Open headcount is increasingly more difficult to fill these days. This impacts many facets related to equipment, including design, installation, operation, and maintenance. Challenges resulting from limited labor resources have amplified negative impacts.
With limited resources, thinking outside the box for smarter solutions is critical. Newer technologies in motor control keep customers keep moving forward.
These innovations often provide a significant benefit for larger motor applications where serious work is being done. Here are four innovations in higher-amp contactors you should know about.
1. Know when it’s time to change the contacts.
Large motors complete important work. Downtime can have a significant impact. Contact tips in contactors wear down as the contactor opens and closes over time. At some point, they need to be replaced. Traditional contactors don’t alert operators when contact replacement is needed. This often results in unplanned downtime.
TeSys™ Giga by Schneider Electric™ includes contactors with a diagnostic LED on the contactor face, indicating when the contactor has less than 15% usable life remaining. An optional add-on accessory further allows a wired signal to light an external pilot light or provide an input to a programmable logic controller (PLC) if desired. This alarm provides maintenance staff ample time to order replacement contacts and schedule the installation on their schedule, instead of reacting to unplanned downtime.
2. Eliminate the large control transformer.
Traditional motor control schemes typically use a control voltage lower than the main power voltage. This helps reduce risk to those that may be turning selector switches or operating push buttons. A control transformer is used to reduce voltages to a lower alternating current (AC) voltage (typically to 120 volts AC), and a power supply is used to reduce to a lower direct current (DC) voltage (typically to 24 volts DC). The size of the transformer or power supply increases as the size of the contactor increases, as more power is needed to operate larger contactor coils. This means a large-horsepower (HP) contactor may require a sizable transformer to operate it.
A power supply large enough to power a larger contactor 24-VDC coil may end up being a costly expense. In this scenario, a dedicated control transformer might be added, along with an interposing relay, to allow a 24-VDC signal to indirectly control the operation of the contactor. This is a somewhat complicated approach to simply control a contactor operation with a PLC.
The new TeSys Giga advanced version higher-amp contactors include a coil-input contact that allows motor control directly from a PLC. How does this help offset the need for a large transformer or power supply? It gives the panel designer the ability to power the contactor coil from the main power voltage while controlling the ON/OFF operation using the PLC input signal. In this scenario, a large transformer or power supply is not needed to operate the large contactor coil, which saves on material costs and panel space, while also simplifying the wiring.

3. Turn a two-person job into a one-person job
As control panels get larger, it becomes more difficult to maneuver them during the assembly process. Sometimes, this can require electrical components to be mounted while the panel is standing up (versus mounting while the back pan is in a horizontal position).
Have you ever had to install a large higher-amp contactor while the panel is standing up? If you have, then you know how difficult it is for a single person to hold a large contactor in position while trying to mount the contactor to the back pan. This makes for a two-person job, but not so for TeSys Giga contactors.
TeSys Giga contactors include a “hang-on” screw mount position that allows the contactor to be hung on a mounting screw on the back pan, thus supporting the contactor position while installation screws secure it to the back pan.
4. Avoid complaints and customer heartache
Inconsistent voltage is a problem in certain locations. It can be the result of increased demand on a power grid, excessive voltage drops, phase imbalance, or other causes. This can impact contactor operation that may appear to initially be the result of a defective contactor, but actually is the result of significant deviation in voltage level.
Let’s examine one such scenario and its potential impact on equipment manufacturers.
Suppose equipment with a large HP contactor is installed at a location where the voltage supply drops from time to time. When the contactor is called to operate in this condition, the contactor coil may burn up due to the low voltage and stop working. To the operator or maintenance technician, it may seem that something is wrong with the contactor, and they need to contact the equipment manufacturer for resolution. However, after evaluating the contactor either on-site or after shipping the unit to the manufacturer, it may become evident that there is a voltage problem at the application site. The end user is then asked to check the voltage at their site. The voltage condition needs to be addressed and the contactor replaced. However, if the voltage drops are intermittent, the voltage may seem fine during the time it is checked.
Of course, unplanned downtime is frustrating to the end user. The interruption also costs the equipment manufacturer, not only in terms of time and money but also potentially in terms of customer relationship.
TeSys Giga contactor acts differently in this scenario in two ways:
- The TeSys Giga coils have a wide voltage application range, whereas traditional higher-amp contactors operate at a single nominal voltage. This means that a nominal control voltage of 120 VAC could drop as low as 48 VAC. The TeSys Giga contactor with 48 – 130 VAC/DC coil operates as desired.
- If the voltage is sufficiently low (below the bottom threshold of the wide TeSys Giga coil range), the TeSys Giga contactor will not attempt to pull in as traditional contactors would, which could result in damage to the coil and subsequent failure.
Let’s consider the previous scenario, this time using TeSys Giga contactors. When the voltage drop occurs, TeSys Giga contactors will continue to operate as normal until the voltage drops below the extended voltage range of the coil. When the operator or maintenance staff investigates the reason for the contactor not pulling in as expected, they will observe the visual diagnostic LED, alerting them to the cause of the undervoltage issue. They can address the voltage issue and resume operation.
This approach either continues operation as normal, or if the voltage is too low, it allows the end user to become aware of the issue directly without having to involve the equipment manufacturer or contactor manufacturer. It also avoids time and costs related to replacing/repairing the contactor — much better for all involved.
Learn more
Operating smarter can make a significant difference in various phases of equipment—from design to operation and maintenance. Schneider Electric leads the market with innovative motor control solutions for higher-amp contactors that help equipment manufacturers and panel builders succeed. Scan the QR code below, or click here to learn more about TeSys Giga motor starters or to connect with a knowledgeable sales representative.
Learn more about TeSys motor starters or request a follow-up with our support or sales team
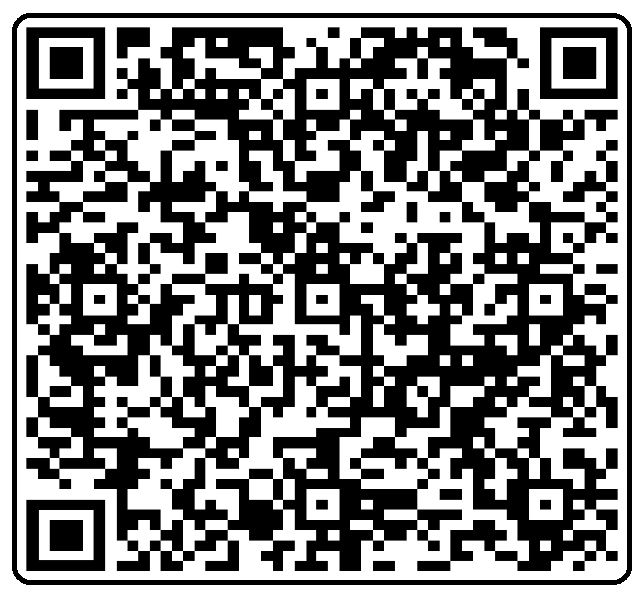