This audio was created using Microsoft Azure Speech Services
Author: Schneider Electric Industrial Automation
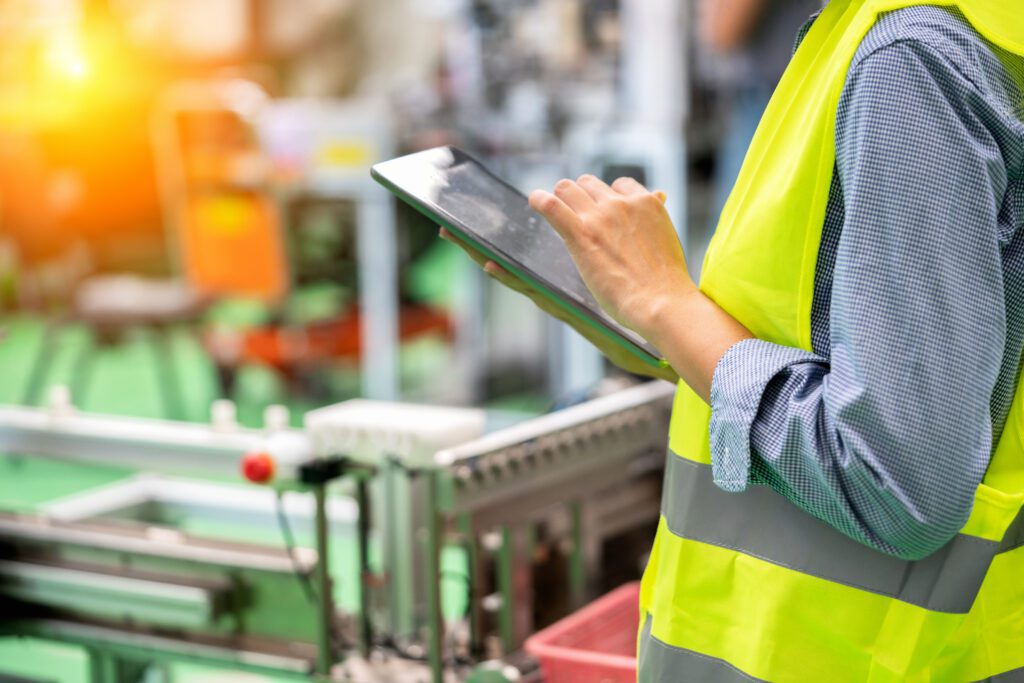
As sustainability continues to gain attention in industrial markets and, as the previous post explained, investment also increases, more stakeholders are also starting to understand that process and plant optimization results in cost savings and increased profitability while also achieving sustainability goals. These insights drive manufacturing companies to invest in technologies and solutions that improve their operational sustainability and overall environmental footprint.
A recent survey and report by Omdia, identified that more than half of respondents are working on environmental management projects. While most said they will deploy energy management and renewable energy systems within three years, there is concern that many of these systems sit within different departments.
This concern underscores the need for a common digital thread across industrial organizations to be able to create the ability to analyze relevant data. Viewing systems datasets holistically helps with informed decision-making and prioritizing investments in potential sustainability projects.
Technologies that impact manufacturing sustainability goals
The survey highlighted several technologies that will have the most significant impact on manufacturing sustainability goals, including:
- Sensing
- Internet of things (IIoT)
- Artificial intelligence (AI)
- Digital twin
- Cloud, supply chain management software
- Energy management systems
While some of these solutions are still emerging in the manufacturing sector, some respondents have already deployed them to gain cost savings and ensure operational resiliency.
Smarter automation, efficient energy management, and the cloud
Upgrading inefficient equipment requires a strategic approach, and the results should directly reduce a company’s energy consumption and overall total cost of ownership. Nearly half the respondents indicated that more efficient automation (i.e., motor drives and higher-efficiency motors), energy management systems, and cloud solutions would impact their sustainability initiatives the most. Forty-five percent further recognize that legacy assets can be a challenge to optimizing processes and more efficient automation.
The primary function of energy management systems is utility bill management; however, more than a third will use them for energy, carbon, and greenhouse gas emission reporting and certification within three years. Some even utilize integrated technology solutions like EcoStruxure Resource Advisor to report on all three today.
Using the cloud to gather and collect data from all operational processes and edge locations onto a central platform has significant benefits, including increased visibility, equipment optimization, and overall project management effectiveness. Aggregating plant-wide data with increased connectivity enables thorough analytics and informed decision-making. Leading industrial organizations are already taking advantage of industry-specific cloud solutions like AVEVA Data Hub and AVEVA Connect.
Increasing supply chain visibility with more sensors and analytics
A manufacturing organization’s ability to optimize operations relies heavily on its’ capability to manage its supply chain. Industrial sustainability inherently depends on increased connectivity and data gathered by various sensors within the plants’ processes. When aggregated, this data gives organizations the necessary visibility to make intelligent decisions directly affecting their operational success. The accumulation of data allows various analytics to be performed, from basic identification of threshold limits to machine learning and deep learning algorithms. Scalable technologies like EcoStruxure Traceability Advisor and the AVEVA Unified Supply Chain solution enable holistic views of various industrial organizations.
Designing for the future while preparing for today
Digital twins replicate a design or setup and then simulate it under various situations, conditions, and scenarios. This allows advanced planning and strategic thinking to impact current processes and future developments. With climate change reinforcing the importance of industrial resilience, EcoStruxure Machine Expert Twin and AVEVA Process Simulation enable manufacturing companies to build resiliency into their operations.
To learn more about the technology and solutions available to help deploy your organization’s sustainability programs and the current state of industrial sustainability, please download the latest research report, Industrial Sustainability: Moving Sustainability Forward in Manufacturing.
Add a comment