This audio was created using Microsoft Azure Speech Services
Although we think of wireless technology as young, history will show that it has been in our lives for a while now, but with a recent acceleration. Let’s take a look at the past milestones:
- 1896: first wireless telegram
- 1946: first radio-telephone service
- 1962: first communication satellites deployed
- 1979: first cellular network
- 1997: birth of Wi-Fi
Only relatively recently has this technology started to widely spread in our lives, thanks to 3 key wireless chip trends:
- Compactness
- Cost reduction
- Energy consumption drop
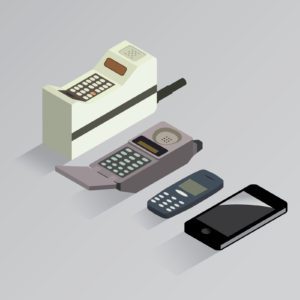
At the same time in the factories, 3 key drivers emerged:
- Mobility
- Flexibility
- Digitization
These drivers are meant to control or increase one of the key challenges for any industry: profitability.
Indeed, mobility saves operators time by reducing displacements and centralizing tasks; flexibility enables quick production lines repositioning and therefore decrease the time between shifts; digitization gives a better understanding on what’s going on in order to take faster and meaningful decisions.
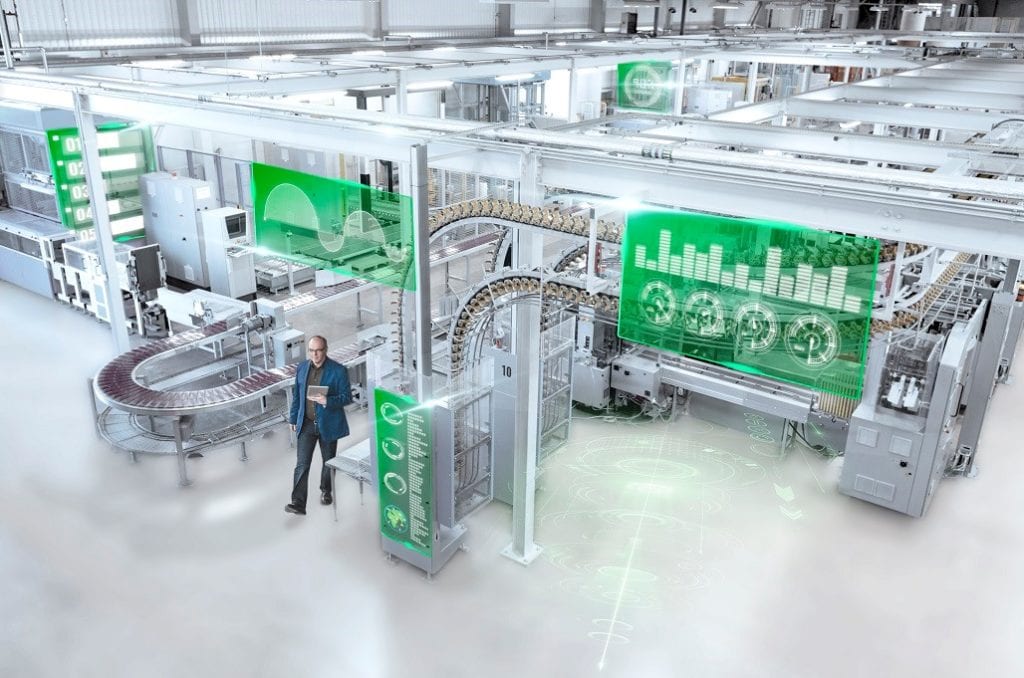
In these conditions, we will see wireless technology playing a key role in factories more and more, supporting these drivers thanks to the latest technological improvement: while compactness helps to integrate transmitters in even the smallest parts of the machines/processes, fixed or mobile, the competitiveness makes their cost insignificant, compare to the profitability generated.
Indeed, saving as low as 5 minutes of an operator’s time per day is still largely compensating the initial price of a few tens of dollars.
But on top of those improvements, one remains ever more important: energy consumption. The main drawback of wireless technologies is their need for batteries. Even though battery lifetimes have increased over time, running out of battery always happens at the worst time.
New wireless devices can be now found on the market which are not only compact and cheap but also battery-less: no more battery management, constant availability.
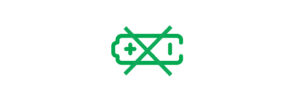
Those new devices are also compatible with the worlds-leading offer of Industrial Control units (pushbuttons, selector switches, …). They then bring the best of wireless for profitability without any drawback.
Mobility: work smarter and save operating cost
Mobility brings profitability by enabling 2 new options:
Control from far: opening an automatic door, turning on a light, starting a packaging process from a forklift etc… By avoiding unnecessary displacement, a lot of operator’s time is saved in the process.
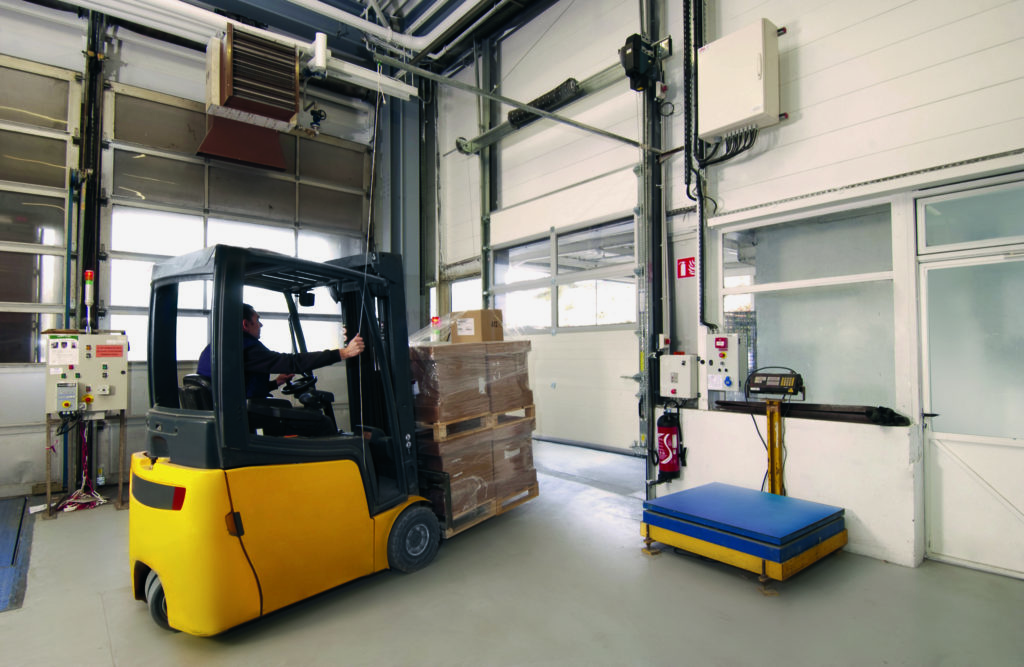
Control from close: adjusting a machine, a parameter. Most of time, when adjusting a parameter (position, level, etc…), especially during time between two production batches, 2 operators are needed: one which actuate the selector switch on the panel, the other one who checks the parameter and gives instructions. Only one operator is necessary when using a remote control with selector switch: he can control the parameter while looking directly at the machine, from very close.

Flexibility: quickly upgrade your equipment
In those ever-changing days, a quick adaptation, even of the physical assets, is a key for industrial actors’ success.
However, adding even the simplest and cheapest pushbutton to an existing equipment, to add a new function a control a new equipment, can become a highly cost- and time-consuming journey.
Indeed, you need to think about wiring, programming, even masonry sometimes.
Using a wireless and battery-less pushbutton or selector switch is therefore the most affordable solution and offers a competitive advantage to your operation…
But we can also think beyond that: you can duplicate a function. Let’s take an example.
Because of new standards, a factory needs to find a way to add an air extraction system to each of their 20 machines. To save money, the best scenario would be to actuate those extractors only when the processes are running.
Let’s now imagine to simply click a wireless contact on top of the existing electrical contact, on the start button for example. This wireless contact will actuate the extractor anytime the operator will press on the start button of the machine. No additional wiring or change on the existing wiring required.

Digitization: simply collect your existing machine data
On top of mobility and flexibility, a very interesting of a wireless and battery-less transmitter, compatible with standard industrial control units, is data collection.
Collecting data, even simple data, for example functioning duration, can simplify the calculation of key production indicators (Overall Equipment Effectiveness, Time before Maintenance) and therefore support the management to take fast and meaningful decision.
However, updating existing machines to enable data collection can be a very complicated, expensive and a long process. Even when the equipment is “connection ready”, the program needs to be updated which leads to complications:
- Very old software with no more support
- Risk of warranty loss
Then the only way to collect data from an existing machine is to add an additional PLC and to duplicate the wiring of the inputs/outputs. Still the programming needs to be done.
Using a wireless and battery-less contact, compatible with the standard electrical contacts, can do the job:
- Without modifying the machine cabling
- Without modifying the PLC program
Imagine a layer of connectivity on top of the exiting process. Anytime the operator will press on the control units (start, stop, reset, emergency stop, manual mode selector…) it will trigger the data wirelessly to a wireless collector, with all the data (contact ID, time stamp). Other wireless sensors can also be used to collect even more data (temperature, position, voltage, etc.). By analyzing the data out of the collector, then one can have a remote and digital picture of equipment.
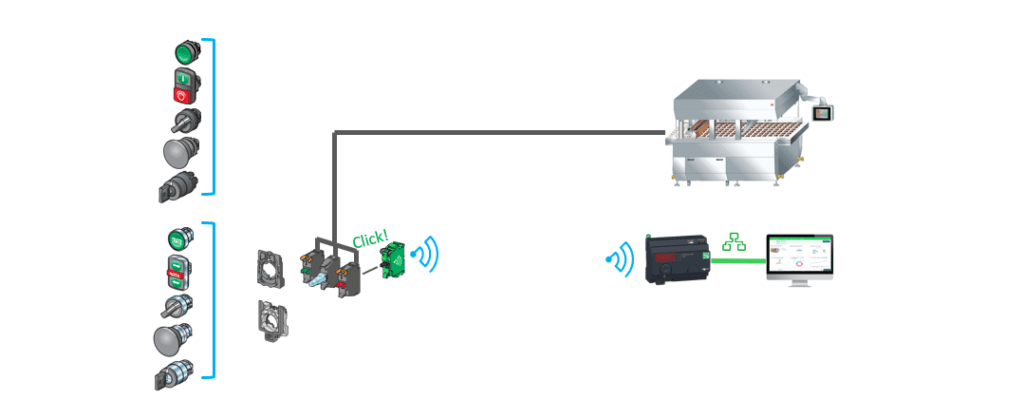
All in all, thanks to the latest innovations, wireless technology offers factories a handy and affordable solution to begin digital transformations.
On top of straightforward capabilities, as mobility and flexibility, now it can also help collecting data from the shop floor. Not only on brand new machines but also on existing machines which represent, per definition, most of the cases.
Useful links:
Solar Impulse – efficient solution award
The Reluctant Rise of Wireless in Industrial Control (blog)
Harmony ZBRT: Remote Control and Monitoring Made Simple (video)