This audio was created using Microsoft Azure Speech Services
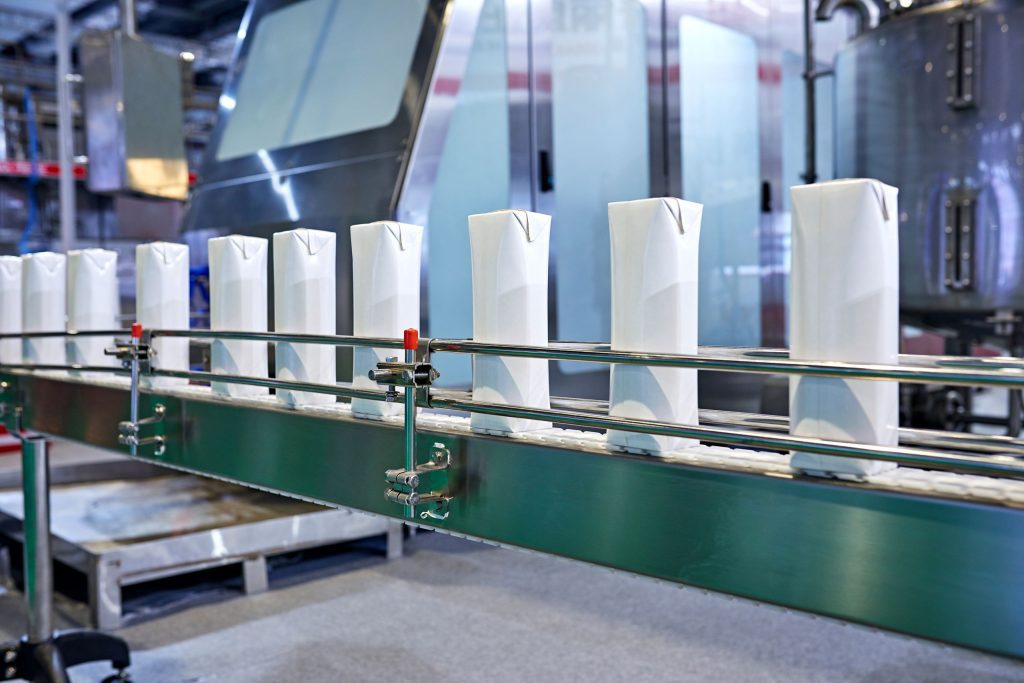
Milk is no longer just milk.
Today’s consumers expect a wider range of dairy products. In terms of variety, few sectors can match the dairy industry, where seasonal variations and product innovations are also at home.
The range further reflects the dynamic consumer environment and the changes in eating habits.
As such, the development of new products is a crucial activity for remaining competitive. Demand is constantly changing, and dairies that can respond quickly and flexibly to consumer needs have a real advantage in the market.
And this is why lean and adaptable production is so important. Smaller batch sizes, shorter product life cycles – the innovations just keep on coming.
Only those willing to change remain.
Integration is the key
When looking to the future of the dairy industry, an important, if not the most important, vision is that of the integrated dairy. This is an issue that impacts both greenfield and brownfield plants.
Bringing digitalization concepts to life is comparatively easy when constructing new processing plants. Existing or brownfield plants are generally characterized by a heterogeneous landscape of varying, supplier-dependent automation solutions. However, the resulting divergent life cycles and plant-wide data tend to weaken the ability of the plants to adapt and be flexible. When integrating new digitalization projects seamlessly into production, it is advisable to introduce modular individual solutions that – when used effectively – pay for themselves in a short time.
One of these lucrative individual solutions is, for example, a data management level between top floor and shop floor. While many dairies still utilize paper to bridge this vital gap, a software solution can offer an effective remedy by serving as both a modeling and a contextualizing element. Besides IT skills, this also requires process know-how and technical expertise.
From grass to glass: the fully integrated dairy
Hochwald Foods GmbH, one of Germany’s largest dairy cooperatives, has been tackling this issue together with ProLeiT.
Automation specialist ProLeiT is playing a pivotal role in the construction of a brand-new plant in Mechernich, which represents one of Europe’s largest greenfield projects in the UHT milk industry. It is all about delivering the vision of a ‘fully integrated dairy’ as part of a collaborative partnership.
Founded in 1932, Hochwald Foods presently employs more than 1,960 people at ten locations and processes more than two billion kilos of milk annually, which is used to make food for people around the world. The new plant, which was planned from scratch, offers an annual capacity for more than 800 million liters of milk.
Thomas Wunderlich from ProLeiT explains how the project came about: ‘With over 35 years of experience in process automation for milk-processing companies, we have long engaged in knowledge transfer with Hochwald. After securing the order for the MES solution integrated within the existing ERP system, we were soon entrusted with responsibility for the complete automation.”
Frank Brück, Head of ICT at Hochwald, says in summary: “Thanks to ProLeiT’s end-to-end horizontal and vertical integration, everything from the entrance barrier to the finished pallet is fully traceable from a compliance and quantity perspective.”
Achieving a global data view requires a high level of reporting transparency. Other objectives include reducing paper use in production, providing intuitive user guidance and ensuring standard visualization of the entire plant technology.
Accurate solution for horizontal and vertical integration
ProLeiT offers precisely the right solutions to meet all the needs: Based on Plant iT V9, automation is achieved with a perfectly harmonized blend of Plant Liqu iT and Plant Batch iT. This also allows Hochwald to operate well within specified quantity limits in the area of beverage milk blending and dry ingredient handling.
The amount of data collected across the value chain presents a wealth of opportunities for data-based insights. At the same time, the primary challenge lies in the fact that only contextualized data can yield such significant knowledge gains. However, there is more to it than simply collecting and accessing data. Manufacturers also need to analyze data within a specific context before making decisions. And without the correct context, production data could be misinterpreted or misunderstood. Insufficient contextual information can result in flawed analyses and subsequent erroneous decisions, adversely affecting production, quality and overall business results.
As such, Hochwald benefits from the fact that ProLeiT’s automation solutions deliver data within the relevant context (e.g. time, place, material reference, operator feedback, etc.) as soon as the data are generated. While many other systems retroactively assign the data context, leaving room for potential errors, Hochwald’s production data in Mechernich are contextualized directly at process control level.
Technological blueprint for other Hochwald locations
When summarizing the project, Thomas Wunderlich says: “We are delighted with the trust invested in us and the challenge of bringing to life the vision of a fully integrated dairy with Hochwald. This project will also serve as a technological blueprint for other locations. For instance, our colleagues are currently automating another plant in Thalfang.” It is also a compelling testament to Germany’s prowess as a business location, which was validated by the successful launch of the plant in 2022. And provides Hochwald with the assurance of scalable growth through modular expansion, ensuring its adaptability to any future needs.
Add a comment