This audio was created using Microsoft Azure Speech Services
Sustainability is a must for all organizations, nowadays any operation or company cannot conceive a strategy where emissions reduction is not one of key to reach a sustainable operation.
For heavy industries such as mining, minerals, and metals (MMM) where the processes to raw material extraction and transformations request a lot of energy , been energy electricity , fuel, steam , gas, etc. A short-term strategy to reduce consumption keeping the same quality, quantity and profitability is the challenge for MMM companies
The current digital technologies have improved the computing capabilities to data processing and the communications features embedded with the most of control devices have enabled measure for most of all variables and have allowed identify where and how much there are energy saving chances.
William Thomson says, “If you cannot measure it, you cannot improve it.”, nowadays we get a lot of new tools to measure and share data; but when we are in solution stage we must look to the mathematics. Those equations and theorems that we thought were theory rather than touchable applications are the bases of the Advanced Process Control (APC) that leveraging current data processing capabilities can deliver a considerable energy savings during the plant lifetime.
The Intention of this blog is not to dive deep into a discussion about control paradigms; thus, a brief review would say that the first stage for APC is modeling the plant, the modeling starts with the system observation. Observation is to measure all systems outputs in answer to a known input. After observation stage all data gathered must be tabulated to identify a mathematic abstraction that identify variables dependence and describe the process behavior in one or several mathematics equations with several variables are identified, it is a multivariable control; yes, it is complex math; fortunately, APC software processes all data and delivers the model. Before software tools these convolutions of variables were limited a few variables or took a lot of time.
To highlight how the APC and all mathematic behind can reduce emission and save money, we are going to compare in a quick view the traditional control vs APC
Traditional Control
The majority of process can be controlled with traditional PID (Proportional, Integral and Derivative), again, a very brief review would say that a close loop PID control uses an algorithm to reduce the difference between the physical variable measured and the setpoint (target) given by the plant operator
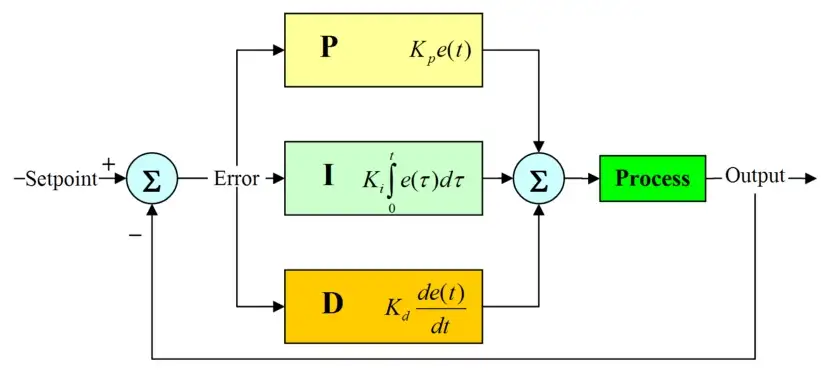
The traditional control does not need a model, the algorithm drives a control element such as valve, pump, fan etc… in order to keep the physical variable as close as possible to the setpoint (target) , the control loop needs a tuning to set the P , I o V constants. But in brief the algorithm is reacting as physical process is changing.
The physical output of the variable to be controlled would be something like (without AVEVA APC)
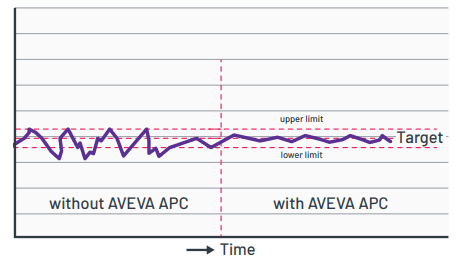
In the section without APC, each fluctuation peak is an unnecessary energy spend. In addition, sometimes the variable is going beyond the limits recommended for quality, quantity, or both.
Suppose the process shown above is the temperature in a furnace for a cement plant, where the setpoint is around 1450°C ; when the PID reaches stable stage, the temperature will be around to 1450°C but “around” means some peaks and sags , thus the questions are how much energy was spent in those peaks? Or how product quality was affected by those peaks and sags? In the example every time the temperature exceeds the setpoint there is an energy wastage.
APC Control
Now let´s suppose the same furnace is controlled with APC, it means a model was developed, the model is the equation can predict the output based on input values, in fact one of the main differences with the traditional control is that APC setpoint are several targets, it means maximum temperature for maximum product quality and less energy wasting within quality process limits (upper and lower limits) .
Focusing on furnace temperature control only, the temperature would be something like (With AVEVA APC part) :
The variable is as close as possible to the setpoint avoiding unnecessary energy spends.
So, 3 conclusions with this furnace example analysis are:
- For a process where there is a considerable energy consumption, traditional PID control fluctuations mean an energy wastage. This wastage during plant lifetime working 24/7 means a lot of tons of unnecessary emissions.
- APC in addition to savings for few fluctuations can take the process variables to the maximum limits of quality, quantity, and energy savings because APC is a multivariable control. It means optimization.
- APC is a sample of how mathematics concepts in conjunction with current computing and software tools are working together to reduce the emissions and production costs. It means sustainability and optimization for mining, minerals, and metals operations.
Also considering the experience of the company Gansu Qilianshan Cement Group Co. in China, facility of Hongda plant, we could highlight the results gotten thanks to AVEVA APC
- They saved 600KEUR in 2019 due to electricity bill reduction.
- The coal consumption was reduced to less than 100kg per TON (10% of reduction)
The APC is math and computing; both are helping with money and energy savings, as well as with emissions reduction.