Today, we are seeing with our own eyes how global warming is impacting our planet. Incidences of extreme weather occur more frequently and with more intensity. As greenhouse gases (GHG) trap the heat from our sun, the surface and oceans are heating up. The atmosphere’s carbon dioxide intensifies this effect, and burning fossil fuels releases vast quantities of carbon dioxide.
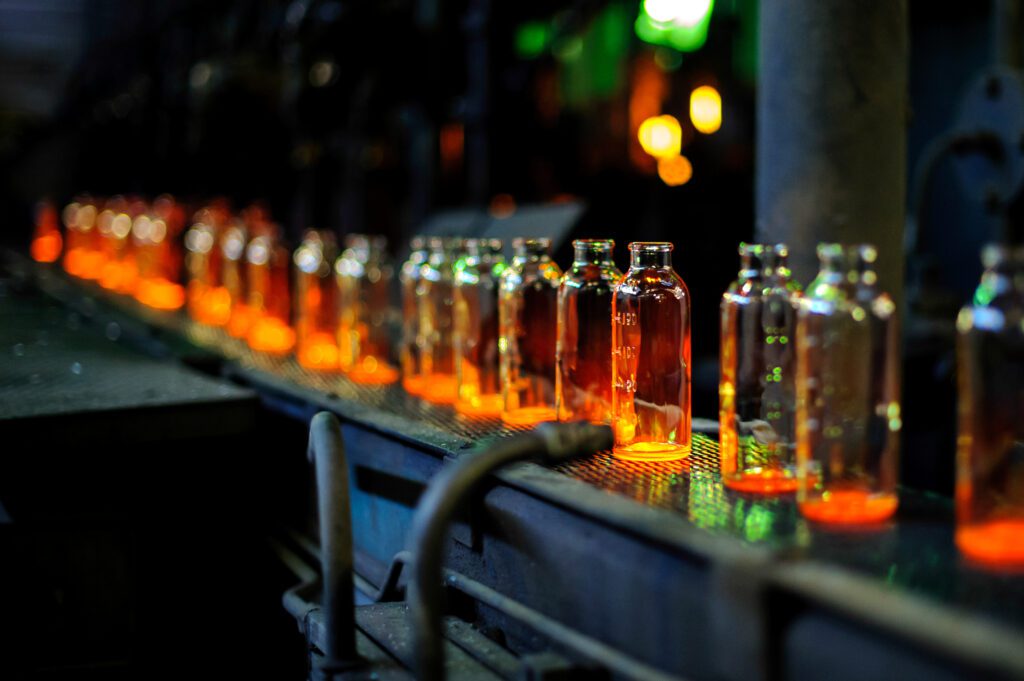
The current global warming dilemma and its adverse side effects challenge all of us. Heavy industries (e.g., cement, steel, and glass) traditionally relied on fossil fuels to run their blast furnaces. As manufacturers look for new ways to decarbonize their operations and reduce fossil fuel dependency, new alternative energy possibilities are emerging that help facilitate the transition to lower emissions.
3 options for managing the migration to green glass
How will the glass industry migrate to the next echelon of high efficiency and low carbon emissions?
Let’s look at three opportunities.
- Biofuels — Any fuel derived from biomass is a biofuel. Biomass is organic matter from any plant (including trees), algae material, or animal waste. Examples include wood, wood residues, energy crops, agricultural residues, straw, and organic waste from industry and households. This waste gasifies when bacteria digest the organic matter, and the gases released can be used to produce energy. Since such feedstock material can be readily replenished, biofuel is considered a source of renewable energy, unlike fossil fuels such as petroleum, coal, and natural gas. For the glass industry, however, questions remain as to whether biogas fuel will be available in sufficient quantities to address the demand for their furnaces, resulting in high prices and low availability.
- Hydrogen — Natural gas reforming (producing hydrogen from natural gas through a steaming process) and carbon capture (placing CO2 waste back into the wells where the natural gas came from) sound like logical approaches to decarbonization. However, the carbon capture concept feels like a landfill or an underground nuclear waste dump. The “problem” is not resolved; it’s just temporarily displaced. In addition, burning hydrogen is not energy efficient, hence why hydrogen cars have fuel cells.
To operate, the glass industry largely depends on heat rather than hydrogen. The compression and cooling of hydrogen contribute to higher energy losses. Storing large quantities of hydrogen can be complex and carries explosion risks. Electrolyzing, compressing, cooling, storing, transporting, and burning hydrogen in a glass furnace consumes energy. Given these circumstances, overall efficiencies are lowered as about 70% of the initial green energy potential is lost.
- Electricity — Replacing traditional fossil fuel infrastructure (e.g., coal and gas-powered furnaces) with electrical equivalents helps achieve melting at the scale needed to meet consumer demands, but performance optimization persists. The more electrical energy that needs to be fed into a furnace, the higher the number of electrodes required. With more electrodes to manage, workers would have less time to perform maintenance, which could negatively impact furnace uptime.
Designing electrical furnaces with bigger electrodes or using higher frequency power could help to address this situation. The new-generation electric glass melting systems — that replace the older, more inefficient, and high emissions furnaces — can easily fit into existing plant real estate and become the new standard for both brownfield sites and greenfield builds.
Regardless of the chosen new energy approach, next-generation glass plant infrastructures must be digital to be efficient. Artificial intelligence (AI) and advanced control help glass industry players move faster with higher yields. This enhanced flexibility drives competitiveness through lower energy operational expenditure (OpEx) while keeping an eye on lower emissions and preserving the social license to operate.
Working with the right partner can accelerate the transition
Innovative solutions are available today to help address decarbonization challenges. But ushering in these solutions will require upgrades to electrical infrastructure. With energy demand soaring, medium-voltage power and control systems must become high-voltage.
Today’s glass plant operations need more power available on-site and sufficient hydrogen, biogas, or syntactic fuels. As specialists in energy management, Schneider Electric is in a strong position to help glass manufacturers transition to digital operations and renewable energy. Our experts assess energy consumption reduction opportunities and help you minimize energy transition risks.
To learn how your organization can reduce energy costs while lowering carbon emissions, download our Green Glass Transformation handout.
This article was previously published in Glass Worldwide
Add a comment