This audio was created using Microsoft Azure Speech Services
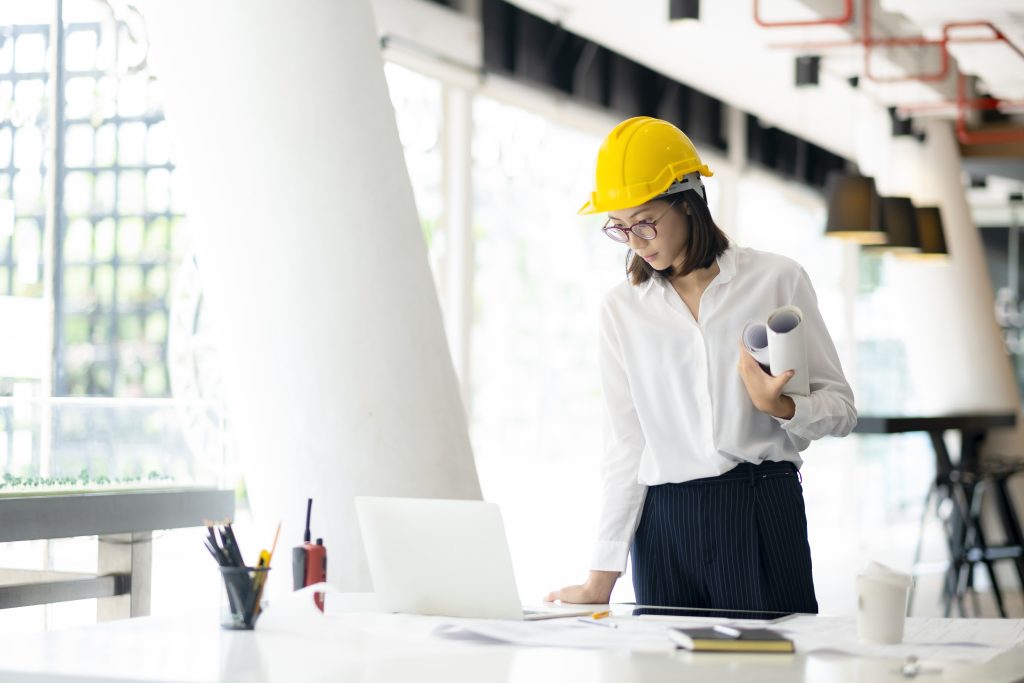
Life science companies carry a lot of responsibilities around the world. After all, they provide products and medicines crucial to the health and welfare of the global population, but they also face significant challenges due to today’s volatile conditions:
- A shift towards a green economy, with increasing regulations on energy usage and carbon emissions
- A need to decarbonize operations to support market competitiveness and appeal to investors
- Fewer experienced employees
- Staff who prefer companies with clear sustainability goals
- Consumers who are now factoring in environmental and social impacts into their purchasing decisions
While other industries face similar issues, they can avoid the stringent regulatory environment that pharmaceutical and other life sciences companies can’t.
Life sciences companies must embrace sustainability as a core element of their business, incorporating it into the design and development of new products and facilities to enhance long-term efficiency and effectiveness.
Traditionally, industrial facilities are designed to keep initial costs down, focusing more on CapEx than OpEx. This approach overlooks efficiency opportunities, as retrofitting is expensive and impacts productivity once the facility is operational.
Life sciences companies must focus on three main objectives to embrace sustainable facilities and maximize their business value.
1.Design for efficiency
Designing for efficiency requires a proactive approach. Integrating sustainability and efficiency initiatives early in the facility design phase allows for fundamental efficiency considerations, such as utilities’ generation, distribution, consumption, and building orientation.
Orienting a building to take advantage of sun exposure means it can capture and use environmental heat. Using cooler areas for passive cooling can significantly improve the building’s underlying efficiency. Further boosting efficiency by locating processes together to consume waste heat or by-products from one production line to power or cool another can also help.
The use of low-grade energy can help reduce OpEx and minimize utility capacity. However, to be practical, these considerations must be an integral mandatory part of the design requirement from the beginning and are vital in reducing the carbon burden. Changing once the project is underway becomes complex and expensive.
2. Include digitalization
To truly address decarbonization and long-term sustainability, system designs must include digitalization. Conventional systems can be time-consuming and lack the details to effectively manage the operational efficiency required to meet and adapt to today’s fast-changing environment. Including smart sensors and devices across systems designed for key points within manufacturing facilities enables data to be automatically collected and easily accessible across operations, eliminating manual collection and reducing human error.
The real-time system insights enabled by digitalization allow for much more precise process management, driving manufacturing based on additional sustainability KPIs, optimized energy mix, carbon emissions, environmental impact, and potentially net carbon zero. This digital sustainability at the heart approach also proactively mitigates critical asset failure risks, enhances processes for consistent product quality, and improves overall line performance, compliance, and reliability.
Digitalized systems can also include valuable tools to empower staff decision-making. Digital shadows or full digital twins of equipment, unit operations, or entire facilities allow staff to test possible courses of action to ensure they choose the best option.
3. Consider modularity and decentralized infrastructure
Traditional models typically rely on centralized infrastructure. However, a decentralized design for utility systems like steam, compressed air, and chilling capability can provide key sustainability benefits. Modularity also makes expanding, supplementing, identifying, and isolating problems easier. This, in turn, makes overall system management and individual employees’ jobs easier.
For example, rather than using one giant steam boiler, several smaller steam generators near their serving processes may be more efficient and save site-wide distribution losses. This decentralized approach helps reduce the operational cost of steam generation and optimizes uptime since an issue will only affect one line rather than the entire plant.
Similar win-win-win opportunities exist for other utility systems. An electrical system can include backup systems that target specific critical equipment rather than the entire plant or process line. This can reduce costs while meeting or exceeding the critical goal of minimizing outages.
A competent approach to designing sustainable life sciences facilities should include some key elements:
- A digital platform that can provide data and insight across the entire enterprise, including process and infrastructure operations (not just utilities). This system aggregates information from multiple sources into a single “pane of glass” for enhanced enterprise visualization. It provides connected process metrics, maintenance analytics, engineering documentation, financial performance, and other data required for real-time sustainable operational performance management.
- Utilities management systems, including water and waste management, gas, steam, and electrical systems.
- A carefully selected choice of products and equipment to minimize environmental impact – including the embodied carbon in each product or component of the project.
- A detailed corporate energy strategy and the energy management solutions needed to implement it, including backup power and renewable energy options.
Designing for sustainability offers some major benefits:
- Minimizes carbon emissions and improves carbon reporting for Scopes 1, 2 & 3
- Reduces energy usage and costs, including water conservation
- Maximizes reliability and operational productivity
- Provides a strong brand value by demonstrating green values and environmental awareness
If your company is looking to embrace sustainable design, we can help. Schneider Electric has extensive experience with sustainable design, beginning with our own manufacturing facilities. The World Economic Forum has honored us with numerous Lighthouse awards for our sustainable facilities, and we love sharing what we’ve learned. For more information about creating a compliant and sustainable production facility, please download our eGuide.
Add a comment