This audio was created using Microsoft Azure Speech Services
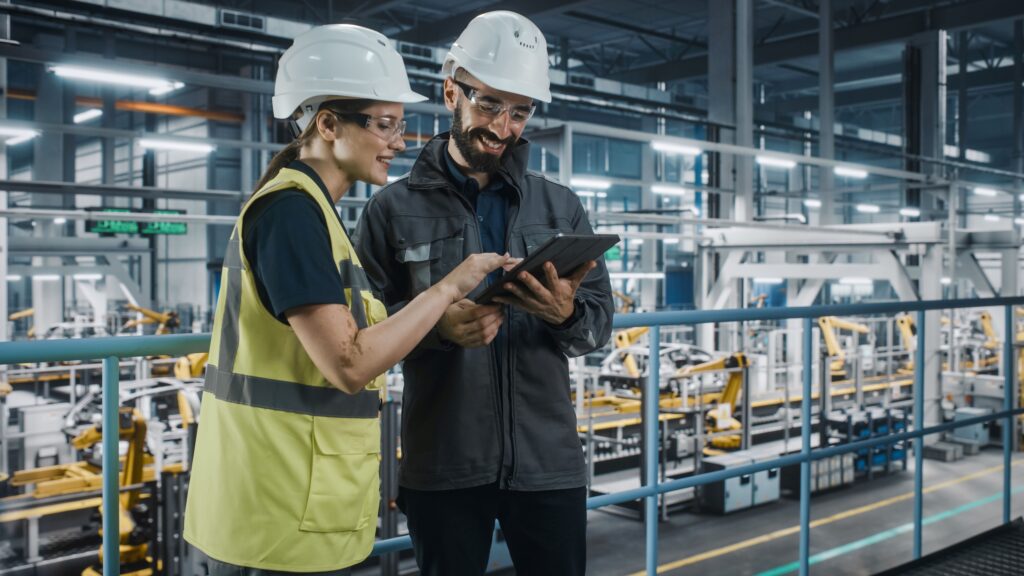
A recent report found that 80% of manufacturers believe smart factories are crucial to their future success.
Actionable information is key to improving process efficiency, but today, many facility personnel face the paradox of information overload. The greater the volume of alerts and alarms, the harder it can be to monitor shifting conditions effectively. Although control systems are essential to support the complex, interconnected operations in most industrial facilities, legacy distributed control systems (DCS) or safety systems cannot always provide the high-level visibility front-line teams need to manage changes in programmable automation equipment appropriately.
Leveraging smart automation technology that analyzes and prioritizes mission-critical data can give stakeholders the tools to avoid distractions, focus on priority issues, and run plants better. Choosing the right automation enhancement tools and services can also help decision-makers manage change, solve persistent challenges, and boost the productivity of key job roles in process-intensive plants:
- Plant operators – need to improve facility utilization, operational efficiency, and productivity. With better visibility into the criticality of abnormal conditions, updated control logic, new alarms, and system extensions, operators can better categorize problems and accelerate decision-making.
- Safety engineers – need to document all tags names references, have multiple ways to search data, and change tracking. Enhanced Management of Change (MOC) tools that provide critical system governance controls and retention of knowledge capabilities can significantly improve safety performance.
- Plant engineers – are expected to improve a plant’s efficiency, increase production, and reduce manufacturing issues. With potentially thousands of control loops in constant need of careful, systematic management, superior loop management capabilities will help engineers identify and adjust system parameters as conditions change.
With industrial environments being highly variable, numerous risks to performance and safety are present, so it’s always essential to ensure all personnel involved in the production process have the right tools to identify and manage control system changes to protect automation assets and boost overall productivity.
Technology operates hand in hand with people in a smart plant
For many industrial plants, operating EcoStruxure™ Foxboro™ DCS and EcoStruxure Triconex Safety Systems provide users two combined software and consulting services solutions. They provide proven tools, techniques, and strategies to manage change, improve safety, meet goals, and minimize risks to automated production:
- EcoStruxure System Advisor – Process Control – a knowledge administration and system governance application that centralizes electronic documentation and alarm management functions to improve operational integrity and insight. It provides powerful change management capabilities, configuration functions, and alarm management capabilities.
- EcoStruxure System Advisor – Process Safety – helps improve operational integrity and insight by providing enhanced configuration documentation, change tracking, and I/O management for Triconex Safety Systems.
These smart digital systems and collaborative expert services provide information on managing changes as new control logic, alarms, extensions to the system, and upgrades to the control system are implemented. Together, they offer a comprehensive solution for plant operators looking to make their plants run better. The Resident Engineer program offers technical support and operation improvement through trusted advisors. This way operations can add value through services focused on day-to-day engineering implementation and support for Schneider Electric assets.
Make your existing data more useful
Implementing smart digital tools to enhance plant performance doesn’t have to be an all-or-nothing proposition. Organizations risk overlooking easier-to-implement, low-cost, high-return opportunities to boost process efficiency and safety today by focusing solely on future transformational gains.
Enhancing plant operation doesn’t always require the newest technologies. Often the highest-value solutions make better use of existing tools. Yet, despite the potential payback, many decision-makers are sometimes reluctant to move forward with process improvement initiatives. Primary concerns include costs, lack of in-house digital expertise, insufficient real-time equipment monitoring, and IT security risks.
However, thanks to the capabilities provided by advanced digital tools, combined with professional services, enhancing a plant’s existing control and safety systems is straightforward and cost-effective, as well as being a vital first step in making processes run better.
Discover how you can get more from your existing process control and safety systems by visiting the EcoStruxure System Advisor page.
Add a comment