging along keeping a constant vigil over manufacturing operations to ensure everyone goes home safely at the end of the day.
That is safety 101 and something everyone in the manufacturing sector works toward daily. However, when it comes to safety, there can be so much more, like using safety to enable a more profitable manufacturing process.
“The most important thing for senior management is safety gives them business sustainability,” said Sven Grone, Safety Services Practice Lead Asia Pacific & Middle East for Schneider Electric. “It gives them the ability to get licenses to operate in places they couldn’t if they had a poor safety record. It gives them the ability to make business decisions to deliver better shareholder value. There are soft and hard benefits. Some of the soft benefits are image, reputation, brand, and business flexibility. If you don’t have incidents, you are producing and are more profitable and you can satisfy your customers.
“Then there are increases in productivity because of less downtime, less business interruption, reduction in production costs, reduction in maintenance costs because you are designing and operating the appropriate amount of safety, not over engineered and under engineered, but the appropriate amount.”
What is at odds today is people do not associate safety and profitability in same sentence. Safety has always been done one way and that is the way it will always be done. But that way of thinking is changing.
“Safety, good business, good practice, and reducing downtime, directly links to profitability,” said Steve Elliott, Senior Director at Schneider Electric. “I think we can slowly change the minds. I think the minds of the more mature companies are changing. I was once talking about profitable safety and I got a message from one older worker saying we should never talk of profitability and safety in the same sentence. His reaction was almost immediate. It was a mindset.”
New Age Intelligence
Today’s way of thinking needs to go beyond the conventional and move into the more digital and connected world.
“It is not limited anymore to keeping systems up and running,” said Yusuf Kapadia, Principal Technical Safety Consultant, Safety Systems Portfolio at Schneider Electric. “It is about when the system is running, how well is it running. If you are running within a certain operating window, you will have a longer lifecycle. If you have an operating window exceedance, you have a non-safe scenario. This is how serious the industry is today in checking safety performance. We have an organization here in the Middle East, who treat an operating window exceedance like a near miss scenario. For example, let’s say you have a specific pressure in a pipe where the pressure operating window is 45-55. If the pressure moves above 55, it will not create a trip because the high-pressure trip point is set at 75, but if the pressure changes from 55 to 65, it still creates a stress in the pipe. This, in the long term, could create a pipe that explodes or a pipe that requires a replacement.”
Taking a different approach is exactly where profitability comes into play.
“As soon as you start talking about how you start reducing Capex (capital expenditure) and Opex (operating expenditure), all of sudden safety isn’t just a cost anymore,” said Michael Chmilewski, Vice President Process Safety Business at Schneider Electric. “Now you are showing them you’re reducing their costs, which then naturally gives a boost to their profitability. If we help them take away one percent of the cost, that is one percent to the bottom line. If you save them two percent, that is two percent to the bottom line.”
Case in Point
Using more automated and digital technologies, proved to be a profitable and safe testing process for two major oil and gas players.
“When one major oil and gas company talked about automated testing on their boilers, they ultimately gained four extra days of production they wouldn’t have had otherwise,” Elliott said. “They estimated a savings of about 50 percent of their factory acceptance testing man hours and reduced their start up time by 85 percent – without compromising on quality. It is a 330,000 barrel a day refinery, that is over 1.2 million barrels over four days. If you take 1.2 million x $50 per barrel that is $60 million in revenue they received by having the plant running four days before they expected.
“Another organization in Singapore said they saved over 200 man days on their FAT (factory acceptance test). Using tools and technology in the right way improved productivity, enhanced performance and created unexpected profit.
“The breakthrough here was in the minds of the people,” Elliott said. “The mindset was we can’t do this using the traditional way, we have got to find a different way. They could have said ‘No, it can’t be done.’ They were forced into finding a different way.”
The oil and gas industry is in the process of going through modernization projects and they are looking at how they can make safety more profitable.
“There are people looking at engineering processes that want to have the consistency of safety, but they want more profitability,” Kapadia said. “They want less equipment, less redundancy, less SIL ratings required. If we look at HIPPS (High Integrated Pressure Protection Systems), which is the last line of defense for a pipeline system, HIPPS before was always a SIL 4-rated system. Today, you see HIPPS more like a SIL 3 rated system. If you look at the oil industry; when oil moved from $100 down to $50, we can see decisions from oil and gas companies change, as they were relooking at all their engineering processes. The idea was not to miss any safety aspects, look at how they were doing things and improve profitability while still being safe.”
Insurance Factor
Another way to add to the bottom line is to prove to insurers the operation is running safely with a very low probability of a process safety incident.
“Insurance companies today are recognizing there are best practices and recognized standards out there for doing safety correctly, so if you can show the insurers you are managing your safety in accordance with best practices, you can potentially reduce your premiums,” Grone said.
“If you can show you invested in making your assets safe, you are protecting people, have systems and measures in place and are constantly monitoring their performance,” Elliott said, “you can prove to the insurer that you have done a good job and will be able to offset this with your insurance premiums.”
Meeting safety compliance is one thing, but to achieve a more profitable manufacturing environment there needs to be much more.
“Safety is about a long term sustainable performance and that includes profitability,” Elliott said. “Today’s technologies should be helping those safety professionals at the site to clarify decisions so they understand the ramifications of their actions on safety outcomes, safety and profitability are not achieved by just complying to the letter of the law.”
To learn more…download your FREE white paper: Profitable Safety – Improving Real Time Operational Safety to Jumpstart the Profit Engine here
Conversation
Amos Notea
6 years ago
In your document: “Profitable Safety – Improving Real Time Operational Safety to Jumpstart the Profit Engine” by Peter Martin & Steve Elliott
A patent is mentioned:
“Schneider Electric has developed a
patented approach called Dynamic Performance Measures to model the measurements of these variables from process sensor data in real time”.
Is it possible to get a description of your approach?
With Thanks,
Prof. Amos Notea