This audio was created using Microsoft Azure Speech Services
By Craig Resnick
This year’s “Key Technology Trends” report was influenced by the combination of continued supply chain issues, worker shortages, high inflation, geo-political conflicts, and the lingering effects of the COVID-19 pandemic in certain geographies. It was a year when industrial markets, despite slower growth, declines in stock valuations, and fears of recession, did not typically suffer from demand problems but were often impacted by supply chain issues and the ability to find both skilled and unskilled workers to fill many open positions. This drastically shifted the need for industrial companies to respond in real time to supply chain issues and use technologies, such as artificial intelligence (AI) and autonomous operations, to fill the void for missing workers, as well as provide productivity tools to existing workers that are often lacking in experience but comfortable using technologies, such as augmented reality (AR) and virtual reality (VR). This has led companies who are deploying these technologies to become more agile and flexible, sometimes needing to, for example, redesign their products and manufacturing work processes in real time to respond to changes in the supply chain. The result of this will create demand for technologies that ARC feels will grow more mainstream in 2023 and beyond, helping industrial companies increase their revenue and profits as well as their sustainability and operational resilience.
New digital transformation technologies used to augment people and processes across the manufacturing industries, in the edge, cloud, etc., combined with artificial intelligence (AI), are changing the way people work and how companies perform. AI-enabled solutions are a major component of digital transformation, which touches industrial products, operations, value chains, and aftermarket services. This transformation is enabled by augmenting people and knowledge through the expanded use of IIoT sensors, current and historical data, and predictive and prescriptive analytics. While AI is currently being used for advanced data analytics and to generate new insights predictions, prognostics, or recommendations, ARC Advisory Group sees this technology playing a greater role that significantly impacts everything from workflows to production efficiency.
In last year’s Key Technology Trends report, we focused on trends which include meta-machine interface, the convergence of HMI with AR/VR; real-time smart supply chain solutions; AIoT Solutions, the convergence of artificial intelligence and IIoT; smart safety solutions that increase productivity and resilience; and virtual commissioning converging with digital twin; all of which continued to gain acceptance. For this year, in no particular order, here are some of the key technologies that ARC Advisory Group believes will increase in importance over the next twelve months or so. While far from a complete list, the technologies discussed in this report will almost certainly make an impact on industry and infrastructure in 2023, building upon the demands created for companies to thrive in a world where the only certainty is uncertainty.
Growth in Virtualized and Edge Control Applications Leads to “Industrial-Control-as-a-Service”
There is little question that the influence on future automation architectures caused by the accelerated convergence and in some cases fusing together of operations technology (OT) and information technology (IT) will be tremendous. More and more critical functions are becoming software-based, hardware is becoming more standardized and commoditized, and virtualization is consolidating software on hardware. The industrial edge is integrating classic automation systems to become Edge Automation Platforms, which will make these applications become more IT-like with the convergence of OT and IT at the edge. Edge Automation Platforms create an IT environment that is often lacking in traditional automation systems.
Traditional automation components are endpoint devices. Modern IT architectures deploy application software in a modular fashion in containers, allowing software installations of all sizes to be managed efficiently at scale. As manufacturers adopt Edge Automation Platforms, which are typically managed by the OT group, ARC expects to see growing interest in virtual deployments of time-critical control applications, such for discrete (vPLC), hybrid (vPAC) and process (vDCS) control.
Moving the traditional PLC/PAC from the machine to the industrial edge allows critical control applications to be better managed in an IT-like environment, while keeping them close to process. To support the deployment and management of whole fleets of vPLCs/vPACs, automation suppliers will offer tools that add flexibility and scalability, allow cloud-based PLC/PAC file storage and backups, enable management of traditional and virtual PLCs/PACs in the cloud, and provide automated code deployment. This will be an important step toward providing “Industrial-Control-as-a-Service” in the future.
In 2023, look for the growth in virtual and edge control deployments, which will begin to lay the foundation for future industrial control as a service application.
Digital Threads Become a “Closed Digital Loop” of Continuous Improvement
All industrial companies seek Operational Excellence (OpX), which is a systematic approach to attain best-in-class performance in productivity, quality, and delivery of products and services. OpX spans product design and development; enterprise resource planning and control; supply chain management; manufacturing execution; and operational effectiveness of people, processes, and assets. However, rather than a destination or endpoint, OpX is an ongoing journey.
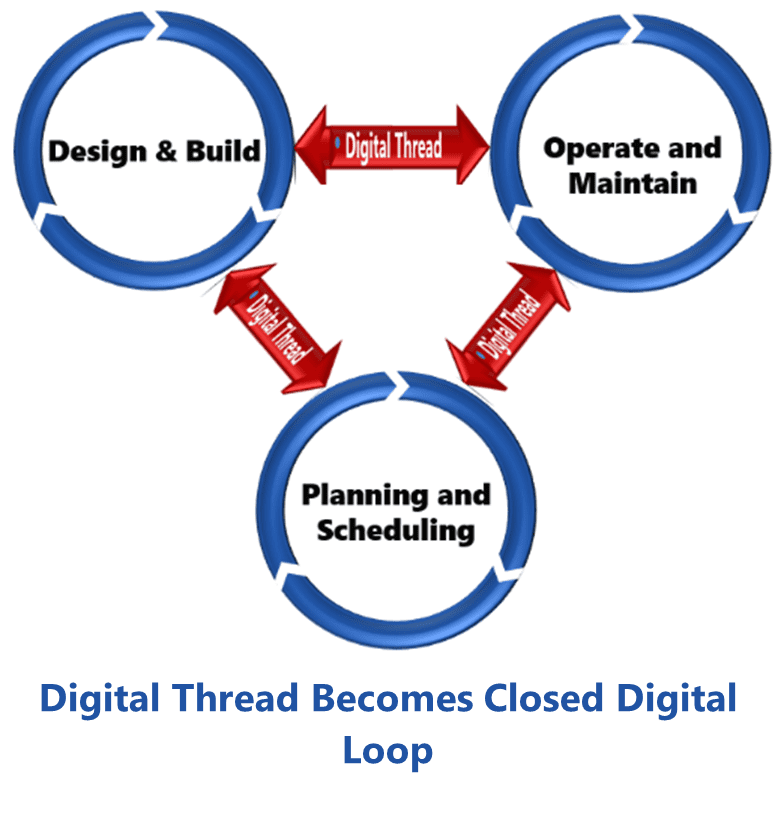
To meet these OpX imperatives, industrial companies must continue to leverage a common digital thread to improve agility, reliability, and efficiency. The digital thread involves a communication framework to connect the silos and provide data flow across the manufacturing domains. This enables an integrated view of the asset’s information, documentation, and data throughout its lifecycle across the traditionally siloed functional perspectives. A digital thread extends across design and build, through handover, toward operate and maintain, and into the next upgrade cycle. Engineers typically spend 30 percent of their time looking for information. A digital thread provides a means to significantly reduce this waste.
In recent years, technologies and approaches such as OpX have been providing companies with new tools to make the digital thread into closed loop, providing continuous improvement to all manufacturing domains. Having a closed loop digital thread provides a common denominator for connecting the raw operational and asset data converted into actionable intelligence to all design, engineering, operational and maintenance domains that enable humans, software applications, and machines to take the right actions at the right time to continuously improve operational, asset, and supply chain performance.
In 2023, look for digital threads to be configured into closed loops of continuous improvement, which will result in greater improvements to all design, build, operate and maintain functionalities as well as OpX.
Convergence Drives Need for “Enterprise Visualization Interface” Solutions
Most industrial companies use standard tools to display real-time information on their control room, PC or laptop screens and historical data funneled into static reports using tables and charts. However, with the convergence of IT, OT and Engineering Technology (ET), more sophisticated data visualization tools must be added to display more diverse information that allow for faster interpretation and better decision-making. These tools must support “on-the-spot” data and information analysis leveraging complex analytics and provide a presentation format that delivers the highest user comprehension while allowing selections in real-time of whether the information visualized is from the process, production management, or other information sources. This has led to a new category of tools known as Enterprise Visualization Interface (EVI) solutions that can consume multiple types of information and structure it into a complete view.
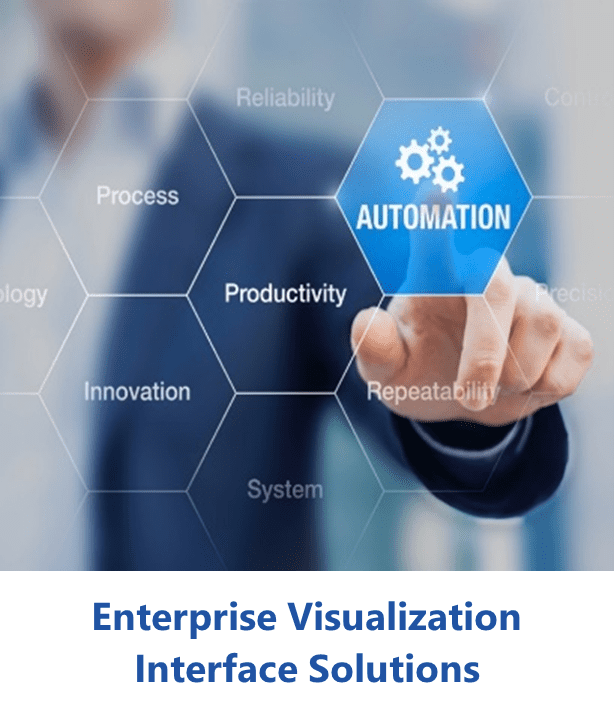
A differentiator of EVI solutions is the ability to exchange data with any application and shape it into a higher-level view. This is influenced by data democratization, which is the process of making data accessible to a non-technical user without having to involve IT. Industrial companies are borrowing IT approaches and architectures developed for enterprise systems with a focus on speed and scale and combining them with OT data practices and process-centric viewpoints. These next generation EVI solutions employ tools to help assist IT and OT personnel in accessing the data they seek to solve problems without retraining or adding data science capabilities to industrial organizations. EVI solutions will be both on-premises and cloud enabled, unlocking the ability to consume and aggregate data from anywhere.
In 2023, look for new EVI solutions to be deployed, both for new applications as well as upgrades from traditional HMI Software solutions.
Workforce Issues Drive Rise of No Code-Low Code Solutions
From retirements due to age or COVID to shortages of qualified engineers and data scientists, the availability of skilled personnel is a major challenge for companies globally. As industry struggles to find skilled personnel, those workers remaining have had more responsibilities added to their roles. Industrial companies are looking for tools to help simplify their workers’ jobs and empower them to perform their jobs safely and effectively, while making sure the company continues to improve performance. This has led to the use of Low Code and No Code technology being incorporated into industrial solutions with the objective of enabling these solutions to be deployed by less experience employees versus being programmed by data scientists or very experience engineers.
There are differences between Low Code and No Code software development platforms. Low Code software requires just minimum coding to configure and deploy and is often used in applications, such as control, HMI, and MES. Low code platforms are designed to be user friendly and require minimal technical knowledge, making them well suited for inexperienced workers to develop applications faster and more effectively. No Code software development platforms differ as they are tools that allow applications without having to write any code. These platforms typically provide a graphical user interface (GUI) that allows users to drag and drop components to create applications. They also often provide a library of pre-built components that can be used to more quickly create applications.
In 2023, look for growing number of industrial software platforms, such as HMI and MES, to be embedded with Low Code and/or No Code capabilities to help industrial companies address their workforce staffing and experience issues and deliver value faster.
New Solution Suites Categorized Specifically for Operational Resilience
One of the objectives of a company’s digital transformation journey is to ensure resilient operations that not only help to increase sustainability, energy efficiency and meet or exceed ESG goals, but to also improve a company’s capabilities to overcome business risks, such as increasing cybersecurity threats, meeting new regulatory compliance mandates, becoming more climate resilient, overcoming supply chain disruptions, securely enhancing remote monitoring and control operations, and adhering to more strenuous plant and personnel safety requirements; all of which is driving demand for dedicated Operational Resilience Solution Suites.
Operational Resilience Solution Suites are typically a portfolio of existing automation and energy management solutions that are being packaged together and enhanced with specific capabilities that focus on operational resilience but provide many other benefits. These solutions often include capabilities that, for example, help companies to break down physical and organizational boundaries to better engage their workforces, connect teams, and enhance real-time collaboration between operations and energy management. These solutions also include capabilities that help supply chains to be managed in real time to maintain their integrity, agility, and flexibility, enabling the company to respond immediately to market demand and shifts in material availability. In addition, these solutions provide tools to help workers become more productive in the face of worker and skill shortages. Companies are deploying these solutions to protect against unscheduled downtime and asset failures, ensure product fulfillment, protect personnel, sustainably manage their workforce, and enhance security architectures, all of which provide a clear alignment behind their operational resilience journey.
In 2023, look for a growing number of Operational Resilience Solution Suites to be introduced that provide companies with results that demonstrate how greater operational resilience also leads to greater productivity and profitability.
Other Trends to Watch
Whereas the key technologies for 2023 are based on a combination of research and client discussions regarding matching the latest technologies with future demand, ARC Advisory Group also surveyed 546 persons who work in industrial manufacturing and processing globally across the discrete, hybrid, and process industries regarding which existing technologies that they feel will change manufacturing and will be the most impactful technologies over the next five years.
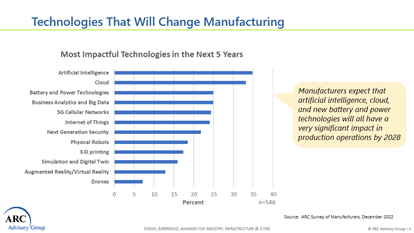
The results were that manufacturers and processors expect that artificial intelligence, cloud, and new battery and power technologies, followed by business analytics and big data, 5G cellular networks, and internet of things, will have a very significant impact in production operations by 2028. However, based on ARC’s research, we are likely to see big increases in simulation and digital twins, as well as augmented reality and virtual reality, in future end user surveys. ARC Advisory Group will continue to research and evaluate these latest technologies and approaches and looks forward to witnessing their impact on the digital transformation of industry, energy, and infrastructure.
For further information or to provide feedback on this article, please contact your account manager or the author at cresnick@arcweb.com. ARC Views are published and copyrighted by ARC Advisory Group. The information is proprietary to ARC and no part of it may be reproduced without prior permission from ARC.
Add a comment