As the stewards of a company’s buildings throughout their lifecycles, facility managers are essential in incorporating sustainability strategies into operations. They are responsible for keeping all building systems and operations functional, ensuring occupant comfort, and monitoring space and workplace usage. In other words, they are the gatekeepers of performance data required to understand current operation baselines and track the effectiveness of future upgrades.
As our world changes, sustainability has become an essential strategic objective for today’s leading corporations. Now, more than ever, they are working to measure and improve their energy and sustainability performance. This is clearly demonstrated by the 98% of S&P 500 companies that publish sustainability reports.
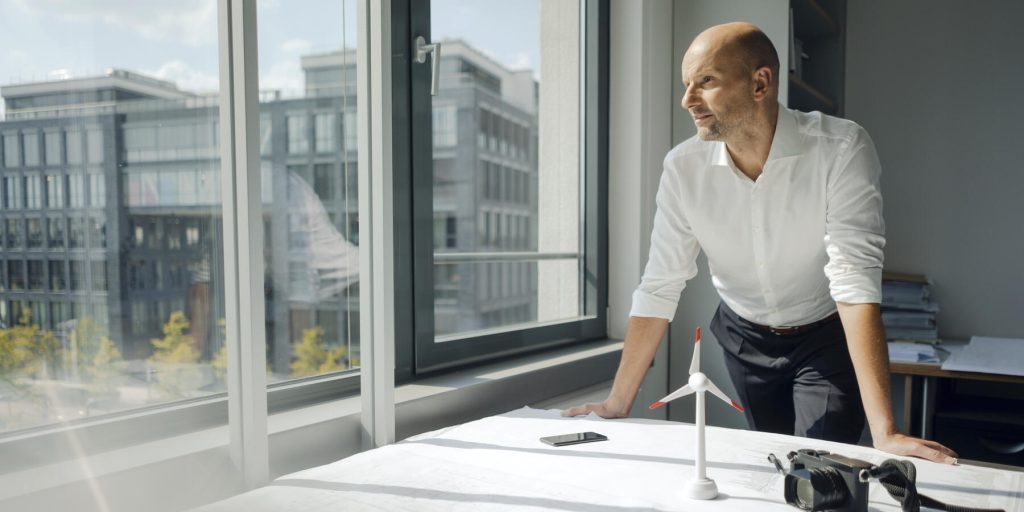
A company’s buildings offer an opportunity to boost environmental and financial performance. Buildings are responsible for ~40% of global energy consumption and 33% of greenhouse gas emissions, creating a logical opportunity for improved environmental performance strategies. Sustainability efforts must be authentic to be effective. This vision must be a cornerstone throughout the company’s culture, values, and risk management.
We need to ask how we move from the strategic and intended to the practical, day-to-day operation that will drive change. By leveraging technologies like environmental sustainability monitoring software and integrations with building and power management systems, facility managers can actively support the operational and reporting requirements to advance their organization’s sustainability goals. Today, this data type is often stored in a single software platform, such as an Integrated Workplace Management System (IWMS). Data collected and managed in an IWMS typically includes physical, operational, and financial details about a building, its spaces, assets, equipment, waste management, organizational units, and people. These are the very same elements that impact key sustainability improvement areas.
Integrated technology delivers six key sustainability benefits
- Improved workplace quality and efficiency – For sustainability reporting requirements, IWMS systems play a critical role in documenting workplace usage, preferences in workplace layouts such as collaborative vs. private, ideal interior temperature conditions, and other factors that typically impact employee well-being.
- Intelligence driven operations – Connected systems can allow influenced changes based on clear business rules. This process leads to intelligence driven operational changes aimed at reducing carbon and improving experience.
- Reduced commercial real estate expenses – An IWMS can track home office locations and related resources to determine whether hybrid work has saved resources, such as less electricity, or just shifted their use.
- Mitigated ESG-related risks – Facility managers can better protect against facility-related ESG risks through well-documented processes, accurate and current data, and strategically placed alarms and notifications. For example, these measures are supported by connecting an operational system (e.g., BMS) to an IWMS to provide real-time data.
- Accurate reporting and disclosures – Building management data provides crucial insight into resource consumption and emissions. An IWMS helps augment non-financial disclosure data for ESG reporting by tracking the percentage of the workforce working from home, employee commuting, use of renewable energy, product procurement, and disposal, etc.
- Smarter maintenance – A strong maintenance program provides two sustainability benefits. Extending equipment lifespan reduces material waste and traffic to the landfill, while lower operating costs are often a result of reduced energy usage.
Putting the data to work
One American furniture manufacturing customer used integrated data monitoring and transparency solutions to reduce energy consumption across nine sites drastically. Their goal was to leverage centralized data better to help transform it into a more sustainable organization.
To minimize waste, they selected EcoStruxure Resource Advisor for precision monitoring and tracking manufacturing and operating processes. It provided actionable insights to identify opportunities for better data sharing and transparency data across the organization. This improved collaboration and increased data visibility helped them achieve a:
- 27% reduction in manufacturing energy consumption vs. the past decade
- 97% reuse, recycle, or reutilization of manufacturing waste, attaining zero waste to landfill status at nine of their sites so far
Learn more
This is just one example of how facility managers can become leaders in the move toward net-zero building operations. To start your company on its data-driven sustainability journey, check out our new eBook, ‘Facility Management and Sustainability, a Fundamental Alliance,” and explore our software for sustainability and efficiency portal.
Add a comment