The chemical industry is a large and diverse sector that manufactures a wide range of products, including fibers, plastics, surface finishes, and pharmaceutical excipients. Agriculture, construction, transportation, healthcare, and consumer goods are just a few sectors that use such chemical products.
Along with a significant amount of research and development, this industry produces chemicals from raw material such as fossil fuels and other natural resources using various techniques and advanced technologies.
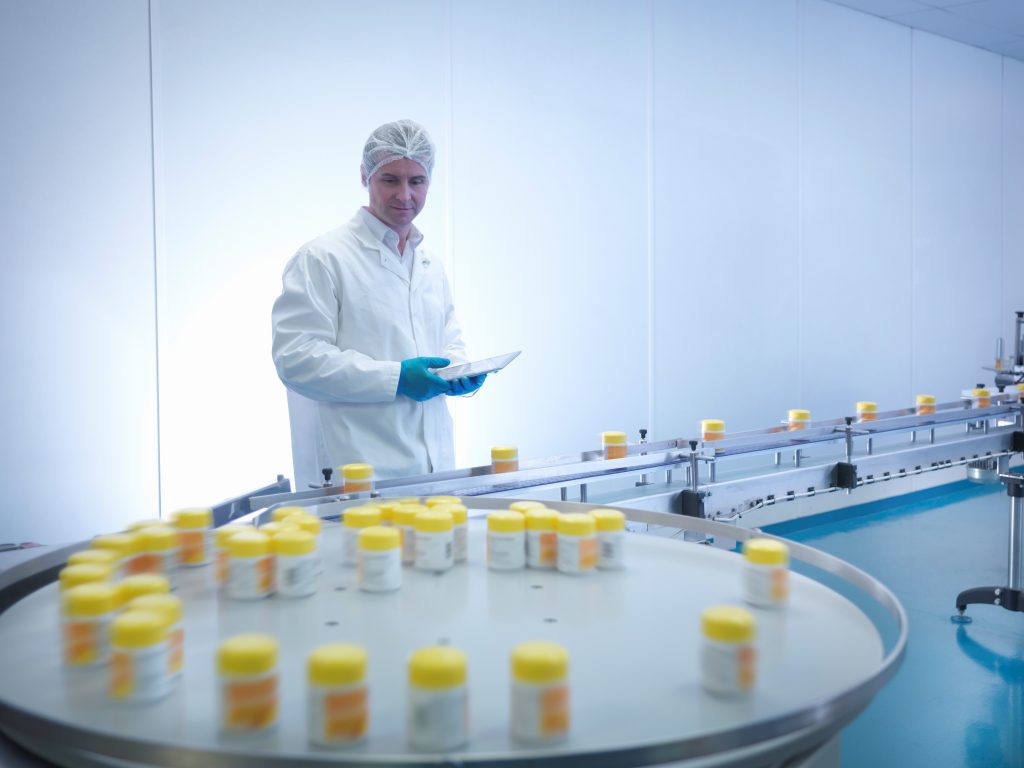
Due to the nature of its products and processes, various regulations and guidelines relating to safety and sustainability play a significant role. Here are global trends that affect the future of the chemical industry:
- Sustainability and environmental concerns
- Digitalization and autonomous systems
- Changes in global trade and economic conditions
- The shift towards renewable and bio-based chemicals
3 challenges the chemical industry is facing
Though the above trends are global and affect all industries, their impact on the chemical industry is colored by the industry’s own challenges. There are a number of chemical industry challenges and considerations for the future. Software-centric automation can address these challenges:
- Complex and rapidly changing processes: Small change in raw materials or operating conditions or technique impacts production significantly.
- Continuous market demand for new chemicals: Frequent updates to production systems and associated workflows which requires skilled resources to make changes that are tested and validated.
- Aging installed base of proprietary automation systems: Automation applications are system-specific, follow varying implementations of standards and lead to isolated islands that use hard-to-maintain interfaces both within OT and with IT systems.
It is clear that automation systems play a significant role in chemical production. End users are beginning to see proprietary automation systems as a barrier to growth and a cost, rather than an enabler and source of profit. There is a clear need to move from hardware-centric to software-centric automation, a.k.a. universal automation which supports modular plug-and-produce automation deployments.
Open processes increase profits
Many organizations recognize that next-generation industrial automation must be interoperable and break free from the proprietary locked-in model we have now. Moving to open automation not only benefits end users, but it also gives an edge for automation companies that exploit software innovation.
Digital transformation and electricity 4.0 will help the chemical industry avoid obsolescence and increase supply change resiliency and profitability.
There are organizations working towards this goal of secure, interoperable, and open automation.
- Open Process Automation Forum (driving O-PAS as a “standard of standards”)
- NAMUR (driving MTP and open architecture standards)
- OPC Foundation
- OMAC (PackML standard)
However, the approach is standards-based and could have the same pitfalls as previous attempts at open automation. Status-quo or incremental changes will no longer suffice. How we think about and deploy automation systems in the chemical industry requires a paradigm shift.
Path for the future of automation in chemicals
The world of plug-and-produce automation software components that solves industry challenges in a proven way. Universal automation is key. This is where Schneider’s expertise comes in as leaders in driving open and inclusive to achieve sustainability.
Here are several guidelines for the chemical industry to future-proof its automation and avoid obsolescence:
- Flexible – Change is the only constant. Production needs to be efficient (energy and raw materials) and sustainable in such an environment
- Autonomous – Bringing new products to market is a significant differentiator for chemical manufacturers. Leverage AI/ML at every stage of your production facility from design, build, operate to maintain
- Portable – Asset life of a chemical plant is typically in decades while automation hardware has shorter lifespans. Hardware component obsolescence should not force a full system upgrade
- Modular – Standardization and efficient deployment of control applications mirroring process modules / equipment is essential since these components of the chemical factory are typically built by multiple companies before they come together at site.
- Interoperable – A chemical facility has differing automation needs even within a single site. As a result, chemical companies select best-in-class system for each automation requirement. Hardware / software components from multiple vendors can be put together seamlessly in a system architecture
- Sustainable – Application is easy to maintain and update
- Open – Edit and maintain applications or the control system irrespective of who the supplier is
- Software centric – native integration with IT systems and ability to engineer control applications using IT talent pool – attracting the right talent is a challenge for the chemical industry.
Software-centric automation as the future
The technology and automation communities need to change to plan accordingly for the next generation. Schneider Electric is one of the founding members of Universal Automation Organization (UAO) which owns and shares an IEC-61499 based common automation software layer (UAO runtime) among hardware and software technology vendors, end users, system integrators, OEMs, startups, and academic institutions.
This containerized automation layer (UAO runtime) supports event driven control function blocks and allows separate models for the device, the control application, and the system. This separation will allow independent lifecycles for these components of any automation system.
Containerization enables agnostic deployment of control applications across multiple hardware components. This shared technology (owned and developed by UAO) will form the basis for an ecosystem of portable, interoperable, plug-and-produce solutions.

Automation systems are delivered to and operated by energy producers or chemicals manufacturers. So, any large change needs buy-in from these end users. ExxonMobil and Shell are examples of large end-users that have been actively behind open automation standards and are part of UAO.
Automation in the chemical industry requires machine controls, batch and continuous process controls which need to co-exist and have varying control applications sizes. UAO applications will allow chemical customers to ensure agile and reliable production while protecting their automation investments.
Learn more about universal automation.
Add a comment