Come sfruttare le ultime tecnologie digitali per superare la sfide della digitalizzazione e scalare le opportunità della quarta rivoluzione del settore industriale.
Di Barbara Frei è Executive Vice-Presidente e Chief Executive Officer, Industrial Automation di Schneider Electric.
Indice degli argomenti
- Restare focalizzati sulla trasformazione e sull’efficienza nel settore industriale
- Guidare una trasformazione industriale responsabile nei siti produttivi
- Portare la trasformazione industriale fuori dal singolo impianto
- Le persone sono il cuore pulsante della trasformazione industriale su larga scala
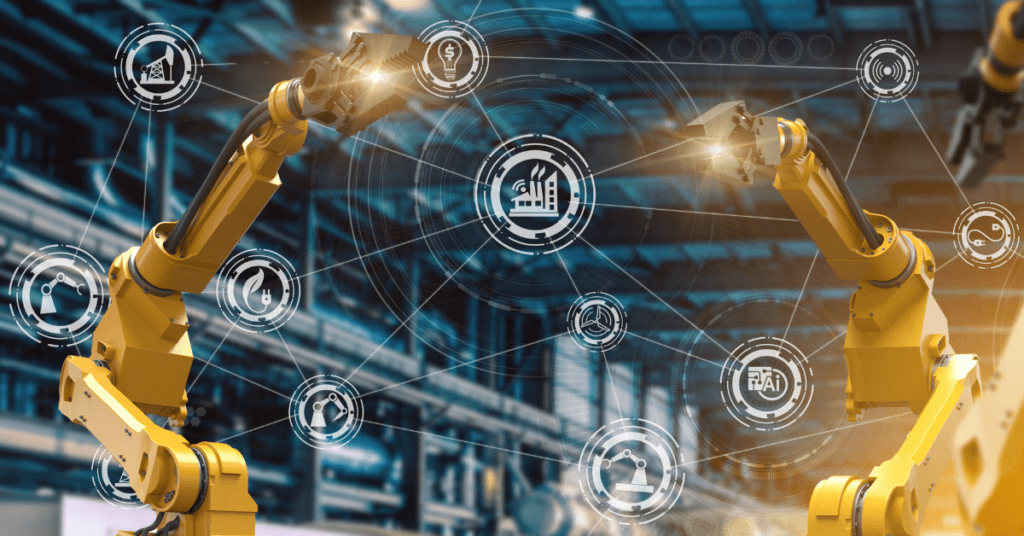
In tutto il ventesimo secolo i libri di fantascienza, film, serie TV hanno immaginato come sarebbe stato il futuro. Isaac Asimov, nel suo ciclo di romanzi e racconti sui robot, parlava del potere dell’automazione. I protagonisti di Autofac, un racconto del 1955 di Philip K. Dick erano macchine che si auto-replicavano, prendevano il controllo di una fabbrica e portavano la produzione al suo limite.
La gran parte delle previsioni sulla trasformazione del mondo industriale non si sono realizzate. Il più recente report World Robotics, però, rivela che l’uso di nuovi robot industriali è al più alto livello di diffusione di tutti i tempi. Solo nel 2021 se n’è installati mezzo milione in impianti di tutto il mondo. In parallelo le reti 5G, l’Internet of Things e l’Intelligenza Artificiale hanno fornito i “mattoni” su cui costruire un futuro industriale. Anche se appare molto differente dal presente – per non parlare del 1955.
Restare focalizzati sulla trasformazione e sull’efficienza nel settore industriale
Chi opera nell’industria oggi riconosce che le tecnologie dell’Industria 4.0 possono non solo trasformare l’operatività. L’industria 4.0 può rivoluzionare il concetto di efficienza operativa e migliorare la competitività, non solo in termini di produttività.
Attuare questo cambiamento su larga scala e velocemente rimane comunque una sfida complessa. Molte aziende industriali stanno sperimentando vari casi d’uso, ma devono ancora realizzare i benefici tangibili di un’operatività più intelligente.
Inoltre, in tutto il mondo le imprese stanno affrontando uno scenario di incertezza senza precedenti. Le conseguenze della pandemia. La geopolitca. La crisi energetica globale. I prezzi delle commodity in vertiginoso aumento. I costi sempre più alti della logistica. Il cambiamento climatico. La pressione sempre crescente sul ridurre le emissioni di anidride carbonica e l’impatto ambientale. Tutto questo, ripercuotendosi pesantemente sulle supply chain, ha portato i temi della resilienza operativa, dell’agilità e della sostenibilità in cima all’agenda.
Guidare una trasformazione industriale responsabile nei siti produttivi
Pur confrontandosi con tali scenari, alcune aziende manifatturiere si sono messe alla guida di un percorso di trasformazione industriale adottando l’intera gamma di tecnologie Industria 4.0 per sfruttarne l’enorme potenziale.
Ad esempio, oltre i cancelli dell’impianto Schneider Electric di Le Vaudreuil, nel nord est della Francia, veicoli senza conducente e robot collaborativi sono parte dell’attività produttiva quotidiana. Le Vaudreil è stato riconosciuto dal World Economic Forum due volte, come Advanced and Sustainability Lighthouse; è uno di sette siti produttivi al mondo indicati come pionieri della digitalizzazione, dell’efficienza industriale e della sostenibilità; al suo fianco, fabbriche operate da Johnson & Johnson in Irlanda, da Western Digital in Cina, da Unilever in India e da Micron a Singapore.
Lighthouse vuol dire “faro”: come il nome suggerisce, sono esempi che possono fungere da guida per altri operatori del settore che cercano di superare le sfide e scalare le opportunità della quarta rivoluzione industriale.
A Le Vaudreuil, i dati operativi convergono in un centro di controllo unificato per rivelare le performance di asset, energia e processi. Cruscotti operativi mostrano cosa avviene in ogni angolo di questo impianto da 14.000 metri quadrati, dando al personale sul posto e ai team in remoto aggiornamenti in tempo reale, inviando allarmi, fornendo informazioni data-driven sull’efficacia dei macchinari e su qualsiasi collo di bottiglia nella linea produttiva, o su improvvisi picchi di domanda.
Dall’avvio del programma di digitalizzazione nel 2012, l’uso dell’energia e le emissioni di anidride carbonica dell’impianto di Le Vaudreil sono diminuiti del 25%, e lo spreco di materiali del 17%. I processi di riciclo abilitati dall’AI, inoltre, aiutano a risparmiare preziose risorse idriche.
Portare la trasformazione industriale fuori dal singolo impianto
Per quanto i risultati siano significativi, non siamo assolutamente arrivati alla fine del percorso. Il prossimo capitolo della storia della trasformazione industriale prevede di prendere il potenziale di questi sistemi di produzione digitalizzati e applicarlo non solo nel singolo sito produttivo, ma nell’intera rete di produzione e logistica e nelle supply chain di un’organizzazione.
Questa rete può comprendere decine, anche centinaia di siti: – impianti di produzione, magazzini e simili – in molti diversi paesi e continenti. Schneider Electric ad esempio ha quasi 200 fabbriche, oltre 80 centri di distribuzione e migliaia di fornitori, con i quali collabora in modo molto stretto per abbattere le emissioni di anidride carbonica scope 3 (indirette).
Per molte aziende, integrare reti così complesse è un’enorme sfida. Troppo spesso i siti operano in modo separato, usando diversi sistemi legacy, standard e approcci. E troppo spesso gli obiettivi di trasformazione non vengono raggiunti perché ci si focalizza su singoli impianti o su processi disparati.
Per affrontare la serie apparentemente infinita di crisi che ci circondano, le aziende devono ripensare dalle fondamenta il loro approccio alla trasformazione industriale – perché avvenga in modo sistemico, digitale, basato sui dati e olistico, così da poter ottenere su larga scala valore e performance operative migliori in più siti, e trasversalmente in tutta l’impresa.
Immaginate quanto di più potremmo ottenere standardizzando lo scambio di dati tra sistemi IT quali i software ERP e le tecnologie operative presenti nell’impianto produttivo. Oppure orchestrando un ecosistema completamente interconnesso di fornitori e partner, che possano accedere alle informazioni sugli ordini e all’inventario di più siti per migliorare la pianificazione, la qualità e anticipare potenziali rischi. Oppure, immaginate di poter raggiungere più rapidamente gli obiettivi net-zero e risparmiare sui costi delle utility scoprendo modi per ridurre il consumo di energia e controllarne l’utilizzo.
Tutto ciò richiede la capacità di applicare una chiara roadmap basata sulle tecnologie digitali e sostenuta da un’adeguata governance sulla standardizzazione dei dati e da strategie di cybersecurity.
Le persone sono il cuore pulsante della trasformazione industriale su larga scala
Naturalmente, avviare una trasformazione così completa richiede pianificazione, investimenti e tempo. E richiede anche le persone giuste. Questo significa fare grandi sforzi per attrarre “nativi digitali” con i più diversi background, e offrire continuamente ai dipendenti la possibilità di aumentare le loro competenze e capacità.
Ma abbiamo anche bisogno di un cambiamento culturale: solo quando aziende, team, individui capiranno l’importanza strategica di operare come un’organizzazione unica e integrata potranno fare di più rispetto
a ottenere, semplicemente, obiettivi di produttività sul breve termine – e potranno massimizzare il pieno potenziale che il cambiamento tecnologico può portare, nel lungo termine, nelle industrie del futuro.
Pertanto, mettiamo finalmente da parte questi scenari robotici e fantascientifici “da incubo”. Per vincere le sfide dei prossimi anni e decenni, le industrie devono portare a un livello nuovo la loro capacità di trasformazione, sfruttando la forza complementare di umani e macchine. Significa abbracciare un concetto di efficienza basato sui dati, in modo trasversale in tutta l’impresa, e fornire ai dipendenti le competenze e la formazione di cui hanno bisogno.
Se lo faremo, avremo la possibilità di diventare le aziende industriali sostenibili, agili e resilienti di cui il mondo ha bisogno.
La versione originale di questo articolo è stata pubblicata sul sito web del World Economic Forum.
Aggiungi un commento