This audio was created using Microsoft Azure Speech Services
Someone once said, “You can’t solve today’s challenges with yesterday’s solutions.” You don’t have to look further than the metal processing industry to see this in action. Even though the legacy approaches to blasting, crushing, and smelting are reliable, they are no longer sufficient to support the growing need for efficiency, sustainability, and energy recovery in metal processing. For example, global demand for lithium is expected to quadruple by 2030, and nickel is forecasted to grow at nearly the same rate, thanks largely to sustainability initiatives and electric vehicle (EV) production.
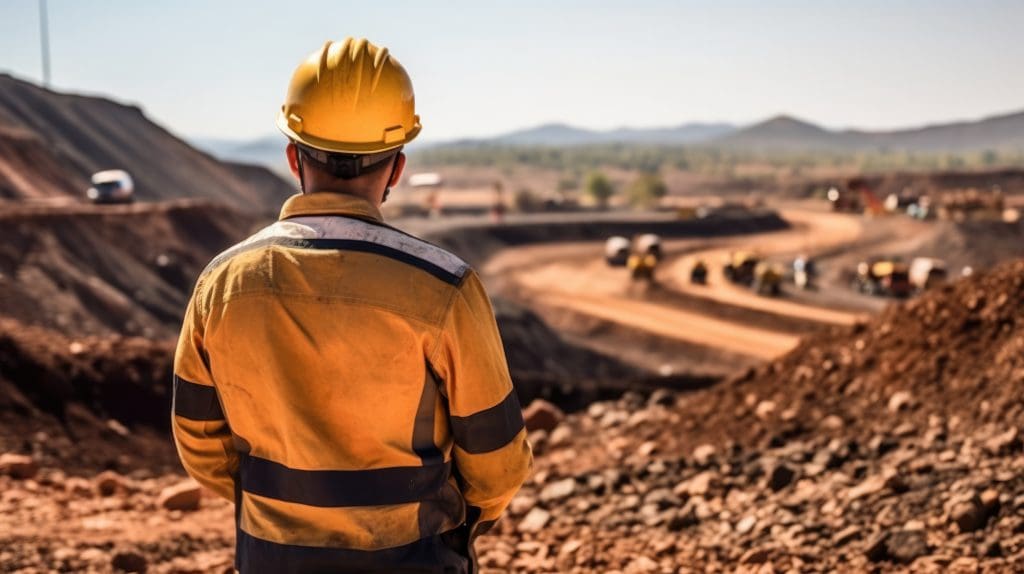
In response, metal processing operations are embracing data-driven innovations to balance their production needs with energy efficiency and sustainability. Through this data-driven decision-making, metal processors can scale operations and optimize complex processes such as crushing, concentration, leaching and casting.
Here’s a closer look at the driving forces behind this transformation.
Load balancing, demand response, and real-time optimization
One of the biggest hurdles for metal processing plants is their remote locations, often in areas where the power grid is unreliable or non-existent. This makes energy management and efficiency crucial for maintaining continuous operations. At mine sites, load balancing and demand response systems enable intelligent energy distribution in plants. In this way, operations to continue seamlessly during energy shortages or peak demand.
Integrating data from multiple systems enables real-time energy optimization. This enables operators to adjust energy usage instantly to maximize efficiency and minimize waste. This is especially valuable in energy-intensive processes like smelting and refining. Precise furnace control can prevent unnecessarily high temperatures (and the associated excess energy consumption) and help lower operational costs.
Enhancing efficiency through a supply chain view
A critical factor in boosting energy efficiency is viewing overall needs through a supply chain lens. By analyzing data across the supply chain, operators can uncover hidden inefficiencies from isolated processes to reduce energy consumption without impacting output. To revisit our smelting example, real-time monitoring can identify unnecessary energy use—such as heating when no material is being processed—to allow for energy-saving adjustments.
This is where advanced co-simulation tools such as ETAP Transient Stability and AVEVA Dynamic Solution shine. By running simulations, companies can:
- Perform feasibility studies
- Analyze current conditions (e.g., electrical load, process efficiency, or equipment health)
- Answer operational questions by modeling both power and process interactions—such as how switching from gas to electric smelters impacts equipment and energy needs
- Determine if they have the necessary infrastructure or need upgrades
- Identify improvement areas before investing in infrastructure or upgrades
Moreover, co-simulation models can evolve into digital twins, which provide ongoing operational benefits throughout the plant’s lifecycle, from commissioning to operator training.
Gaining enterprise-wide visibility for better production control
For large-scale metal processing operations, a centralized, enterprise-wide view is essential for navigating the complexity of daily production fluctuations—shifts in energy demand, equipment performance, or external supply chain pressures. Converging engineering, operations, and other data in context provides a comprehensive enterprise-wide view. This allows operations managers to monitor and optimize production in real time across multiple sites.
For example, Nutrien, one of North America’s leading agrichemical businesses, uses AVEVA™ Unified Operations Center to integrate live plant data from their nitrogen and phosphate production facilities. By combining insights from the AVEVA PI System with the UOC, Nutrien teams can troubleshoot operational challenges and optimize performance across multiple sites. This enhanced visibility enables them to anticipate and resolve issues before they impact production, streamlining operations and improving team collaboration.
With market conditions constantly in flux, this overview becomes a powerful tool for:
- Staying ahead of supply chain disruptions
- Managing production schedules
- Adjusting energy use across the entire operation
The metals industry has been a leader in adopting this technology due to its decentralized operations and need to monitor production across distributed sites.
The shift to electrification and sustainability
One of the most significant trends in metal processing is the transition from fossil fuel-fired smelters to electric-fired ones, which are more sustainable and have precise energy control to avoid waste. Data analytics helps operators maintain optimal energy use, avoiding over- or under-utilization and minimizing waste while allowing equipment to operate at peak performance.
Emerging technologies that enable new efficiencies
A suite of emerging technologies is making these changes possible. Artificial intelligence (AI) driven systems and advanced sensors provide the granular data needed to optimize energy use. Meanwhile, predictive analytics and machine learning (ML) help plants reduce downtime and identify inefficiencies before they become significant problems. Additionally, these technologies can be embedded within controls strategies using EcoStruxure Automation Expert.
For example, using EcoStruxure Automation Expert in a plant with 20 different process areas, applications such as Video Analytics can be embedded with a group of controllers and I/O cards in an environment that’s simple to interact with and seamlessly integrated.
Interfacing with AI and machine learning becomes a natural extension of the system. Combining EcoStruxure Power and Process with EcoStruxure Automation Expert makes energy efficiency in metals processing easier, particularly in critical processes like smelting, casting, temperature control, and other heating operations.
A path forward for metal processing
Optimize your metal processing operations with real-time data-driven insights, energy efficiency, and improved production control. Discover how EcoStruxure™ Power and Process and EcoStruxure Automation Expert work together to streamline your processes.
Add a comment