This audio was created using Microsoft Azure Speech Services
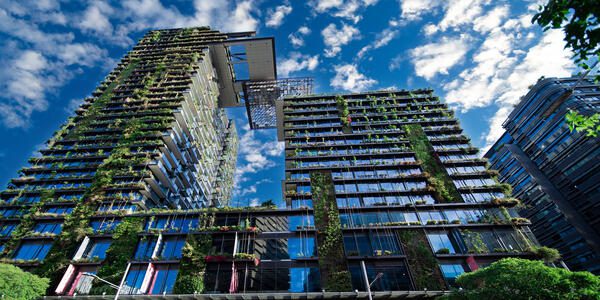
Market initiatives towards Green Steel production practices are helping manufacturers move away from fossil fuel-based to electrical energy-based steel production at pace. This change leads to several challenges for steel producers, including >3X increase in electrical power usage.
This higher amount of electrical power demands greater attention on the electrical distribution system design and costing which entails higher-sized electrical equipment, larger power cables, bigger installation footprint, and therefore a more complex design. In turn, this translates to higher capital expenditure (CapEx) making the power distribution system a critical area necessitating proper planning and design at the early stages of a project.
In an electrical system, the majority of the cost comes from the required MV switchgear (circuit breakers), transformers, busbars and power compensation equipment. Each of these cost points can be optimized from appropriate design considerations. This would also reduce footprint, installation cost, ongoing maintenance cost and stock inventory of the related (critical) spare parts. Thus, there is a potential for a significant reduction in CapEx and OpEx if done well.
Over the years, Schneider’s experience in this type of electrification projects has driven us to a set of best practices I´m glad to share here:
Optimized power system design considerations:
- Various OEMs develop unique power system designs specific to their unit package like DRI/EAF or LF, this is often limited to their own package, not considering the wider needs of the value chain.. Consequently, the overall design amalgamates these diverse pieces of information and requirements which is not conducive to optimization. Hence, the overall power system design should remain unified, while procurement can be conducted in phases according to specific requirements.
- Different system suppliers attempt to introduce their nonstandard specialized products to eliminate their competition. Even though these products may have an attractive initial purchase cost, their monopoly ultimately results in higher costs for spare parts and maintenance as time goes on for the end user. Hence, one should adhere to standard product ratings and refrain from using specialized rating equipment where possible and consider open systems
- Often we see then the key decision makers tending to go for low risk and incorporate excessive cushions and/or redundancy in the system because of a lack of confidence, knowledge, excessive caution, inadequate planning, over-provisioning, or other factors. So, rather than incorporating such cushions and redundancy, we would suggest investing instead in education and partnerships allowing to place greater reliance on advanced technologies like health monitoring systems, preventive maintenance systems, and energy management systems and leveraging their specific benefits for the site.
- Users must ensure that they stay within standard fault current values to avoid compliance issues with OEMs and increased costs. This can be achieved by avoiding power transformer parallel operation and/or adjusting the transformer percentage impedance as needed as systems evolve at the site.
- One should strive to minimize variations, as this not only reduces the need for expensive spare equipment but also enhances asset as well as manpower management.
The optimization work can be carried out either manually or using software. The initial step involves manual optimization based on experience and domain knowledge, which is then replicated in the appropriate software for further simulation.
However, engaging in manual calculations, study and optimization activities comes with inherent limitations. There exists a boundary that cannot be surpassed through manual efforts alone. Therefore, to achieve further optimization, it becomes imperative to employ suitable software for the task. This also with the benefit of covering more scenarios before locking in the best solutions for the site. Sites can leverage the ETAP software from Schneider Electric in conjunction with their partners or Schneider Electric to increase their domain knowledge to optimize the power system overall. This widely accepted software not only facilitates power system design study but also enables optimization. However, domain knowledge is essential while working with this software too but as the installed base is significant and global many of our clients use it internally before working with us around nuances based on our product portfolio.
This software offers various modules to cater to different needs, including:
- Load flow studies:
Load flow analysis stands as a fundamental power system analysis during the planning, design, and operation stages of power systems. It serves the purpose of computing the stable performance of the system under different potential operating scenarios and examining the impacts of alterations in equipment configuration.
- Short circuit analysis:
A short-circuit study involves analyzing an electrical system to ascertain the currents’ magnitude during an electrical fault. The initial step in ensuring the safety of the power system involves comparing these computed values with equipment ratings.
- Arc Flash studies:
An Arc Flash Study involves analyzing an electrical distribution system to calculate the worst-case arc flash hazard personnel could face during an arc flash event. Once the hazard is determined, control measures can be implemented to reduce the risk.
- Transient behavior studies, Harmonic analysis, Relay protection and coordination, and more.
Conclusion
As we are aware, high-voltage power system equipment comes with a substantial cost. By optimizing the relevant Single Line Diagram (SLD), we can achieve significant savings in capital expenditure (CapEx), ranging from 20% to 40% on a case-by-case basis. In terms of cost, this saving could amount to approximately ~10 million Euros or more considering typical integrated green steel productions we see in the market.
Such optimization would then lead to further savings in operational expenditure (OpEx) for the duration of the life of the asset and is often 10-20 years and beyond. We invite you to discuss with us how we can further, enhance your operational efficiency and overall reliability minimizing your total expenditure (TotEx) in Green Steel production.
Want to know more? Read here on Power distribution system and related challenges in Electric Arc Furnaces
Add a comment