This audio was created using Microsoft Azure Speech Services
Often, large motors go unnoticed — until they stop operating. Downtime can mean reduced output, lost revenue, unplanned costs, and inconvenience to customers. The design of the motor switching and protection schemes plays a large part in how the equipment addresses issues and recovers from downtime.
Motor controls and protection design also impact the initial cost of the equipment, even more so for larger motors. These costs impact materials, build time, and commissioning.
In this blog post, we’ll explore five things control panel design engineers and specifiers should know about switching and protecting large motors and why it can help reduce downtime and costs.

1. Select and size your motor starters properly
There are different types of motor controllers and motor protection forms. The simplest form involves a motor starter (a contactor plus an overload relay), where the contactor applies the full voltage of the supply circuit to the motor when operated. Some systems require a phased start due to the mechanical impact on the system or the delicacy of the loads being moved. In these cases, where care must be applied during the starting phase, a multi-speed or Wye-Delta starter scheme (consisting of several contactors/overload relays) or a soft starter may be used to ramp up the start of the motor. Some applications require the ability to adjust or regulate the speed of the motor to set the pace of the equipment or reduce energy consumption. In these cases, it’s best to use an adjustable frequency drive.
Sizing a contactor for a large motor is fairly simple for most applications in the U.S. Whether using an International Electrotechnical Commission type or NEMA type starter, the contactor or starter is sized based on the motor horsepower rating and voltage. The next factor is the coil voltage, which is often different than the motor voltage. Typically, the voltage in the control circuit is 120 volts alternating current (VAC). Twenty-four volts direct current (VDC) is often used in equipment that has a programmable logic controller (PLC) or other electronic devices that operate at that voltage. Control voltages may sometimes be the same as the motor voltage in cases where the equipment motor(s) operates on a single-phase voltage or in commercial equipment applications using 240 VAC or less.
When using an overload relay, several considerations factor into which type you use, including, but not limited to:
- Communication or data needs
- Trip class (i.e., how sensitive the trip response should be)
- Sensitivity to ground fault
- Sensitivity to phase imbalance
When sizing overload protection, the protection should be sized no larger than 115% of the motor full load amps (FLA) in most cases. This likely raises the question, “How is the overload protection sized in the design phase before the motor FLA is known?” It’s not unusual for the motor selection to be determined after the panel is designed or even built. However, both the National Electrical Code (NEC) and Underwriters Laboratories (UL) provide motor FLA tables that design engineers use to select their overload protection devices.
Additionally, many overload protection devices are designed to trip at 115% of the amp size on the setting dial. This makes selection much easier for design engineers when applying sizing requirements.
Overload protection devices typically have a range of currents that can be set to a specific level. Because the actual motor FLA may be a little higher or lower than the design FLA, it’s a good idea to select an overload device with a range that allows some room to increase or decrease as needed once the motor is in place.
Sizing motor controllers and motor protection for other situations can be somewhat more involved or have specific rules. It’s always a good idea to consult an experienced expert in codes and standards and the specific motor/load application.
2. Use motor protective circuit breakers the right way
All motor circuits need an overcurrent protective device to protect against short circuits. Historically, this was done using fuses or a circuit breaker for larger motors. Ideally, a fuse or circuit breaker could do the job of both short-circuit protection and motor-overload protection. If you attempt to size a circuit breaker or fuse to align with the motor FLA, odds are the circuit protection opened the circuit during motor startup. Motors have a high inrush, so breakers are often sized up to 250% of the motor FLA, and fuses are sized between 175% and 300% depending on the fuse type.
Because the breaker/fuse has to be sized to account for the motor inrush, a separate overload relay device is needed to protect the motor from overload. Wouldn’t it be great if a single circuit breaker device could protect at the short-circuit, motor inrush, and motor overload range? Well, that does exist. It is called a motor protective circuit breaker (MPCB).
MPCBs are UL 489 rated like a molded-case circuit breaker, but they are also tested and rated under UL 489 Supplement SH, which tests the breaker for use as a motor overload protective device. MPCBs are different from standard circuit breakers in that they include a motor overload current dial, similar to an overload relay device. Some MPCBs also have selectable features such as trip class and ground fault.
Why use an MPCB?
- Fewer devices save panel space.
- Fewer devices take less time to wire.
- Most MPCBs have a large overload adjustment range, simplifying inventory.
- Overload trip reset options: Some MPCBs have pre-trip alarms that can be wired to open the contactor instead of tripping the MPCB (or the overload relay in the traditional approach). This can be beneficial where manual resetting is difficult to accomplish. It gives the option to reset (or restart) the unit from a more convenient location.
- Interaction through mobile device: Some MPCBs can wirelessly communicate with mobile devices, allowing users to view fault history and adjust protection settings.
When using an MPCB may not make sense:
- MPCBs are typically the size of a molded-case circuit breaker, which may require more width on circuits for 40 HP and less. Typically, MPCBs are used above 40 HP.
- MPCBs use an electronic trip unit, which has a higher cost than thermal-magnetic molded-case circuit breakers. However, the MPCB takes the place of a molded-case circuit breaker and overload relay, so this may not result in a higher material cost.

3. Avoid large control transformers
Large contactors have larger coils than smaller-sized contactors. This traditionally means a larger transformer is needed, and a power supply may be so large that it becomes cost prohibitive. If PLCs are used in signaling the contactor operation, an interposing relay is needed to protect the PLC IO from coil surges.
New coil technology provides an additional way to construct coil control that saves material costs and wiring. A PLC input on the contactor coil allows the coil to be powered using the motor voltage, while receiving the operation signal direct from the PLC, without an interposing relay necessary. This not only simplifies control wiring, but also eliminates the need for a large transformer.
4. Know your short-circuit current rating
Code requires the control panel be marked with a short-circuit current rating (SCCR), and that the panel SCCR be sufficient for the available short-circuit current (also referred to as available fault current) where the control panel is installed. Determining the control panel SCCR can be complex. An over-simplified explanation uses a weakest-link approach based on the component SCCRs of the devices in the power circuit according to UL 508A.
The SCCR of the contactor and overload relays are typically marked on the product label or instruction manual. The rating specifies the SCCR level (kA) based on the voltage and the required overcurrent protective device.
What to watch out for regarding large motor contactor and overload relay SCCR:
- Is the required breaker size large enough? It can be difficult to pass an SCCR device test using larger circuit breakers. Essentially, the larger the breaker, the higher the potential for let-through current, making it more difficult for the contactor during the short-circuit test. As a result, it’s common to see large motor contactor SCCRs that require a breaker size that is too small for the motor inrush. This results in a bump up to a larger contactor with a higher permissible breaker size, taking more space in the panel and adding more cost.
- Delta or Wye voltage? Some device SCCRs are approved for 480 Y/277 V, instead of 480 V delta. If the voltage supply is 480V delta, then an SCCR rated at 480 Y/277 V cannot be used. However, a 480 V delta-rated SCCR can be used for either 480 Y/277 V or 480 V delta.

5. Maintain contact tips to avoid downtime
Given that most large motors are doing serious work, unexpected downtime can have significant consequences. Several factors can impact the contactor’s performance, lifespan, or both. One of these factors relates to the coil’s operation in adverse power conditions. With the strain on electrical grids, you commonly see a drop or rise in voltage that is feeding the contactor coil. Newer coil technology can increase the acceptable voltage range, making these conditions more forgivable.
Another issue relates to maintaining contactors in operation. As the contacts close, the contact tips experience high inrush current, which results in wear over time. Eventually, these contacts must be replaced. Often, people don’t realize this until the contactor can no longer effectively close the circuit to the motor. Then it becomes a race to either source and replace the contacts or swap out the contactor with one in reserve. However, Schneider Electric™ has developed a patented algorithm for the TeSys™ Giga contactors that identifies when 15% of usable contact life remains. The contactor diagnostic LED indicator informs maintenance when it reaches this point.
Power quality doesn’t plague only the contactor coil. It also affects the overload relay, which can result in nuisance tripping. Protection against phase imbalance is commonly included in larger overload relays. Some conditions, such as remote locations or circuits with loading that are not effectively balanced, are more prone to experience phase imbalance. This can be particularly true in oil and gas applications and agriculture. Some motors are capable of dealing with these more rugged environments, and the phase imbalance protection on overload relays can become a nuisance. If this applies, be sure to consider overload relays with the option to turn off phase imbalance. The TeSys Giga overload relay by Schneider Electric includes this feature.
New solutions for old problems
So there you have it. These five ways to operate smarter make a big difference — from design and build to operation and maintenance. Schneider Electric leads the market in innovative motor control solutions that help equipment manufacturers and panel builders succeed. The latest motor control solution for large motors, TeSys Giga, brings new solutions to old problems — including the five topics I cover here.
Scan the QR code below to learn more about TeSys Giga motor starters and connect with a knowledgeable sales representative.
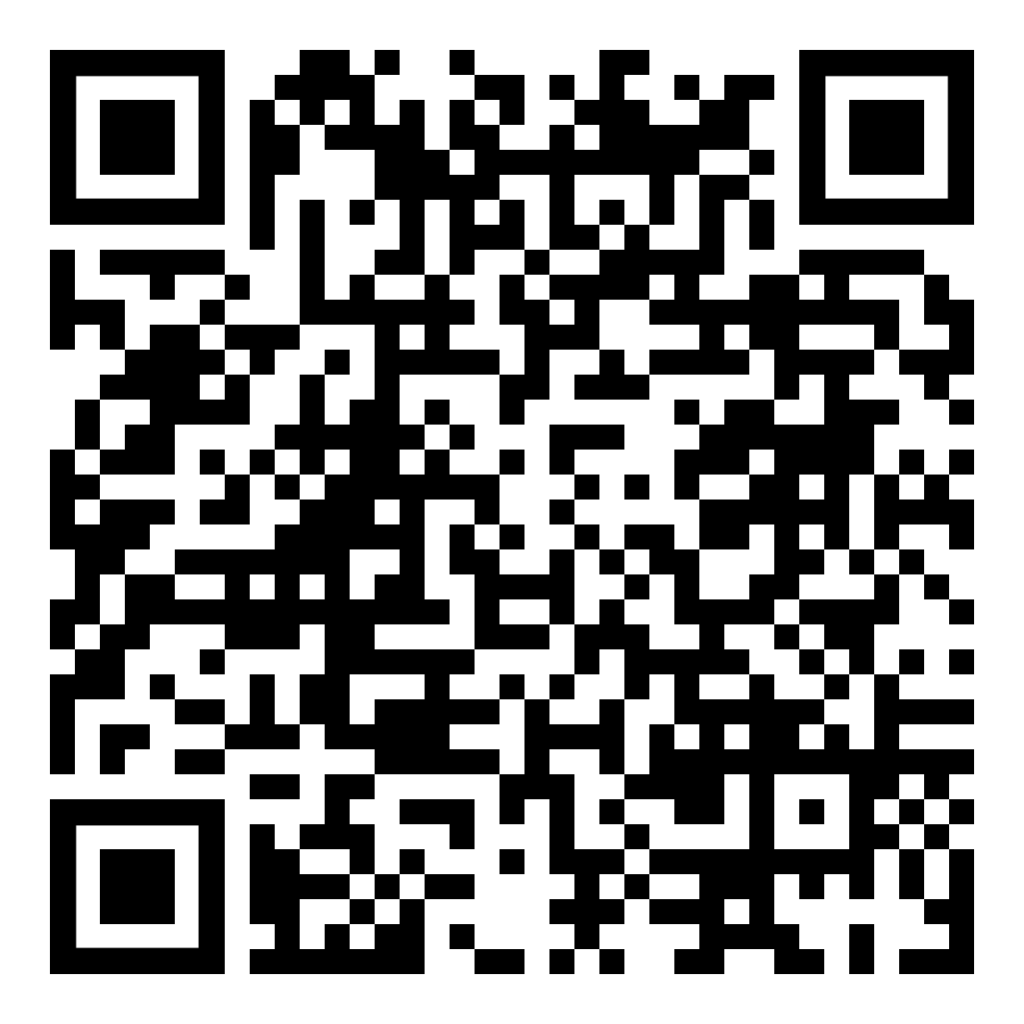
Add a comment