Oil refineries emit almost 5% of global GHG emissions
Decarbonization has become a global priority for all industries in an effort to stop climate change. The consequences of climate change are dire, include harming the environment, human health and the global economy. While all industries emit CO2, a major contributor to climate change, the oil and gas (O&G) sector has been singled out as an important industry to decarbonize because it is responsible for 15% of total energy-related emissions. Many of those emissions come specifically from oil refining. There are more than 800 oil refineries worldwide and an average-size refinery (i.e. with a crude capacity of 150 kbbl/day) typically emits more than 1 million tons of CO2 per year, depending on its specific configuration, without taking into account the emissions from the downstream petrochemical plants potentially integrated with a refinery.
It is challenging to reduce oil refining emissions because refining is energy-intensive and complex with significant energy needs. For example, a typical medium-complexity refinery requires around 700-900 MW of thermal power and over 50 MW of electricity (Schneider Electric, 2024). The bulk of refineries’ GHG emissions come from burning fossil fuels for process heating and steam generation, but some also come from specific processes like hydrogen manufacturing.
Electrification is an effective strategy for reducing CO2 emissions
Oil refineries and petrochemicals have a number of decarbonization options to consider, such as energy efficiency improvements, carbon capture, utilization, and storage (CCUS), low-carbon or green hydrogen generation, and electrification of the process. However, there is no single best method for reducing CO2 emissions while being technically feasible and economically attractive for all refineries. Any plan must be tailored based on a refinery’s size, configuration and the regulatory requirements it must fulfill.
Electrification – using low-carbon electricity to power processes traditionally reliant on fossil fuels – is one of refineries’ most effective decarbonization options, according to research from global organizations, including IRENA, IEA, and the industry-led Oil and Gas Climate Initiative’s Energy Efficiency work stream. Electrification can be powered on a small scale using renewable energy sources, such as solar, wind, and biogas (produced either on-site or remotely), but nuclear power may also be important for large-scale electrification.
Many of refineries’ fossil-fueled processes and equipment can be electrified
A refinery’s electrification potential is determined based on criteria, such as its fuel gas and steam balance, process configuration, electricity supply and distribution, and energy mix.
While there are many opportunities to electrify, some examples include:
– Steam-operated equipment: Steam-operated equipment, such as steam ejectors used for vacuum operations and turbines used as compressors drivers, can be electrified using existing technology. This can reduce CO2 emissions from the steam production, while also improving energy efficiency. Electric motors coupled with variable speed drives (VSD) are much more energy-efficient (around 90-95% energy efficient) than their steam turbine counterparts (as low as 25% energy efficient). Equipment like electric steam boilers can be used to generate steam at lower carbon intensity or “green steam,” which can differ based on steam temperature, pressure, and production flowrate requirements.
– Process heating: Besides the steam production and usage, there are multiple opportunities to electrically power process heating equipment using commercially available technologies. For instance, low-hanging fruit can be found across multiple distillation reboilers, fired heaters, especially when stacking the benefits of energy efficiency gains and reduced CO2 emissions with operational and/or maintenance cost improvements (e.g. replacing end-of-life, low-efficient or technically constrained heaters, identify fuel or steam-powered bad actors, improve process controls accuracy, faster ramp-up/down times to benefits from grid flexibility mechanisms, etc.). For petrochemicals, especially steam cracking furnaces, there are on-going developments to scale-up electrical cracking furnaces which represent the largest CO2 emitters of such plants.
Refineries must consider how electrification can introduce challenges, such as changing energy needs
Refineries and Petrochemical plants must address several challenges before starting widespread electrification efforts. They must ensure their power systems can handle increased electricity requirements. Currently, only 5% to 10% of refineries’ energy use is electrical. Increasing this to 20% or more will require refineries to source additional power or increase internally generated renewables or low-carbon power, while upgrading their power distribution systems. It will also involve working with grid utilities to assess power availability and determine how the plant can benefit from grid stability mechanisms or flexibility.
Electrifying direct-steam or gas consumers can affect the overall energy balance of the plant. This may require changes, such as adjusting the steam network configuration or the way steam is produced and distributed across the site. The fuel gas network balance might also be affected by reducing natural gas demand. These changes can unveil further optimization opportunities.
To optimize efforts, electrification initiatives should start with a comprehensive strategy
There is no cookie-cutter electrification plan because every refinery or petrochemical plant differs depending on factors such as its location, configuration, and processes and equipment that are currently being used. Refineries, as well as other segments of the oil and gas industry, can maximize electrification initiatives by working with industry experts who can help develop a scalable, individualized strategy. Together they can create an electrification roadmap that assesses technical and economic impacts while ensuring the operational integrity of the energy system.
Take a deep dive into refinery electrification
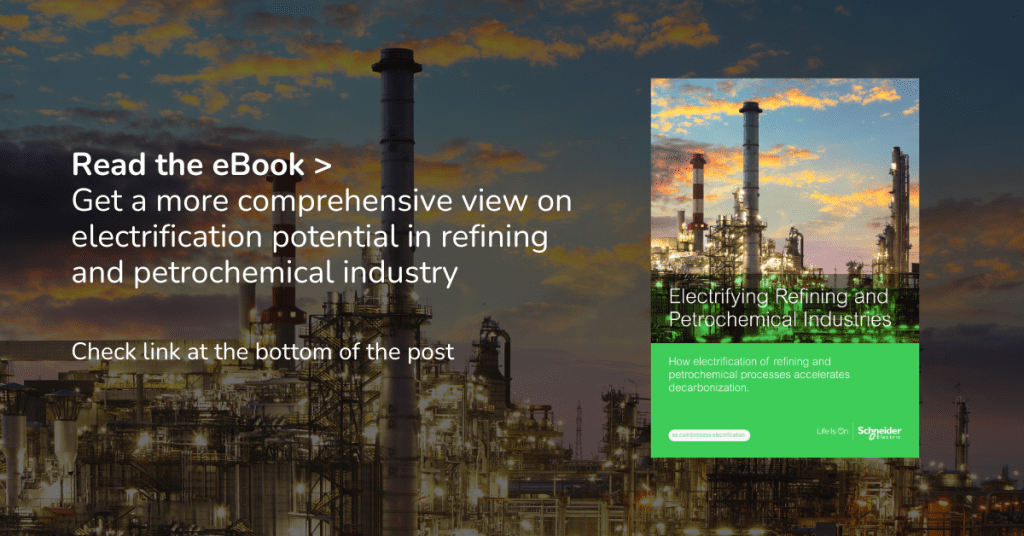
Download our eBook “Electrifying Refining and Petrochemical Industries” to get a more in-depth look at how and why refineries should electrify, including best practices and tips for overcoming electrification challenges.
About the author
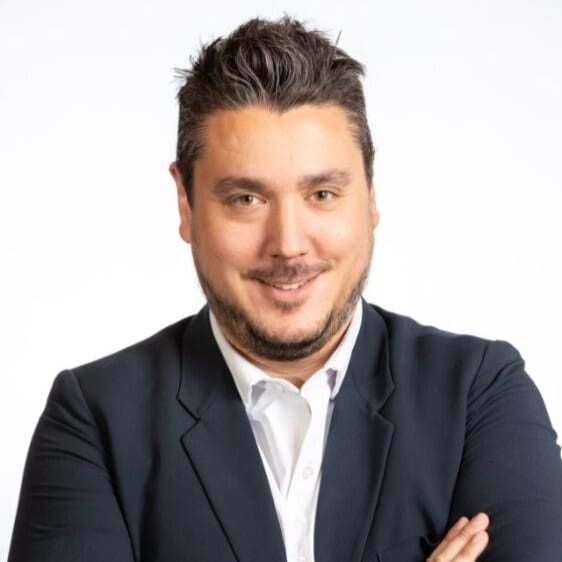
Damien Feral, Process Expert Oil and Gas Industry – Electrification Consulting
Process Domain Expert Throughout his 13 years of professional career, Damien’s area of expertise has been in downstream oil and gas chemicals process, building up his extensive knowledge base in-process unit operations, troubleshooting, start-up, as well as energy efficiency and decarbonization processes for heavy industries.
Add a comment