This audio was created using Microsoft Azure Speech Services
The lithium-ion battery market has been steadily growing and is expected to continue its growth over the coming years (at a CAGR of 12.3% from 2021 to 2030). This increase is, in part, the result of the Electric Vehicle (EV) market booming and the popularity of these batteries with automobile makers due to their small size, light weight, and longer life expectancy. For similar reasons, there’s also been growing interest and demand for li-ion batteries as a replacement for valve-regulated lead-acid (VRLA) batteries in uninterruptible power supply (UPS) applications.
But data center decision makers and other IT professionals need some clarity. They are seeing news articles referencing hazards and environmental issues of li-ion batteries, which are raising questions or concerns about the wisdom of selecting li-ion over VRLA and the impact they may have on achieving their corporate sustainability goals. These articles have included claims of child labor in the extraction of cobalt (a material used in some li-ion batteries) and excessive carbon intensity in manufacturing these batteries, concerns regarding their safety during transportation and in use, and uncertainties regarding how these batteries will be handled once they reach the end of their useful life.
The problem is this… These stories typically give an incomplete picture because they only focus on certain (negative) aspects of li-ion batteries. When we view li-ion batteries holistically over the life cycle compared to VRLA technology, we see a different picture. I recently collaborated on a white paper with our Senior Sustainability Engineer, Ray Lizotte, to help clear up the confusion. In this white paper, we demonstrate that, although there are certain aspects with greater environmental impact than VRLA batteries, overall, li-ion has a lower environmental impact over the life cycle. In addition, we anticipate further improvements in the future. We discuss each part of the life cycle, broken into 3 main phases: Supply chain, operation, and end of life. Here’s some highlights of the paper.
Supply chain
A lot of the questions and misconceptions we hear relate to the supply chain. This includes raw material extraction, the manufacturing process itself, and then distribution/transportation of the batteries.
Raw material extraction – There’s a general assumption that because li-ion batteries require mining to obtain the lithium today (vs. VRLA which primarily uses recycled lead), that it is worse for the environment. But when we look at raw material extraction, there are three main considerations that drive the environmental impact: (1) toxicity of the process, (2) the safety and ethics of the mining practices, and (3) the mass of material needed. In the paper, we explain how the smaller mass of material and a significant decrease in toxicity of li-ion result in lower environmental impact overall in the material sourcing phase of the life cycle.
Manufacturing process – A common misconception is that because a li-ion battery is a more complex “system” in terms of components needed to operate safely (such as battery management system and switchgear), that it has a greater environmental impact during manufacturing. However, for typical installations, when replacement batteries over the lifetime are considered, the environmental impact of manufacturing for li-ion systems is less than VRLA systems, even with the added equipment overhead.
Distribution & transportation – There are often concerns of safety brought up with this topic. It is true that the regulations and processes around shipping li-ion are more complex. But a big factor in the environmental impact of distribution/transportation has to do with the weight of the system. So, although the complexity of distribution and transportation is increased, the lighter weight of li-ion over VRLA enables the environmental impact to be reduced.
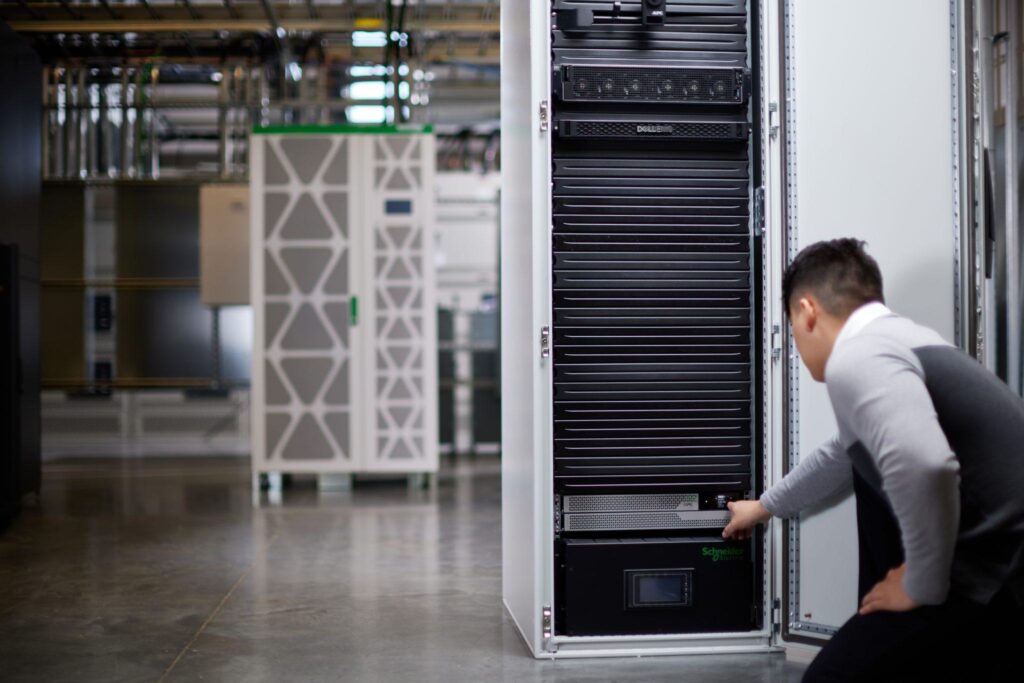
Operation
When we talk about the operation or “use” phase of UPS batteries, the main environmental considerations relate to installation & handling, energy consumption and its associated CO2 emissions, and the battery lifespan.
Installation & handling – The main driver to the difference in environmental impact of the two battery types during installation and handling is the weight differences. Although a minor impact overall, the lighter weight of li-ion and need for less or no li-ion battery replacements over the lifetime results in decreased environmental impact during installation and handling compared to VRLA.
Energy consumption and carbon emissions – The common question here has to do with CO2 emissions from the energy consumed. UPSs are use-driven products, with more than 90% of its emissions occurring in this phase. Although batteries represent a small percentage of that energy, roughly half the energy is needed to keep li-ion batteries charged compared to VRLA, resulting in a decrease in CO2 emissions during the lifetime operation of the batteries.
Life span – The longer lifespan of li-ion (typically 10+ years vs. 3-5 years for VRLA) is the key enabler to an improved operational efficiency and overall lower sustainability impact. The more replacements of VRLA needed over the lifetime, the better li-ion performs.
End of life
Perhaps the most controversial topic regarding sustainability has to do with what happens to the batteries when they reach end of life. VRLA has mature recycling practices. But there is uncertainty when it comes to li-ion because the recycling technologies and processes are still developing.
2nd life applications – Qualified secondary uses for UPS li-ion batteries, such as for microgrid applications, allow them to continue to provide value beyond its first designed purpose. The EV market is paving the way for these second use applications. Using UPS vendors that are committed to this strategy ensures batteries made today will reach their true end of life when the economics of recycling are cost effective.
Recycling – While the recycling infrastructure is not mature today, there is a high degree of confidence that a fully functioning and economical recycling system will exist by the time the earliest UPSs with li-ion reach their end of life. This is because:
- the value of metals is increasing, driving the economics towards recycling
- the EV market is driving investment and research in recycling
- and regulations are further driving recycling maturity
Companies such as li-cycle are making significant advancements for the industry. Their hydrometallurgical process, for example, claims to support all chemistries and formats of li-ion batteries, recovers 95%+ of the constituent materials found in lithium-ion batteries, and avoids landfilled waste during the process.
Evaluating over the full lifecycle
The bottom line is… it is important to look holistically when comparing the environmental and social impact differences of the two battery types. It is not a black and white topic, but all things considered over the life cycle, li-ion batteries have a lower sustainability impact. The paper goes much more in depth on each of the life cycle phases, the key misconceptions and variables impacting sustainability, using VRLA as the benchmark along the way. Check out the paper here (White Paper 71), “Understanding the Total Sustainability Impact of Li-ion UPS Batteries”.