Seventy-five years ago, researchers developed the first semiconducting transistor. The impact these small devices- often called “chips”- have had on how we run our homes and businesses has grown exponentially since then. This has been particularly evident over the last few decades, as communication and automation have become increasingly dependent on semiconductors’ capabilities.
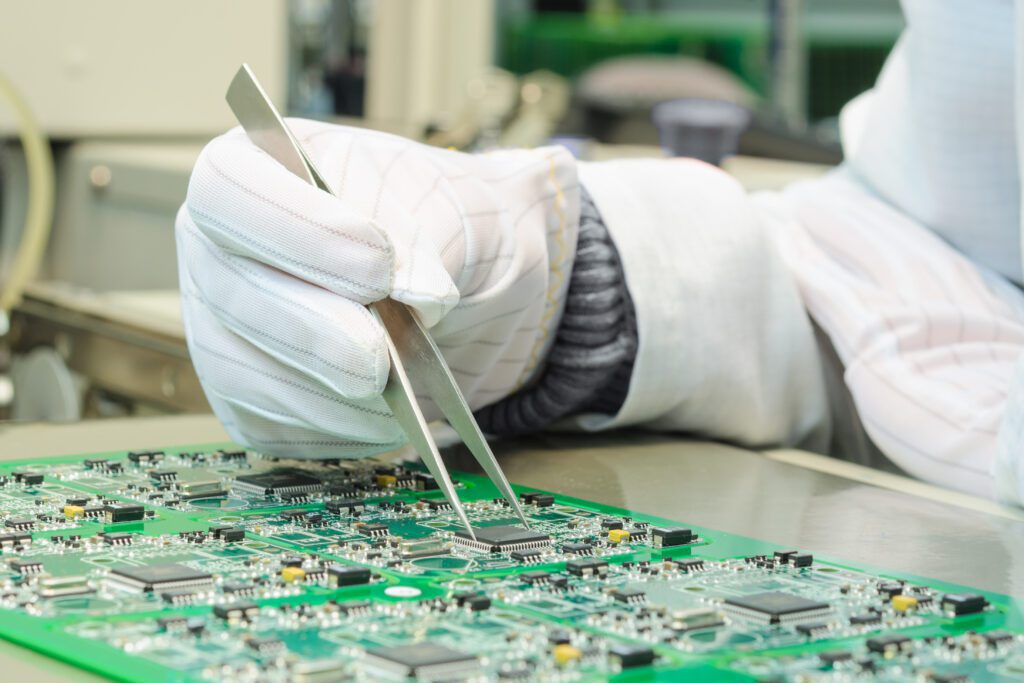
Today, as manufacturers of everything from cell phones to substations seek to add new intelligence to their products, chipmakers around the globe are scrambling to expand capacity to meet demand.
However, demanding requirements make semiconductor fabrication facilities – or “fabs” – expensive to build and maintain. Their owners are challenged to quickly bring new products to market with close attention to cost while minimizing the potential for future downtime and environmental impacts. Choosing a partner with the proper equipment and expertise can give fab owners and managers the insights they need to build capacity, maintain quality, and improve sustainability.
Exponential market growth
As the internet of things (IoT) has worked its way into our lives and businesses over the last decade or so, it has fostered an ever-greater dependence on semiconductors and their fabs. This reliance will only strengthen as we look for new ways to manage energy use and minimize carbon footprints. Market researchers with McKinsey predict annual growth rates for the chip market of 6-8% until 2030, topping $1 trillion by that year.
In the short term, fab owners see a downturn in chip demand. High pandemic-era demand has given way to a glut, and consumers are now spending less on electronic devices. Yet, research firm Gartner says enterprise chip demand is proving more resilient, and manufacturers are moving forward with ambitious growth plans. For example, in February, Wolfspeed announced it would build the world’s largest 200mm semiconductor fab in Saarland, Germany, part of a $6.5 billion effort that includes the world’s largest silicon carbide crystal growth facility, currently under construction in North Carolina.
Supply chain concerns raised during the Covid pandemic and geopolitical considerations are also helping drive demand for new fab development. Currently, 65% of the world’s semiconductors are made in Taiwan. This concentration of chip production is leading governments around the globe to call for added capacity closer to home. Recognizing such concerns, the world’s leading semiconductor producer, TSMC, said it is likely to build new fabs in Japan and Europe soon, extending capacity outside its home base of Taiwan. In the United States, the recently passed CHIPS legislation is already impacting, with several producers announcing plans for new fabs there.
Fab industry challenges
While the market opportunities for fab developers are obvious, the challenges to adding new capacity can be just as significant, given rapidly rising demand projections. We’ve identified four pillars necessary for ensuring success in new fab development:
- Improving the time to market – Fab design and construction is a lengthy process. Developers must find ways to accelerate timelines to bring facilities online more quickly.
- Increasing efficiency – Fabs are highly energy intensive due to both process equipment and the need to maintain precise environmental conditions. Reducing this demand and related costs is critical for a new fab’s future profitability.
- Improving resiliency –Power irregularities and resulting downtime can result in major financial losses for fabs. For example, in February 2021, an Austin, Texas, Samsung plant was offline for over a month following power outages during severe winter weather. According to company figures, losses totaled at least $268 million.
- Growing sustainably – Enormous energy demands can challenge fab owners hoping to meet ambitious sustainability targets. They need new ways to reduce carbon footprints and integrate more renewable energy solutions into their operations.
Supporting fab success
Schneider Electric provides fab developers, owners, and managers with solutions to meet the challenges each of these pillars presents.
- Time to market – Standardized designs and digital architectures help streamline development. Digital twins and other modeling and simulation technologies help design teams spot conflicts and improvement opportunities in the design process and throughout a fab’s lifespan.
- Efficiency – Digitalized sensors, controls, and analytics provide system intelligence to fab operators. This makes for smarter decisions that lower costs and boost efficiency.
- Resiliency – Predictive simulations, 24/7 power quality monitoring and correction, and analytics focused on asset performance help plants stay online for maximum productivity.
- Sustainability – Intelligent sensors and analytics ensure the monitoring and alerting needed to comply with local and regional efficiency requirements and provide data for greenhouse gas emissions for corporate sustainability reports. Additionally, Schneider Electric’s consulting services provide facilities and sustainability personnel support for defining strategies to reach sustainability goals.
Learn more
You can learn more about how Schneider Electric is helping fabs come online more quickly and maximize their potential by visiting our website and downloading EcoStruxure Power for Semiconductor Fabs.