This audio was created using Microsoft Azure Speech Services
Can we really challenge the limits on the specifications of a project?
Edwin Hubble predicted for the first time that the Universe has limits and observed that it is expanding (see Hubble’s law). Because of the Big Bang, everything appears to be flying away from us.
In our small world, the current trend is for automation and control projects to go through a greater integration of functions. It is the opposite of the Big Bang: electrical and electronic equipment is installed in tighter and tighter spaces. So, the environmental conditions are increasingly close to the operating limits of the equipment.
We are very aware of the risk that an engineer takes to establish the maximum (or minimum) limits in relation to external environmental conditions of an installation. Therefore, we recommend he or she always take measures in advance whenever possible.
A very visual example is an installation in countries with high solar radiation and high temperatures. In those situations, the limits are usually established in projects with outdoor temperatures of up to 60ºC.
But, the questions we must ask ourselves when we receive projects with these values are:
- Is the installation indoors or outdoors?
- Are there people working nearby at this temperature? Normally they could not breathe, so we question if this value should be the maximum stable temperature. That is, should it really be considered permanent and throughout the day?
- If the installation is outdoors, will it be dealing with the hours with the highest incidence of solar radiation?
Our experience is that getting answers to such questions can pay off in the preliminary and installation phase of a project.
In beginning of a project, there are some tips that should be kept in mind that will make the job of designing easier. First, it is best if you have proven values close to reality. Such examples will allow you to be able to facilitate the establishment of extreme values in projects in an appropriate way.
Second, if an installation does not exist, temperature extremes cannot be measured. That would seem to make it impossible to get accurate environmental values.
But, you may be able to find an installation with a very similar architecture or power. You can look at projects in subway technical rooms and machine cycles in continuous industrial processes, depending on what you are trying to estimate. For examples in food and beverage, you could look at previous studies of risks of condensation and humidity in bottling plants and so on.
By finding and examining applicable examples with very similar electrical architecture, improvements can be achieved in equipment optimization. This will allow you to avoid materials and equipment problems and changes. In turn that will lead to a CAPEX cost reduction of the installation.
At the project stage or start-up of an installation, finding out the exact environment is also useful.
Even in the commissioning, it may be very beneficial to know in detail the thermal environment that the installation can take. What’s more, the first behavior in real conditions makes it possible to estimate the health of the electronics over the course of the life of the project.
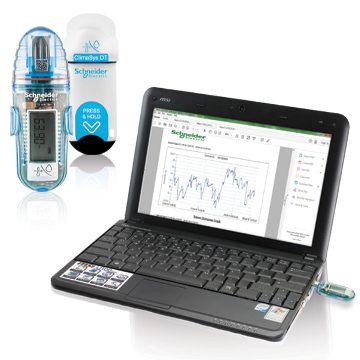
At Schneider Electric, we have developed an ideal diagnostic tool for these design and installation situations. You can guarantee the highest accuracy of the conditions and reliability of the installed equipment by using EffiClima and ProClima software. This process will provide thermal reports and reliable and proven thermal solutions for ventilation, heating, air-to-air or air-conditioning exchanges.
The ClimaSys DT tool enables reliability, energy efficiency, safety and lifetime to be applied to critical production processes with severe downtime risks. The tool can help ensure continuity of service by optimizing facilities in terms of CAPEX and OPEX.
For more info, please download the e-brochure, “Get maximum control panel performance and reliability,” and watch our video.