Quattro modi per aumentare rapidamente l’efficienza operativa e ridurre gli sprechi energetici in un contesto di scarsità di energia e di aumento dei prezzi dei carburanti.
Indice degli argomenti
In ambito industriale gli sprechi di energia si possono trovare ovunque: dalle luci lasciate accese e dallo scarso controllo della temperatura, ai motori inefficienti e alle macchine che lavorano a vuoto per lunghi periodi di tempo. Al giorno d’oggi, questi sprechi possono costare caro alle industrie e minare la capacità di mantenere i livelli di produzione o, addirittura, la stessa continuità produttiva.
Purtroppo, la situazione non sembra migliorare e con l’inverno rischia di complicarsi ulteriormente. L’Agenzia Internazionale dell’Energia (AIE) ritiene che l’Unione Europea si trovi di fronte a un divario tra domanda e offerta di gas naturale equivalente a 30 miliardi di metri cubi (bcm). “Questa differenza potrebbe rappresentare quasi la metà del gas necessario per riempire i depositi al 95% della loro capacità entro l’inizio della stagione di riscaldamento 2023-2024“, si legge in un rapporto. Un quadro preoccupante che sottolinea l’urgenza, sia per i governi che per le industrie, di intraprendere azioni immediate per migliorare l’efficienza operativa e ridurre il consumo energetico.
Ma in che modo?
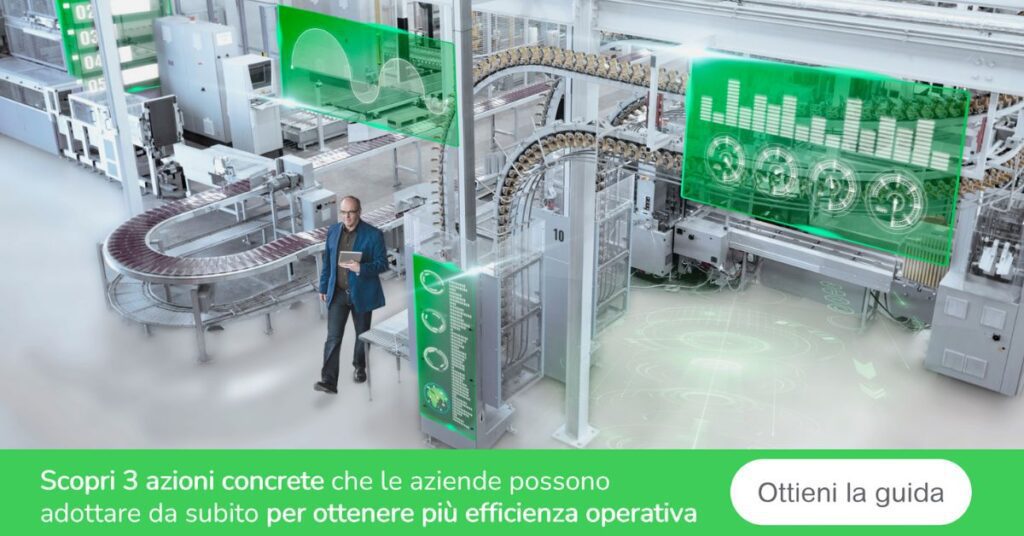
Più efficienza operativa e meno consumi in 4 azioni
Ci sono quattro modi per ottenere questi risultati:
- Misurare i consumi – Condurre audit energetici e installare misuratori di potenza affidabili permette di stabilire dei parametri di riferimento, così da poter preparare un piano efficace di gestione dell’energia.
- Gestione proattiva dell’energia – Soluzioni rapide ed economiche, come l’installazione di azionamenti a velocità variabile o di apparecchiature di distribuzione elettrica connesse e ad alta efficienza, possono ridurre fin da subito il costo della bolletta elettrica.
- Automazione – L’automazione consente un controllo più preciso delle apparecchiature e dei processi, per ottimizzare il consumo energetico senza compromettere i livelli di produzione. È possibile regolare parametri quali temperatura, pressione, velocità e portata utilizzando dati e analisi in tempo reale provenienti da dispositivi connessi.
- Monitoraggio – Un software di facile utilizzo può identificare le tendenze relative agli sprechi di energia e le aree critiche, così da consentire un intervento tempestivo che eviti sprechi di denaro. La gestione dell’energia non va intesa come un’operazione isolata, ma come un processo di miglioramento continuo.
Come sbloccare il potenziale dell’automazione e della digitalizzazione
Automatizzare e digitalizzare i processi industriali può essere quindi il punto di svolta per raggiungere l’efficienza operativa e ridurre i consumi energetici.
L’automazione ottimizza i processi, l’energia e l’uso delle risorse, riducendo gli sprechi delle utilities e delle materie prime. La digitalizzazione rende invece visibile l’invisibile; grazie a data intelligence e agli analytics è possibile individuare ed eliminare le inefficienze lungo la catena del valore.
In particolare, queste 2 componenti possono facilitare il livello di controllo in 3 modi:
- Permettono la creazione di“dashboard” per trarre i maggiori vantaggi dall’utilizzo di dispositivi come sensori, luci o motor drives. Queste applicazioni basate sul cloud sono più convenienti in termini di costi e di qualità (e quantità) di dati generati rispetto al monitoraggio manuale dei consumi energetici. Consentono inoltre di identificare con più efficacia le opportunità di miglioramento nella gestione dell’energia. Grazie alle funzionalità predittive, permettono di sviluppare anche strategie proattive per gestire casi specifici.
- Offrono una visibilità end-to-end che consente di utilizzare lo storico dei dati di consumo energetico per fare previsioni sull’utilizzo futuro. L’acquisizione di questi dati “what-is” consente la costruzione di modelli “what-if”. AVEVA Unified Operations Center, ad esempio, fornisce questa funzionalità e aiuta a superare i limiti tra gestione dell’impianto e produzione. L’integrazione con gli strumenti già in uso in azienda consente di prendere decisioni più accurate e rapide, limitando così gli sprechi, aumentando l’efficienza e ottimizzando le prestazioni.
- Consentono l’integrazione della gestione dell’energia con l’automazione di processo e permettono di:
- Eliminare i limiti legati alla raccolta separata delle informazioni e scoprire tutte le opportunità che hanno un impatto diretto sull’efficienza dell’impianto per ottimizzare il sistema;
- Aumentare la consapevolezza relativa ai consumi energetici in tutto l’impianto;
- Ottimizzare fino al 10% l’uso dell’energia nelle attività produttive.
Un esempio concreto di efficienza operativa
Gli impianti di trattamento delle acque reflue consumano una grande quantità di energia. Massimizzare l’efficienza operativa diventa quindi una priorità. Quando Veolia Water ha deciso di costruire un impianto di trattamento delle acque reflue all’avanguardia a Punta Gradelle, sulla costiera sorrentina, aveva bisogno di un sistema di controllo sofisticato in grado di gestire in modo efficace ed efficiente le complesse operazioni.
La soluzione EcoStruxure™ for Water è risultata perfetta perché offre un’efficace combinazione tra automazione dei processi dell’impianto e gestione dell’energia. La centralizzazione e l’aggregazione dei dati in tempo reale forniscono al team operativo informazioni utili per prendere decisioni più informate sull’efficienza energetica, l’affidabilità delle apparecchiature e sulle azioni di manutenzione da mettere in atto.
Al termine dei lavori, Veolia ha ottenuto un significativo risparmio del 15% di energia (e dei relativi costi) e un miglioramento del 20% dell’efficienza produttiva. Gianfranco Favali, Project Design Department Manager di Veolia, ha definito i benefici ottenuti “davvero notevoli”.
Per avere un termine di paragone, il Dipartimento dell’Energia degli Stati Uniti stima che gli impianti di trattamento delle acque reflue americani consumino più di 30 TWh di elettricità all’anno, per un costo cumulativo di circa 2 miliardi di dollari. Se si adottassero misure per ridurre il consumo energetico del 15% in tutti gli impianti, riducendo gli sprechi e migliorando l’efficienza operativa, si otterrebbe un risparmio di ben 300 milioni di dollari all’anno!
Per ulteriori informazioni
Per saperne di più sulle misure da intraprendere per ridurre il consumo energetico nell’industria, scarica la nostra guida “Tre azioni concrete per aiutare le industrie a superare la crisi energetica europea”.
Questo post è stato originariamente pubblicato sul blog global di Schneider Electric.
Aggiungi un commento