As we approach the end of the year, facility owners and managers must prioritize safety shutdown procedures to protect their assets and ensure the well-being of their employees. A safety shutdown is a crucial process that can prevent costly outages, unplanned shutdowns, and worker injuries in hazardous situations. In this blog post, we will explore the importance of December’s safety shutdown and provide a detailed guide on how to execute this essential procedure effectively.
Understanding the scope and benefits of a safety shutdown
Although a safety shutdown is often just perceived as a precautionary measure, it plays a pivotal role in the holistic safety and operational efficiency of a facility. A safety shutdown is a strategically planned cessation of operations, designed to address and mitigate potential hazards. This process serves as the backbone for maintaining the integrity of people, equipment, property, plants, and the environment amidst hazardous conditions.
The cornerstone of a safety shutdown is its ability to preemptively halt operations to avoid accidents and minimize risk exposure. Beyond immediate safety benefits, this practice is instrumental in ensuring compliance with safety regulations, safeguarding against legal repercussions, and financial penalties that can arise from non-compliance.
A well-executed safety shutdown facilitates a structured opportunity to review and enhance safety protocols, ensuring that each iteration is more refined and effective. It is through this continuous improvement that facility owners and managers not only uphold but also elevate safety standards.
It’s more than just a way to adhere to regulatory protocols, it’s a crucial component of a facility’s operational fabric. Safety shutdowns in facilities not only prevent detrimental incidents but drive operational resilience, ensuring a smooth return to normal operations.
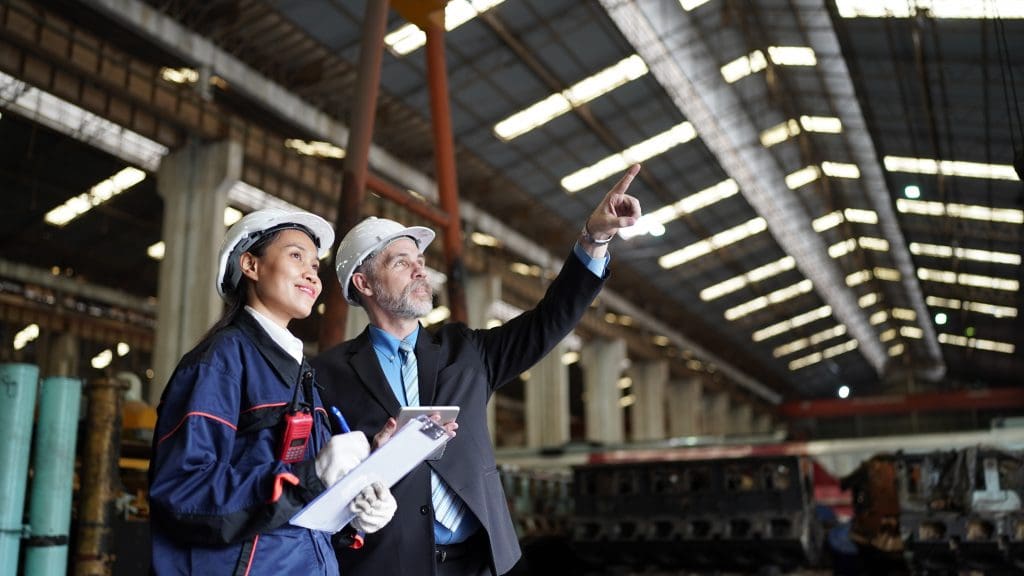
Preparing for a successful safety shutdown
Laying the groundwork for a successful safety shutdown requires meticulous planning and commitment to detail. Begin by conducting a thorough risk assessment to pinpoint any potential hazards within your facility that could pose a threat during the shutdown process. This proactive approach is vital for creating a tailored shutdown plan that addresses the unique needs and vulnerabilities of your facility.
Next, develop a comprehensive shutdown strategy that clearly delineates each step of the process. This strategy should include specific tasks, assign clear responsibilities to team members, and establish realistic timelines for each phase of the shutdown. It’s important that this plan is not only practical but also adaptable, allowing for adjustments as needed based on real-time conditions and unforeseen challenges.
Communication plays a crucial role in the preparation phase. Ensure that every employee is informed about the shutdown plan, understands their role within it, and is equipped with the necessary knowledge to execute their responsibilities safely and effectively. This may involve conducting training sessions focused on safety protocols and emergency procedures, reinforcing the importance of each individual’s contribution to the shutdown’s success.
Lastly, consider conducting a trial run of your shutdown procedure, if possible. This exercise can reveal potential gaps or inefficiencies in your plan, providing an invaluable opportunity for refinement. By rigorously preparing for your safety shutdown, you can significantly reduce risks, safeguard your assets, and ensure a safer environment for all involved, setting the stage for a seamless and effective process.
Implementing energy management and sustainability practices
A safety shutdown provides a great opportunity to elevate your facility’s energy efficiency and sustainability. Consider this period as a strategic juncture to review your energy usage patterns and pinpoint areas where improvements can be made. It’s about identifying not just the quick fixes but also understanding the long-term strategies that can transform your facility into a model of sustainability. Whether it’s upgrading to LED lighting, optimizing HVAC systems, or introducing programmable thermostats, each modification can contribute to a substantial reduction in your carbon footprint and energy bills.
The shutdown period also provides an opportunity to consider renewable energy integration like solar and wind, reducing non-renewable source reliance and enhancing sustainability. It adheres to global directives and establishes your facility as a steward of the environment.
You may also want to consider the adoption of carbon corrective initiatives. By investing in environmental projects elsewhere, you can compensate for your facility’s carbon emissions, contributing positively to the global effort against climate change. Through these actions, the safety shutdown becomes more than a precautionary measure—it evolves into a catalyst for sustainable growth and operational excellence.
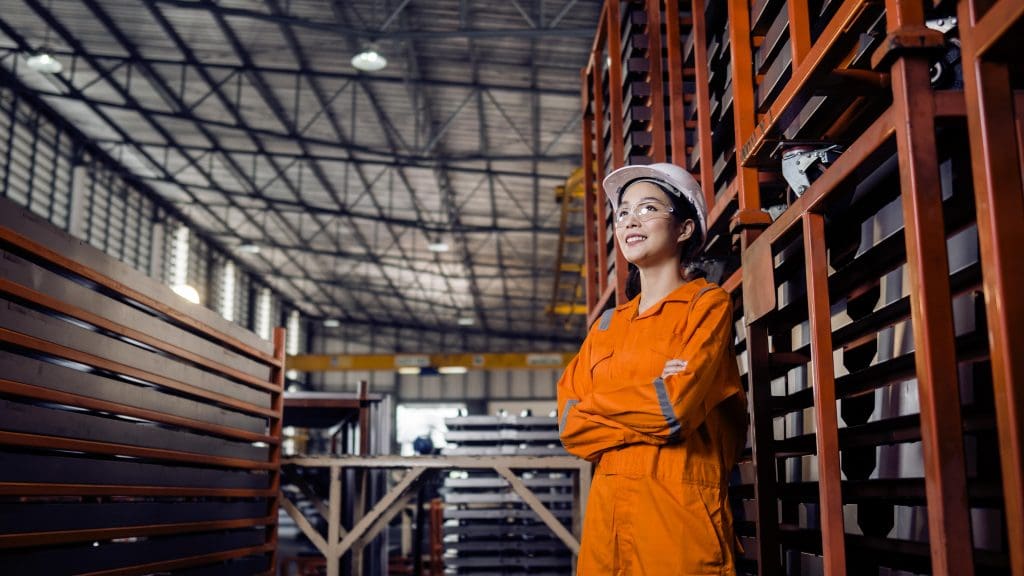
Ensuring a smooth restart after the shutdown
After the safety shutdown, it’s important to return to operational normalcy with precision and care. A good place to start is by conducting detailed inspections of all equipment and infrastructure to affirm their optimal functioning and safety compliance. This examination is essential to uncover any potential issues that could impede operations or compromise safety.
It’s also important to connect with your team as you reopen operations. This not only facilitates a seamless reintegration into their roles but also reinforces the collective commitment to a safe working environment. It’s about nurturing an atmosphere where safety and operational readiness go hand in hand.
Monitoring operational metrics closely as activities resume will offer valuable insights into the effectiveness of the safety shutdown and the restart process. This data serves as a compass, guiding adjustments and optimizations to ensure the highest standards of safety and efficiency are maintained.
The restart phase is not just about resuming operations but reaffirming your facility’s dedication to excellence in safety, sustainability, and operational integrity. This approach ensures that the restart process is not just a return to work, but a step forward in your ongoing journey towards operational excellence and safety leadership.
Learning from the shutdown to enhance future operations
The culmination of a December safety shutdown isn’t just about pausing operations; it’s a critical moment for reflection and growth. Engage in a thorough post-shutdown evaluation, meticulously analyzing the process from initiation to completion. This review is indispensable for uncovering both strengths and areas needing refinement.
Embrace this opportunity to refine your facility’s approach to safety and operations, ensuring that each shutdown becomes a stepping stone towards enhanced performance and resilience. Through this continuous cycle of evaluation and improvement, your facility not only adheres to the highest standards of safety but also advances its commitment to sustainable and efficient operation, setting a benchmark in operational excellence.
Learn how Schneider Electric services can help you maximize efficiency and sustainability during your annual shutdowns.
Add a comment