It’s time for all medium and low voltage business stakeholders to address their carbon footprint.
Today, electrical equipment manufacturers, contractors, panel builders, specifiers, and end users are taking the carbon footprint of their production lines and projects more seriously than ever. Indeed, striving for net-zero operations no longer is an afterthought; it is an integral part of business strategy. For medium- and low-voltage equipment, this commitment means prioritizing a circular economy approach and sustainable equipment design that supports a low-carbon future. These sustainability improvements must also meet the UN’s sustainable development goals, and they will have a direct impact on U.S. businesses that must meet Corporate Sustainability Reporting Directive (CSRD) requirements in the coming years.
Innovative technology is essential for designing greener MV and LV equipment
Stronger decarbonization efforts can be successful only by adopting a circular economy approach that focuses on the entire lifecycle of medium-voltage and low-voltage equipment. What does this mean? The circular economy concentrates on reducing the environmental impact of products, services, and systems. It focuses on extending equipment’s useful life, reducing emissions and energy recovery, and promoting circular flows of materials.
Designing greener medium- and low-voltage equipment starts with a global value management approach that identifies which customers’ needs must be satisfied. This approach also identifies the needs of all stakeholders who are involved over the life cycle to determine the best way to minimize resource use (See standardized definition of value, p.78). This method is one of the best ways to design environmentally conscious products.
Manufacturers, panel builders, installers, and contractors can focus on maximizing the near- and long-term sustainability outcomes of medium- and low-voltage installations. How? By using digital and connected ecosystems technology when designing and installing equipment or systems, such as medium- and low-voltage switchboards, transformers, and relays. Fortunately, advancements in digital technology are accelerating as fast as sustainability efforts.
Specifically, the introduction of digital twins more than a decade ago has been transformative for specifiers who are designing medium- and low-voltage switchgear with sustainability objectives in mind. In a nutshell, a digital twin is a data-made replica of a physical system or equipment, allowing panel builders to gain a realistic view and performance of the switchgear over its whole life cycle. That means the design and building stages can be finetuned to meet sustainability KPIs before the physical equipment is brought to life.
Download our free MV technical guide to learn how you can design more sustainable MV installations.
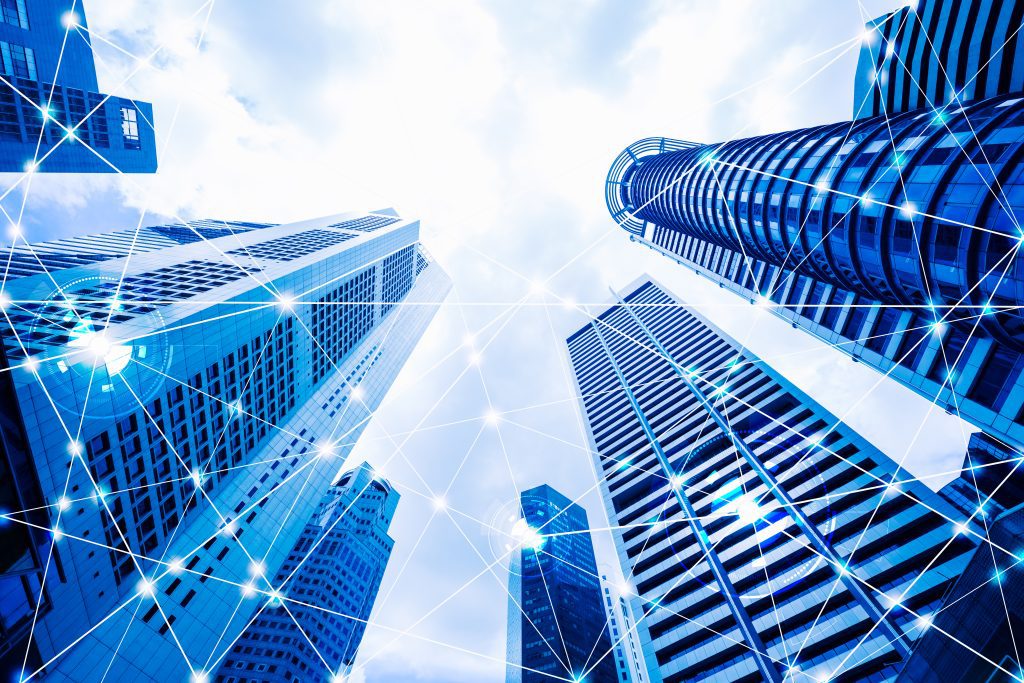
Data is the foundation of a green design
Many circular economy initiatives are launched and focused on the end goal, i.e., the highest level of analytics and methods (the engine) that deliver maximum benefits for stakeholders and electrical equipment users. Initiatives should also prioritize data, however. Data and, more important, the actionable insights robust data models can yield, is the foundation of any digitization plan. For example, data can be leveraged during the design stage to determine how durable the final installation will be based on information that is collected from connected equipment and devices. This visibility, enabled by the digital twin, ensures the final installation will meet each end user’s specific values and needs.
For a digital twin to be effective, though, a strong, clear data strategy must first be in place. As part of that strategy, including data governance, data management allows stakeholders to anticipate decisions or actions to design more efficient, sustainable systems. This capability is possible because data is used to help stakeholders see and understand information that may otherwise be intangible (e.g., system overload, wear, and malfunctions). The data is defined by IEC technical committees in relation to the market needs. The data (from assets), once structured to form trustworthy and accurate digital twins, becomes a living, breathing replica of the engine’s fuel control systems.
An example of digital data is the data needed to define product durability under normal conditions of use. During life cycle analysis, the reference service life is defined under a set of normal environmental and operational conditions. These “normal conditions” are defined by manufacturers. The data is collected using connected devices such as sensors in medium=voltage and low-voltage equipment. Stakeholders such as panel builders then can analyze the data to determine how to support lifetime extension, as well as future secondhand product and parts usage. These condition-based monitoring and material circularities are useful for assessing residual durability, meaning the ability of material, parts, and products to withstand future usages. The residual durability can vary from 0% to x%, depending on the previous life cycle and associated conditions.
How digital twins optimize MV and LV equipment’s design and performance
Digital twins are a good example of how technology enables environmentally conscious design. Since digital twin models are digital representations of a physical device or system in their circular environments, they play an important role in decarbonizing equipment and systems. That’s because giving data value at all steps of the product life (and project) enhances service life efficiency.
During the design stage, for instance, the digital twins are used to build and update a virtual model. Input simulates each step of the project on a single platform, such as equipment’s mechanical, electrical, thermal, and environmental properties. Digital twins provide a risk-free way to analyze, test, and experiment with different design scenarios, processes, equipment, and operations before making any changes to the physical asset’s design. They answer common “What if?” scenarios, allowing designers to make adjustments before the equipment rolls out of production.
For example, when design is based on a functional analysis that reviews all functions needed over the whole life cycle, it will be obvious to stakeholders (e.g., specifiers, end users, contractors, or those using the digital properties, such as designers) how they can extract associated digital properties of this equipment both individually or when integrated in a system. The following figure is a classification of digital properties that can be automated—an important value driver for building digital twins for electrical equipment.
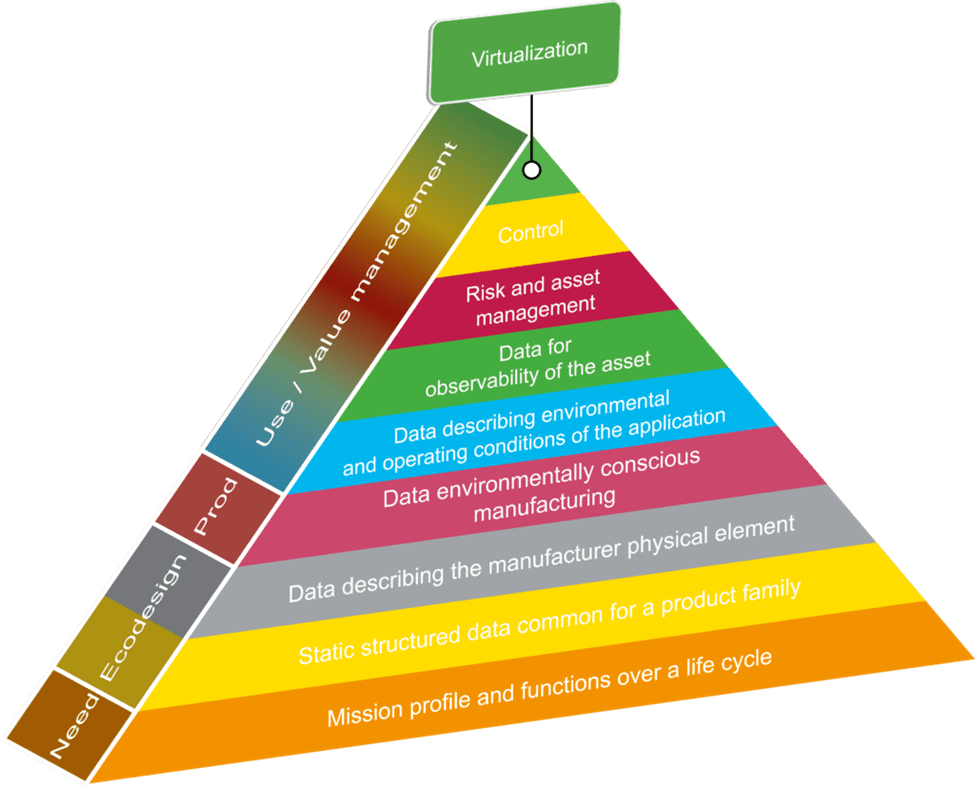
For example, an electrical system digital twin analyzes the process impact and proposes the most adapted architecture. And, if relevant, the electrical system digital twin proposes an optimized power generation combination. In turn, it can identify how to maximize decarbonization by minimizing energy use.
Digital twins are also used for building information modeling (BIM), which is used for designing infrastructures. For BIM use cases, digital twins can apply mechanical representations while other aspects such as electrical, thermal, or control models are necessary. Many existing models, such as IEC 61850 or common information model (CIM), are used and recognized as interoperable to accompany smart grids in their transformation.
Learn how our innovative design eliminates SF6 use in MV switchgear
While SF6-free MV switchgear is driving mature circular economy efforts across the European Union, it nevertheless is an imperative future-state consideration for all switchgear designed for U.S. end users. That’s because zero-waste-to-landfill and responsible end-of-life considerations are driving future-thinking initiatives among innovative specifiers. One example of how an environmentally conscious design based on technology creates a greener product involves designing MV switchgear by using only pure air and vacuum technology for breaking and insulation—instead of using the greenhouse gas SF6. For example, the electric distribution utility EEC Engie is using SF6-free MV switchgear to reduce the utility’s carbon footprint while maintaining the same level of safety, the same footprint, and minimizing changes to operations. Today, U.S.-based specifiers can stand out by future-proofing their designs.
Ready to build digital twins?
Get started with our Eco Consult Electrical Digital Twin Service offer to digitize the customer single line diagram with ETAP software and provide ongoing model maintenance support in a recurring model. Learn more about how to step-up OpEx savings with Electrical Digital Twin Service to improve safety, reduce downtime, and meet regulatory requirements by simply having your digitized electrical system architecture available and updated.
Add a comment