This audio was created using Microsoft Azure Speech Services
Like all manufacturers, glass makers have been tasked with reducing their carbon emissions. This mandate is challenging, however, given the level of power required for the melting process – which is an integral component in all types of glass production.
During this process, raw materials are superheated in a melting furnace to create the chemical reactions that form glass. Temperatures must remain steady during this complex process to ensure quality, as inconsistencies can weaken the end product.
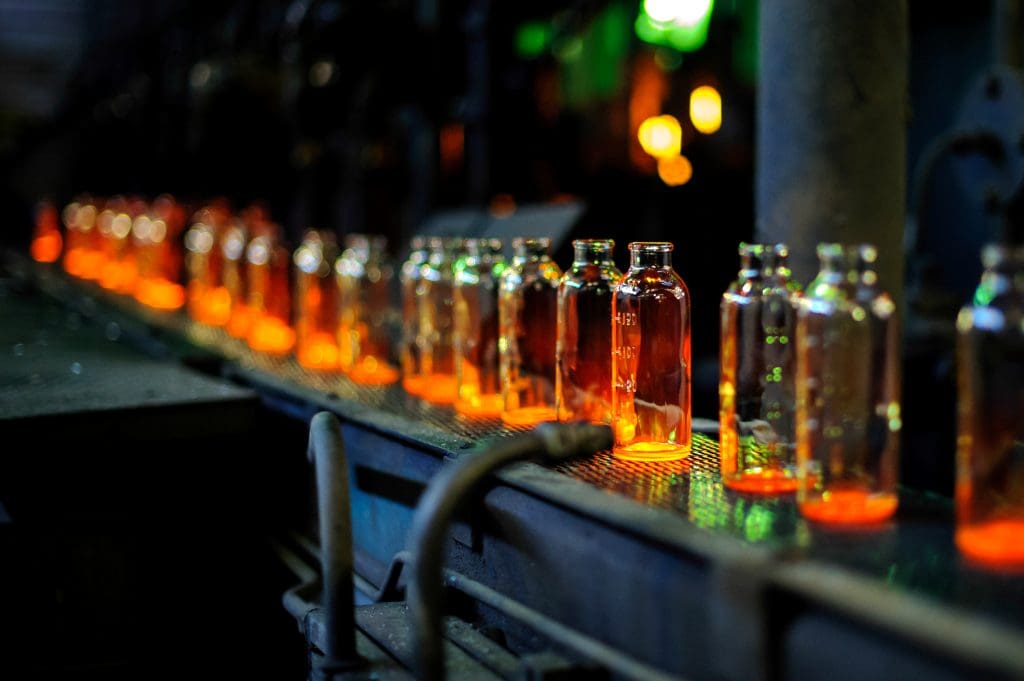
However, maintaining those temperatures – which range from 1500 to 1700°C (2700–3100°F) for 18 to 24 hours at a time – is extremely energy-intensive. In fact, it is a major cost factor in glass manufacturing and uses between 80 and 90% of production line energy.
These traditional glass manufacturing methods have been used for more than 150 years. Since World War II, research and development have made those processes four times more energy efficient by improving the combustion systems, expanding the use of recycled glass, and increasing the size of the furnaces. But while these large fossil-fuel-powered melting furnaces are both operationally and cost-efficient, they are not carbon neutral. To reach decarbonization goals, operators will need to find the optimum point between ideal melt quality while using as little energy as possible.
Switching to electric-powered furnaces can reduce carbon emissions output from this energy-intensive process, but this raises yet another challenge: the need for reliable green energy.
The need for reliable green energy to reach glass manufacturing decarbonization goals
Electrification alone isn’t enough to reduce carbon emissions. To reach carbon neutrality, industries must utilize green energy resources to power the electrification process.
This has caused the demand for green power to skyrocket. Utilities are now engaging in numerous green energy production processes, from renewables to alternative fuels like green hydrogen.
However, although using green hydrogen as a cleaner fuel source for existing melting furnaces is possible, it remains costly and is not readily available. Other industries, such as steel, automotive, and aerospace, require green hydrogen as a chemical catalyst for their processes and are willing to pay higher prices to acquire it.
It’s also worth noting that there can be substantial utility wait times for new or expanded connections of any kind—sometimes years long (as is the case in California, for example). Grid expansions simply aren’t happening enough to accommodate the surge of new electricity demand.
To overcome this grid congestion, glass manufacturers may want to consider non-utility alternative green energy options, like onsite microgrids or energy-as-a-service (EaaS) subscriptions.
Planning for action to meet glass manufacturing decarbonization efforts
It can be extremely stressful for company leaders to decide how and when to switch over without negatively impacting the bottom line. They are essentially gambling on finding the best transition strategy to move towards an electrical system – with an understanding that full transition must be complete by 2050 to meet global carbon targets. This means that there are at most two lifecycles for furnaces, which typically last around 15 years, to determine how to move forward. A successful plan must include investment in a very high level of energy efficiency and flexibility in the power supply systems without exceeding an acceptable level of capital expenditures (CAPEX) at any point in the transition period.
Moving to a fully electrical system requires more insight into and control over the electrical network. New smart monitoring and management systems offer advanced control functions, extensive data collection, and complex analytics. They can provide responsive automation that helps operators control and maintain the new furnaces and can even include integrated training functions to guide staff through unfamiliar tasks.
Combining process & power transitions
It’s important to understand the way that the electrical system impacts the process, to ensure that they truly work together. Unlike with old systems, where power and process are seen as separate, the electrical monitoring and control systems need to be an integrated part of the total manufacturing system.
Putting a transition plan in place can help improve the odds of success for glass decarbonization. That plan starts with how to make existing equipment more efficient (by repairing leaks, improving insulation, and so on). It must also consider the changes needed in both process and power.
A transition plan must also identify equipment end-of-life schedules and determine the lifecycle costs associated with replacement options, including the costs for:
- The new furnace unit – electrical vs. fossil fuel-powered – and associated staff training
- Inventory of existing electrical network and required upgrades
- A reliable source of green power (utility, private microgrid, EaaS, etc.)
- Estimated costs of energy or fuel to power the unit across its lifecycle
- Amount of green house gases emitted
- Assessment of upcoming regulatory requirements, including increasing carbon costs
The value of partnership
The reality is that moving over to greener facilities is a very complex process. This is where an expert partner like Schneider Electric can help. A partner can lead the effort to assess current systems and future needs and provide guidance on what makes sense for your facility in your region. They can help negotiate energy contracts.
Once you have chosen a specific technology, an expert partner can design your system to your exact specifications, taking into account both power and process control. They can also ensure your operators learn the new process efficiently to minimize confusion and human error. To learn more about how Schneider Electric can support your energy transition project, please join us at Booth #14G49 at Glasstec 2024 in Düsseldorf from 22 – 25 October.
Add a comment