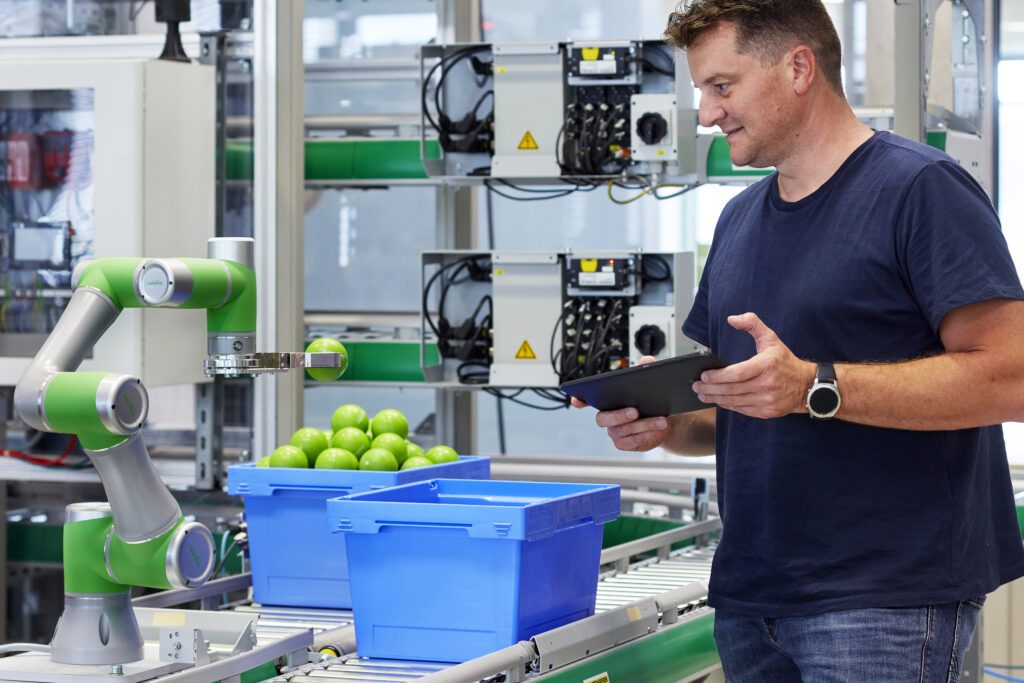
These days, global manufacturers are experiencing labor shortages like never before. According to leading human resources firm Randstad, by 2030 employers will face an estimated shortage of 85 million workers across the globe. For industrial operations to keep running, a robotic solution that supplements human labor could be the key to business continuity.
However, introducing this approach to automation raises questions for many in the industry. Plant owners are concerned with the upfront cost and how the deployment of robots will impact their facilities, while workers question how their jobs will be affected.
The good news is that much has evolved over recent years in the field of robotics. Innovative technologies such as collaborative robots (cobots) and digital twins make robotic implementations easier and more affordable.
Why consider robots?
According to Precedence Research, the 2022 robotics market size of $89 billion is expected to grow to $225 billion by 2030. This growth is driven by:
- Attractive Returns On Investment (ROI) – Market trends and digital innovation now make 18-24-month ROIs possible. By their nature robot solutions tend to be more flexible. They can often be simply reprogrammed for different process operations so robots can be deployed in various applications during their lifetime. Embedded safety features help to reduce equipment footprint. This simplifies deployment and cuts costs. Robots also enable shifts to 24 x 7 ‘lights out’ operation, allowing existing capital equipment to work for a greater portion of each 24hr period and at a time when utility costs are often lower.
- New levels of agility – Customer demand is driving the trend toward mass customization, and this implies the need for increasingly agile operations. Robots and cobots are proving effective at not just customizing for specific markets but also for individual customers. Robots enable high-mix production through quick changes of machine fixtures for easy and fast adaptation. New vision systems allow greater flexibility by “looking” at the environment and adjusting operations, selecting the right modular parts at the right time to execute the required tasks. The new generation of robots is also mobile and can integrate across multiple machines and operations. In distribution centers, for example, automated guided vehicles (AGVs) act as mobile material handling and load-carrying systems that travel autonomously throughout a facility without an onboard operator or driver.
- Help to address acute labor shortages – Robots are not replacing humans, they’re becoming their co-workers. This creates new opportunities for staff to focus on higher-value tasks, resulting in increased job satisfaction. Today, a robotic solution would be designed to work alongside people to do tedious, repetitive, physically taxing jobs and allow humans to spend more time on other higher value-add work. The resulting job enrichment helps with employee retention. Robots can also help alleviate worker shortages and reduce the costs of finding, training, and retaining new employees.
- Sustainability – Robotics support the ‘3 Ps’ of the ‘Triple Bottom Line’: Profit (with the consistency of production), People (increased staff safety, higher value tasks, and job satisfaction), and Planet (helping to recycle, fewer errors/ decreased waste in manufacturing)
- Efficient use of industrial floorspace – Robots can make more efficient use of floor space. Because of their design, some robots can take advantage of unused vertical space in manufacturing facilities. Better use of vertical space frees up more floor space for extra equipment and storage
Best practices for robotics design and deployment
Organizations that decide to invest in a robotic solution should consider the following important steps to lower their risk and maximize their probability of success:
- Secure comprehensive stakeholder support – It’s important to include plant floor operators as well as other key stakeholders such as IT staff (who are responsible for connecting systems and extracting data), and plant safety in your project planning.
- Define success – Clearly define the production problem to be addressed and establish quantifiable objectives to measure success.
- Define failure – Perform the necessary analysis to project what could go wrong and how to avoid costly mistakes.
- Establish a specific budget and define desired ROI– Include factors such as the cost of downtime to install the new solution, the cost to maintain manual processes in parallel with the new systems, etc. It is also important to share financial constraints with those responsible for integrating the new system.
- Information gathering – A deep understanding of the processes involved is critical to project success and making sure the solution deployed succeeds in solving the production problem originally identified.
A strong partner ecosystem helps lower project risk
The successful implementation of any robotic solution relies on an ecosystem of partners, all of which have an essential role in assuring proper integration. That ecosystem includes end users, OEMs, robot integrators, and technology providers, like Schneider Electric. It’s important to align with organizations that have expertise in the operation’s production and processes and who can advise on what works best across the design, commissioning, operation, and maintenance phases.
Besides offering a wide array of delta robots, cartesian robots, and cobots, Schneider Electric provides innovative smart conveying solutions like the multi-carrier transport system which helps to maximize equipment performance. Open engineering frameworks accompanied by digital twin –and teams of experts in specific application and technical areas speed up the design of robot applications. Customer-specific adaptations can be provided by FlexCenter. Our robotics solutions are part of the EcoStruxure platform, IoT-enabled, open, and integrate well with any industrial company’s digitization initiatives. With digital twins, robot designs can be tested and optimized before they are built. Emulation of these systems before they are built in the real world greatly reduces commissioning time and downstream implementation cost, and the work involved in developing digital twins is directly portable to the rollout of the actual physical solution.
For more information
To learn more about how machine builders (OEMs) and integrators drive efficiencies in a future world of robots download our e-guide, Unlocking the potential of industrial robotics.