Ammonia is one of the key drivers of the industrial energy transition. The ammonia produced in the future will be used as a decarbonization tool to reduce CO2 emissions and global dependency on fossil fuels.
Today, CO2 emissions are growing. In 2021, carbon emissions equated to 36.3 gigatons, an increase of 6% from the year before. Additionally, the global economy is vulnerable to unstable supply chains and resource extraction. To combat all these issues, green and blue energy, circular economy, and operational resilience will be key components to a sustainable energy future for the chemical industry.
Ammonia is a key player to create green and blue energy. The viability of green and blue ammonia projects depends on carbon tax laws and government incentive programs and its demand is driven by companies’ sustainability goals. The key drivers for green ammonia are availability of renewable energy, sustainability, cost of electrolysis technologies and regionalized small-scale production. The availability of natural gas, CCUS infrastructure, lower CAPEX and large-scale production facilities are the key drivers for blue ammonia.
With ammonia demand on the rise, Schneider Electric is leading the sustainability journey with a new paradigm of energy efficiency, process electrification, exciting innovations in automation and adoption of digital technology as an enabler.
A physical asset is brought to life through the energy supplied to it. We drive this asset in the right direction through automation and add intelligence to the asset through software such as those for predictive analytics and optimization. Addressing sustainability is not a trivial challenge and will require a combined application of these three components (energy, automation, and software) to achieve our goal.
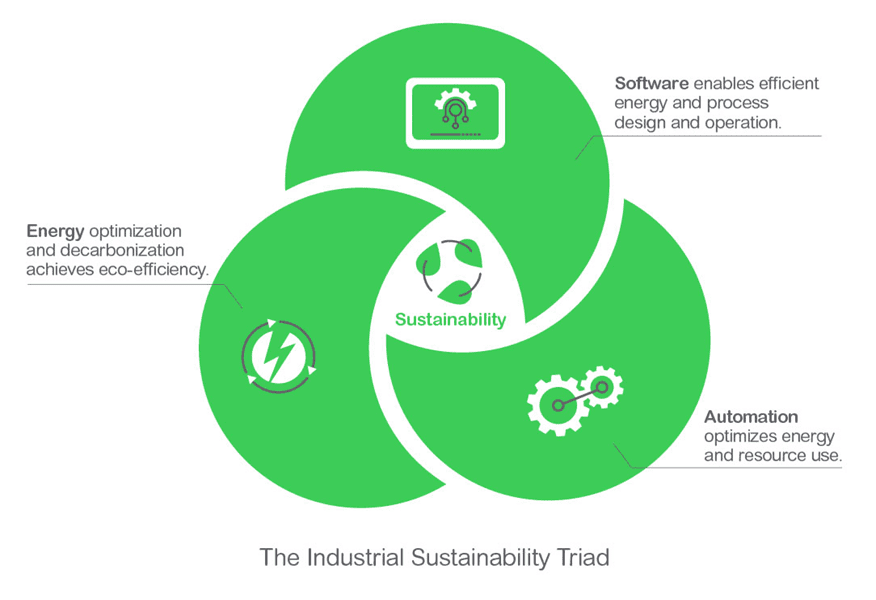
Transformation of the industry for more sustainability
Ammonia projects are growing significantly in North America where, over the next two years, more than $10 billion will be invested in grassroots projects. Sustainability goals can be significantly boosted by implementing technology solutions during early engineering phase, and CapEx/OpEx can be optimized by electrifying the ammonia reformer and rotating equipment.
Digital tools can be implemented to monitor sustainable performance KPIs with dedicated dashboards to report to the key stakeholders. That’s why we are always driving solutions that enhance operations and assets by integrating simulation into engineering to optimize energy efficiency and process automation.
Integrating the simulation of power and process systems during the engineering phase of the project lifecycle leads to designs which are optimized for embedded C02 emission, energy consumption, and sustainability. Solutions like ETAP and AVEVA Process Simulation tools can be deployed in this integrated way to achieve such optimization. This approach also improves and streamlines activities related to commissioning and start-up, accelerating the time to target production and revenue. EcoStruxure™ Power & Process – which deploys a unified, single team execution approach – can help deliver a 20% reduction in CapEx associated with electrical, instrumentation, and controls scope.
Constant monitoring is required to ensure plants operate within acceptable parameters, but these parameters are increasingly complex and interrelated. It is of limited value to optimize energy consumption without considering production or to maximize revenue without understanding the impact on emissions.
Platforms are required to aggregate real-time and historized operational data from multiple systems and deliver them in a unified environment for visibility, collaboration, and analysis. AVEVA’s Pi, Data Hub and Unified Operations Center solutions provide such capability. Deploying them in combination – with other enablers such as AI and critical edge solutions – can help ensure an ammonia plant is operating within its sweet spot: reliable, verify low emissions (if any), and minimizing OpEx while maximizing production and revenue.
This is particularly true in the case of an ammonia plant drawing power from a variety of sources, a situation involving constant balancing and detailed, verifiable reporting. In such scenarios, the solutions mentioned above enable near real-time sustainability performance reporting in a configurable, KPI-driven visualized dashboard.
Critical management components for the ammonia market
Bolstering an ammonia plant with the holistic, multi-faceted, lifecycle capabilities described above requires a complete approach to the digital twin. More than a 3D rendering of the physical assets, this is a living, near real-time accurate model of the plant and its behavior – including the electrical network bringing power from utilities or other sources. This enables insight into the various factors impacting operational performance; connects the plant floor, control room and back office; breaks lifecycle and functional siloes; and it serves as a simulation environment to optimize decisions across engineering, operations, and maintenance.
Ammonia’s role in a successful global energy transition is set to expand massively in the decades to come. Deploying the energy-automation-software triad technology strategies early in the lifecycle as this industry grows will help ensure society and business reap the maximum benefit.
To learn more about the triad approach, visit our EcoStruxure Power & Process page.