According to the June 2022 OECD Global Plastics Outlook, plastics use will triple between 2019 and 2060 from 460 million tons to 1.3 billion tons in the baseline scenario, mainly due to economic growth.
Tripling plastic use can triple plastic waste, and almost half of this plastic is expected to be sent to landfills. This business-as-usual scenario is unsustainable, so building a truly circular economy is key to respond to this urgent challenge.
What is circular economy?
At Schneider Electric, we use the globally accepted definition by the Ellen Macarthur Foundation for circular economy, which defines it as a framework for an economy that is restorative and regenerative by design. It shifts the entire lifecycle of a product to resource-saving and circular practices. This framework also promotes long-lasting products with a take-back approach at the end of life for reuse, refurbish, and recycle.
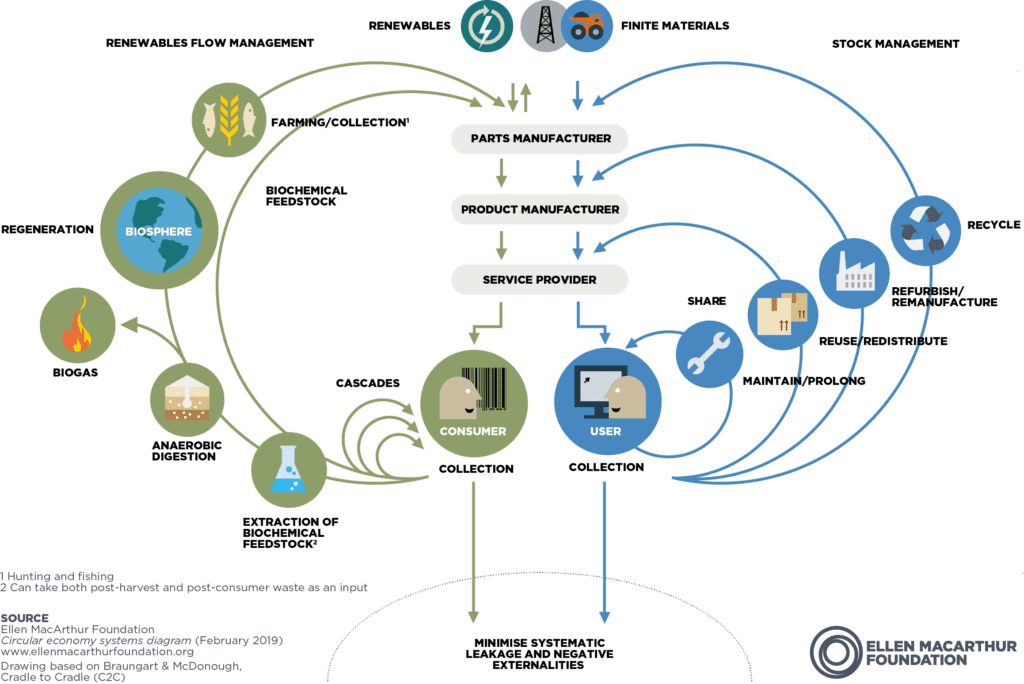
Comprehensive approach to make the circular economy a reality
There is no doubt that achieving true circular economy for plastic products will require a major undertaking in recycling. Schneider sees the need to focus on three key areas to address this urgent challenge of plastic recycling.
- Collection and sorting
The first step to take is to effectively collect and sort waste plastics, with a seamless connection to recycling facilities. The infrastructure and supply chain from the collection of waste plastic to the sorting facility must develop rapidly, with strong policies in a lot of countries. And, the development of advanced sorting techniques using artificial intelligence (AI), embedded digital watermarks in product, for example, should accelerate with process automation and digitalization.
- Advanced recycling methods
Secondly, development of new chemical recycling methods should speed up to complement existing and improved mechanical recycling. The implementation of advanced recycling is an absolute requirement to meet the level of quality necessary in a lot of products, particularly for food contact applications.
- Eco-design
Lastly, the eco-design and circular economy of plastic products should be considered to not only extend their life and improve their recyclability but also to provide safer options for people and ecosystems.
How to minimize CAPEX and de-risk projects
Substantial capital investments will be required to transform this industry. Success depends on the ability to minimize CAPEX, de-risk swift project deployments and sustainable operations. The following are methods to achieve such success:
- Integrate process and electrical simulation to arrive at a sustainable design that addresses operational risks through detailed engineering evaluations.
- Improve project engineering and construction efficiency which reduces CAPEX and schedule slip by integrating solutions like EcoStruxure Power and Process™.
- Build a digital twin that grows from early design into operations. Such validated and trusted information helps to drive the right decisions and actions that lead to increased operational efficiency and optimized OPEX.
- Create an open automation platform where multiple project stakeholders can collaborate to de-risk commissioning of recycling units, which leads into smart operations.
- Utilize modular design for process, electrical, automation, and digital systems to optimize costs and enhance speed of deployment.
- Apply AI for waste plastic sorting, real-time operation optimization, and preventive maintenance.
- Adopt and proactively test different recycled materials already available at a pilot scale and map the safer materials to be used.
- Incorporate innovative plastic product eco-designs without compromising technical specifications, especially in high-performance applications.
Advanced plastic recycling application
A real use case for advanced open automation is shown below for PET chemical recycling, which converts waste polymer (PET) into the respective monomers. These monomers can then be processed back into plastic in conventional polymer production facilities.

The following are the highlights from the modular open automation implementation at this recycling facility.
- Reactor unit controls designed as intelligent automation object in the open automation platform
- Modular engineering of plant automation aligned with process modularity
- Ability to expand capacity of the process (using modular approach) with no additional programming
- Improvement of total-cost-of-ownership due to open automation platform
- Additional optimization by means of advanced data analytics
- OT-IT integration translating into new value chain opportunities
Eco-design to enhance plastic product recyclability & safety
In this area, it is important to work closely and very early on with suppliers of recycled material to test recycled plastic and become an early adopter. This is especially true for high-performance plastic products for electronics and electrical applications.

Here are a few examples of how Schneider Electric approached eco-design and circular economy of plastic products:
- We tested several recycled materials from Pyrolysis of Tires to incorporate as part as their green materials roadmap.
- Mechanical recycling of fishing nets recovered from the oceans that have been incorporated into Schneider Elko Plus light switch products.
- To decrease waste, we partnered with UK-based DS Smith to create a new packaging solution that included printing instructions directly onto the box interior.
Additionally, flame retardant (FR) and additives components can be very harmful to the environment so finding alternate and safer solutions is key. For example, GreenScreen® provides an assessment method to rank the various chemicals products.
The success in plastic recycling will heavily rely on acting on the whole value chain from collection, sorting, implementation of new technologies and working on the product conception itself.
Add a comment