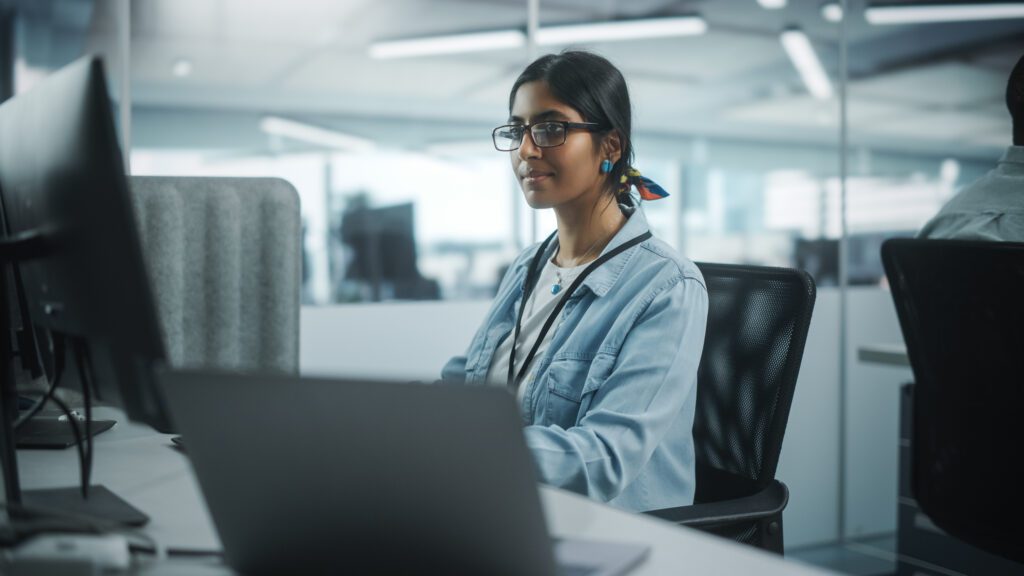
Technical advancements have propelled industries to improve output and enhance productivity. There are a variety of electrical components that work coherently to make industries better every day. Programmable logic controllers are one such component that has been used extensively in the industrial landscape. It has significantly improved manufacturing processes and facilitated effective control of assembly lines, robotic devices, machines, and other devices that need to run at their reliable best. Ladder logic programming is the language that helps in constructing software and programs for PLC controllers. It presents the program in the form of ladder diagrams that are based on circuit illustrations. This article gives a comprehensive view of ladder logic programming and its benefits in the industrial space.
What is ladder logic programming?
Ladder logic programming is a visual representation used in programmable logic controllers to control machinery and processes. For example, it can manage a conveyor belt system by controlling motor start/stop operations based on sensor inputs.
Ladder logic is a rule-based language that was traditionally leveraged to document the construction and design of relay racks in industrial processes. An individual relay rack was represented on the ladder diagram by a symbol. The symbol would further be connected to devices below that would appear as vertical rails.
An individual rung on the ladder presents a specific rule which is executed simultaneously when implemented to relays and other electromechanical devices. When the ladder logic program is applied to programmable logic controllers, the execution happens sequentially in a continuous loop with the help of software.
The importance of ladder logic programming in industrial space
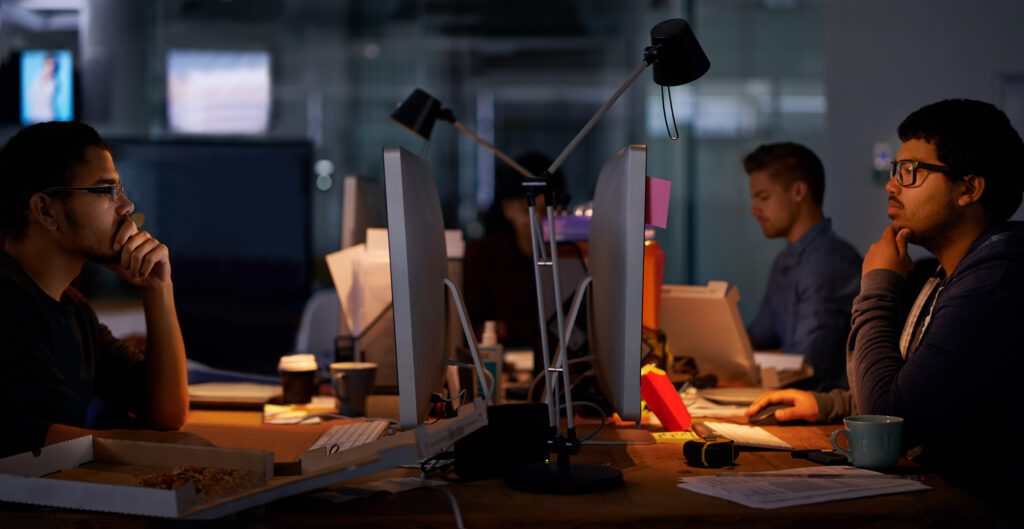
Ladder logic programming is used in the industrial environment to program PLCs for sequential control of manufacturing operations. As a programming language, ladder logic holds great importance in the industrial space.
- It is a programming language that is crucial to program critical functions from scratch or rework traditional hard-wired systems and help them transform into new programmable versions.
- Ladder logic programming is also leveraged in sophisticated automation systems such as car or electronics factories.
- The use of familiar engineering symbols makes ladder logic programming seamless to use. People without an official background in programming can also easily program and implement in industrial operations.
Basics of ladder logic programming
Ladder logic programming is a graphical programming language widely used in industrial automation and control systems. Its name comes from it’s the visual resemblance to a ladder, with horizontal rungs and vertical rails. This programming language is integral to operating programmable logic controllers (PLCs). They help in manufacturing, processing, and other industries to automate and control various processes.
Ladder logic is designed to model and control the behavior of electromechanical systems utilizing a series of interconnected relays, switches, and coils. It provides a straightforward way to represent complex control sequences and logic functions, making it an effective tool for designing and implementing automation solutions.
At its core, ladder logic programming revolves around the concept of logic gates. These gates, such as AND, OR, NOT, and XOR, enable the creation of logical conditions. They determine the state of output devices based on input conditions. In Ladder Logic, inputs are typically represented by normally open (NO) and normally closed (NC) contacts, while coils or relays represent outputs.
Here’s a breakdown of the basic elements and principles of ladder logic programming:
- Rungs
Ladder logic programs consist of one or more rungs, each representing a specific control sequence. A rung typically contains a combination of input contacts and output coils connected in series or parallel using logic gates.
- Contacts
Contacts are symbols that represent the status of input devices, such as sensors, switches, or other control signals. A normally open (NO) contact represents a true condition when the input is active, while a normally closed (NC) contact represents a true condition when the input is inactive.
- Coils
Coils are symbols that represent output devices, such as solenoids, motors, or relays. When the logic conditions in a rung are met, the associated coil will be energized, activating the output device.
- Logic Gates
Logic gates are there to combine or modify input conditions to create more complex logical operations. AND gates require all input conditions to be true; OR gates require at least one input to be true, and NOT gates invert the input condition.
- Control Flow
The flow of control within a ladder logic program is top-to-bottom and left-to-right. Each rung is evaluated sequentially, and the outputs are updated based on the logic conditions met in each rung.
- Programming Conventions
Ladder logic programming follows specific conventions, such as using horizontal rungs for parallel connections and vertical rails for series connections. This visual layout aids in creating a clear representation of the control logic.
- Reliability and Safety
Ladder logic’s origins in relay-based control systems contribute to its reliability and safety. It is widely used in critical applications where precise control and fail-safe operation are crucial.
Ladder logic programming provides a user-friendly and intuitive method for designing control sequences and automating processes in various industries. Its graphical representation and logical approach make it accessible to both engineers and technicians, allowing them to create complex automation solutions with ease. As industries continue to evolve in the new digital world, ladder logic remains a fundamental tool in the realm of industrial automation and control.
How ladder logic programming works
Ladder logic is a programming language commonly used in industrial automation and control systems. It operates on the principle of emulating relay logic circuits, which were historically used to control electromechanical systems. Ladder logic programming allows engineers and technicians to design and implement control sequences for various processes and machines visually and intuitively.
At its core, ladder logic programming resembles a ladder with two vertical rails representing the power supply and horizontal rungs that house different control elements. These control elements, often referred to as “contacts” and “coils,” mirror the behavior of physical relays and switches. Contacts act as input conditions or sensors, while coils represent the output or actuator devices. The logic flow is read from left to right, and the state of each element (either open or closed) determines the path that the control logic follows.
The programming process involves arranging these contacts and coils in a way that defines the desired sequence of operations. When an input condition is met (a contact “closes”), it allows the logic flow to proceed to the next rung, where output actions can be triggered (a coil energizes). This mimics the behavior of activated relays and switches based on specific conditions.
Ladder logic programming is particularly suited for applications requiring sequential or discrete control, such as manufacturing lines, process control, and machinery automation. Its graphical representation simplifies troubleshooting and modification, as engineers can easily visualize the logic flow and make adjustments accordingly. Despite its visual simplicity, ladder logic can handle complex control sequences, making it a versatile tool in the realm of industrial automation. In summary, ladder logic programming provides a bridge between the digital world of computers and the physical world of machinery. It enables efficient and effective control of processes in industries ranging from manufacturing and automotive to energy and beyond.
The underlying structure of ladder logic programming is based on the electrical ladder diagrams that were traditionally used in relay logic. These diagrams were used to document how the connections were made between the devices on relay panels. The moniker ‘ladder’ diagrams were used as the diagrams were constructed in a way that signified a ladder having two vertical rails and a rung between them. The positive power rail to the left would flow to the negative power rail to the right with the help of the physical devices that were connected on the rung.
Before executing any programmed logic, the CPU assesses the physical inputs and outputs that are connected to the input and output modules to update their status in the memory table.
Once the inputs and outputs are duly assessed, the CPU would execute every specific rung or sub-rung rung from left to right. As the CPU reaches the last rung, it updates the real-world outputs and loops to run everything again. The entire execution process will continue for as long as the CPU is powered and on RUN mode.
Benefits of ladder logic programming
- Ladder logic programming is intuitive and provides an excellent graphical representation of the entire circuit design. The highly intuitive nature of the language makes it exceptionally easy for professionals to understand its language. Without prior experience in software training, industrial operators can also leverage ladder logic programming to debug or maintain industrial applications.
- Ladder logic programming allows operators to have a graphical view of the power flow. This makes it exceptionally easy to debug power faults.
- The circuits that are created while using ladder logic programming are easy and more reliable than complex electrical components. This leads to an apparent improvement in the life of all the connected equipment
Advanced circuit branching ladder logic practice
Advanced circuit branching in ladder logic programming involves creating complex control systems by using branches in ladder logic. This technique allows for simultaneous control of multiple operations within a single program. It involves the use of parallel paths (branches) that can operate independently or interact with each other, depending on the circuit’s design and requirements. This approach enhances flexibility and functionality in automation processes, enabling more sophisticated control solutions for machinery and systems.
How limit switches are used with PLC ladder logic programming
In PLC ladder logic programming, limit switches are used as input devices to signal the position of machinery components. When a machine part reaches a specific point, the limit switch activates, sending a signal to the PLC. This input is represented in ladder logic as a contact, which can then control the operation of output devices like motors or valves. By integrating limit switches, ladder logic programs can effectively manage and automate mechanical processes, ensuring precise control and operational safety.
Future trends in ladder logic automation
Ladder logic programming is evolving with advancements in smart technologies. Integrating IoT and AI has improved predictive maintenance and operational efficiency. Future trends include increased use of wireless communication, improved diagnostics, cloud connectivity, real-time data analytics, and seamless integration with other automation systems. It makes industrial processes more intelligent, adaptive, and responsive to changing conditions.
Enhance your industrial facility with Schneider Electric
Schneider Electric’s exceptional offerings empower enterprises to make the most of the available energy and resources. Our expertise seeks to bridge the gap between progress and sustainability. The belief system at Schneider Electric revolves around providing the population with equal access to digital and energy. With the current generation facing an aggressive transition in energy and industry, electricity is regarded as the primary vector for decarbonization.
We take the role of a digital partner to help you and your enterprise achieve your sustainability goals. We integrate industry-leading energy technologies and processes to help your business realize its complete potential and identify opportunities for sustainability.
Under our sustainability initiatives, we contribute toward the United Nations Sustainable Development goals. The six long-term commitments solidify our stance on going the extra mile for the environment, economy, and society. Through our commitments, we act for a sustainable world, become efficient with resources, live up to our principles and trust, curate equal opportunities, empower local communities, and harness the power of all generations.
Schneider Electric’s innovative solutions have delivered immediate decarbonization. 40% of Italy’s energy has been made renewable with the help of Schneider’s EcoStruxure Smart Grid. Moreover, the Climate Group recognized us as the first Clean Energy Trailblazer in 2020. Schneider Electric’s Access to Energy program provided solar streetlights in Tapachula, Mexico, improving security for thousands of refugees.
With our ladder logic programming solutions, industrial operators can seamlessly optimize their operations and tune them for efficiency. The complete control over the logic controllers helps significantly improve output and allows industry owners to reduce a plethora of costs.
Conversation
Thanks for the good training and simple explanation