Steel is the backbone of modern life—essential for buildings, infrastructure, transportation, and more. However, this integral material comes at a hefty environmental cost, as production is highly carbon-intensive. Currently, the steel industry generates 1.8 tons of CO2 for every ton of steel produced. This makes it responsible for around 9% of global carbon emissions. Even though 60% of the largest steelmakers have made firm GHG emission reduction commitments for 2030, global carbon neutrality goals may not be achievable unless we fully address the challenges the steel industry faces in reducing emissions.
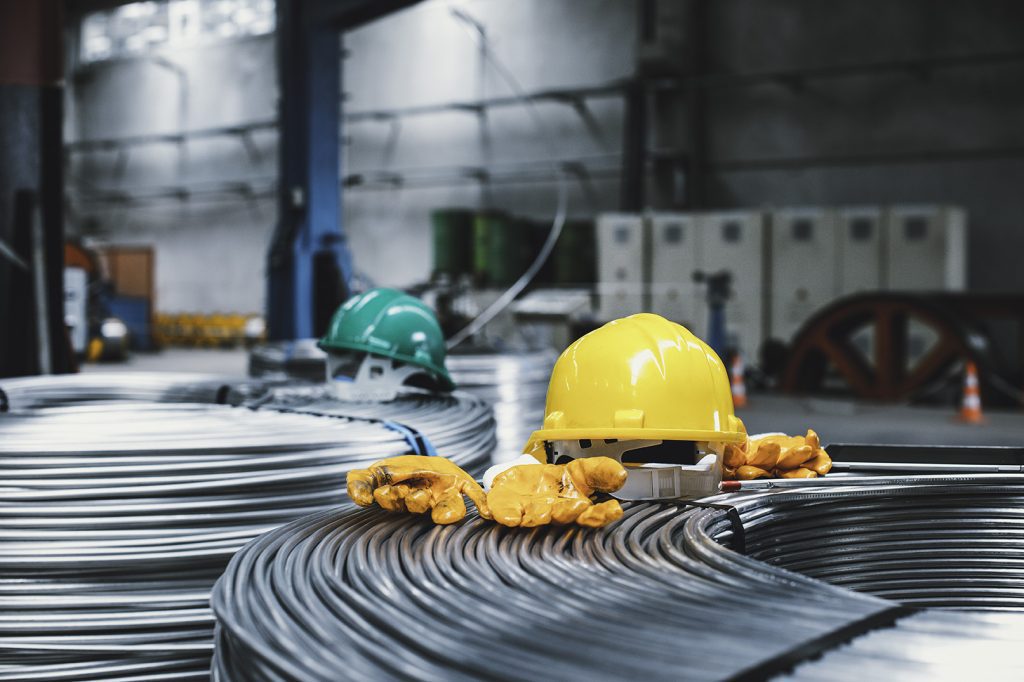
Industry Challenges to Reaching Carbon Neutrality Goals
Steel industry decarbonization is crucial to reaching global net-zero targets. In over 50 countries, regulators are now implementing policies to incentivize lower steel emissions through emissions quotas and carbon prices. The steel industry is also rolling out several innovative approaches to decarbonization.
However, the sustainability challenges extend beyond technology. The availability of renewable energy and hydrogen, the cost of energy, and the volatility of the electricity market—particularly in parts of Europe—are key factors. The added cost of green steel manufacturing may lead existing companies to view overseas investments in steel as more strategic. Insufficient demand for green steel outside the automotive industry, which accounts for just 12% of total steel consumed, is a key concern. Asia-Pacific, where 70% of steel is currently manufactured, must also introduce policies supporting green steel production if we are to meet emissions goals.
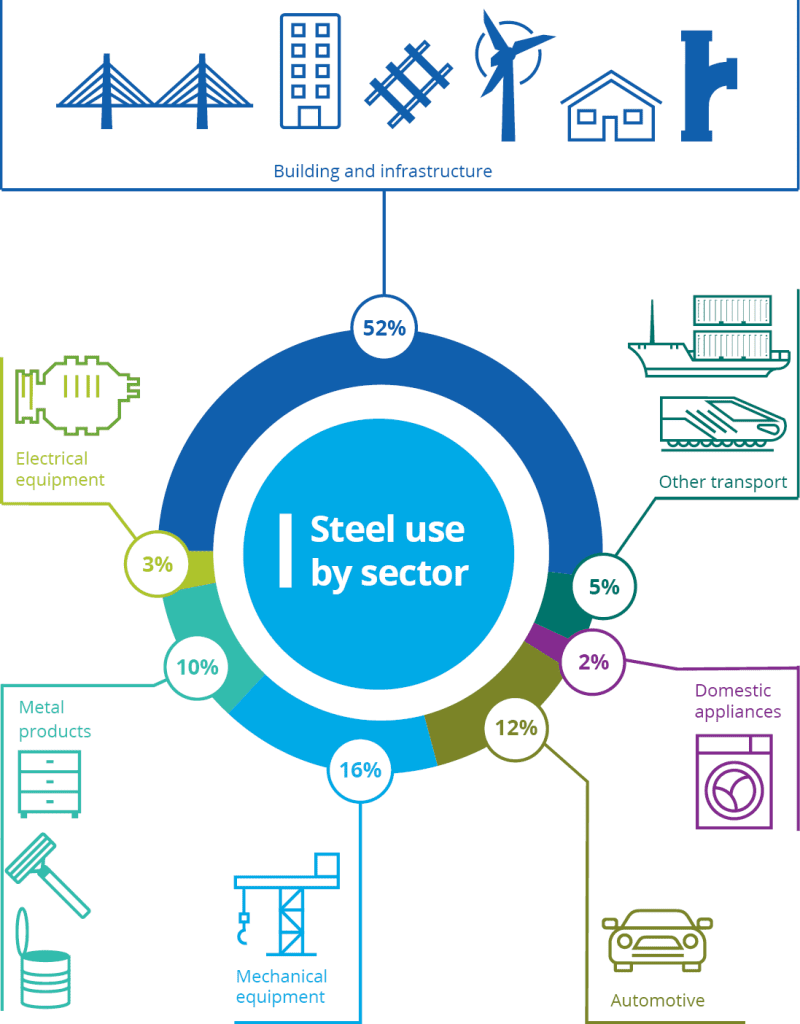
Decarbonizing the industry is also costly. A recent study estimated it will take around €4.4 trillion to transition the steel industry by 2050, implying an annual investment of €15.1 billion in addition to the regular annual CapEx of €103.8 billion. This raises the question: What is needed for the industry to deliver on 2030 decarbonization targets, given limited demand and the need for significant financial investment in these new technologies?
Access to capital
Recognizing the industry’s importance and the challenges steel companies face, governments worldwide are providing financial support. The European Union has pledged €10.5 billion in grants for companies like ArcelorMittal, Thyssekrupp, Tata Steel, H2GS, and others. Through its Inflation Reduction Act (IRA) programs, the US government has pledged up to $1 billion for two new plants. Financial institutions are also showing increasing interest in providing financing directly linked to decarbonization.
However, even with significant subsidies and grants, steelmakers face huge CapEx costs to transition successfully in the next two decades. One small ray of light for the industry is that access to capital is typically easier for recognized “sustainable” companies and could well come at a more competitive cost.
However, more intervention in global markets (specifically the Asia-Pacific region, where government policy and grants are lagging compared to those in place across Europe and the US) is needed to ensure that expenditures on green steel are worth the investment. Asia-Pacific needs to introduce more aggressive policies that financially support green steel production while also providing regulatory support to drive demand for green steel from other industries.
New approaches drive positive disruption
New players in the market are increasingly being seen as positive and disruptive game-changers. ESG-driven green steel startups are paving the way for industry decarbonization with new technologies and a focused approach to the parts of the value chain where they can make a unique impact. Their innovations extend into unique partnerships and funding models. This is attracting progressive investors and putting pressure on incumbent steel manufacturers to do the same or risk losing out as the market seeks greener sources.
As an example, a recent project in northern Europe brought together a consortium of major technology and energy companies to power a low-emission steel plant. CapEx financing was provided to support this green startup and provide the energy as a service.
Using renewable energy from utility providers to generate green hydrogen, the plant produces Direct Reduction Iron (DRI). The DRI is then refined in an electric arc furnace (EAF) with an electrical distribution system. This is designed for maximum efficiency and optimal performance. Overall, this project should result in a 95% CO2 reduction, with a CapEx savings of 25%. It has already elicited strong down-stream demand from automobile manufacturers keen to secure a reliable supply of low-carbon, “green” steel.
Energy-as-a-Service option
One new adaptation in the market that can help steel companies move forward with their green transition is the concept of Energy-as-a-Service (EaaS). Technology suppliers such as Schneider Electric can offer related equipment and services, from design consultation and equipment installation to real-time monitoring of a company’s electrical network, as a service being paid off over a contract timeframe
Whether using a model where the supplier operates and maintains systems for some time or one where the company manages assets funded by a partner, this approach provides major benefits:
- Affordable decarbonization and reduced financial risks
- No upfront costs for upgrades
- Access to renewable energy sources
- Improved operational and energy reliability and resiliency
Want to know if Energy-as-a-Service is right for you? Read our Industry Perspectives masterpiece now.
A transition with global urgency
While the technology to reduce CO2 emissions exists, decarbonizing the steel industry requires more than new equipment. Strong policy and regulatory intervention across multiple industries is needed to ensure the demand for green steel reflects the global urgency of the transition. There must also be a focus on the production and availability of clean power, green hydrogen, and green procurement for low-emission steel.
Another way steel manufacturers can gain insight into their carbon impact is by addressing the footprint of their entire supply chain, including suppliers’ operations. While this may sound daunting, the industry non-profit Global Mining Guidelines Group (GMG) has partnered with Schneider Electric to launch a program called Materialize as a pathway.
Materialize provides a framework for companies to partner with suppliers and other manufacturers to build a comprehensive carbon emissions database to further drive decarbonization efforts. It also supports participating companies by providing opportunities to engage with renewables, clean energy initiatives, and circularity planning for the entire product lifecycle.
Learn more
Explore these resources to learn more about the Materialize program or to discover Schneider solutions transforming the steel industry. Join the movement towards a greener future for the steel industry and start exploring Energy-as-a Service options for decarbonized steel.
Add a comment