This audio was created using Microsoft Azure Speech Services
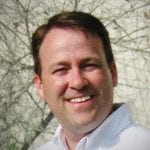
Matt Lawson is the Director of Technical Operations at MDT Software. Matt has 23 years of experience in a variety of engineering roles, many within automation manufacturing industry. He holds an Electrical Engineering degree from the Georgia Institute of Technology. Matt began his career as a Project Engineer and has held increasingly responsible positions in manufacturing engineering, software development and product/project management.
Is your plant protected by against human error, equipment failure, etc.? Who is making changes to the automation devices in your plant? Where is the latest version of the device program? What changes have been made to your device programs?
If any of these questions cannot be easily answered, your plant is at risk for downtime, product loss, safety hazards, security breaches, loss of intellectual property and more. The increased use of plant floor automation to achieve production goals has created a dependency on industrial programmable devices such as PLC, CNC, HMI, Robots and drives. Many of these programs are changed as adjustments to variables and logic are needed to continue smooth operation, but these changes also put the plant at risk. What happens if someone makes a change to a program that results in undesired performance, or corrupts the program due to inadvertent changes? If there is no backup the result is costly downtime.
For example, take one particular large soft drink manufacturing plant, producing up to 4,000 cans per minute and 3,280 bottles of soft drinks per minute, that followed a manual, human driven change management process. The procedure included using two separate back-up systems: a ‘master’ and a ‘working’ system based on manually copied files. Technicians changed PLC code locally and then followed a set of procedures to ensure the change was recorded and backed-up, making the plant very vulnerable to human error. This plant unfortunately discovered that if a change was unauthorized or the engineer simply forgot to save the change to the main back-up file, version control issues resulted. If just one production line went down because a PLC has fallen over due to poor software version control, the plant was faced with downtime costs of around $1,800 per minute.
To avoid future costly errors related to version control, this plant installed a Change Management System (CMS) to maintain an ancestor history of all PLC and non-PLC files on site. Particularly useful to the plant is the CMS’ schedule compare feature that automatically compares the program in the device with a stored program. This feature detects and identifies changes between the programs so that designated users are immediately notified of changes that may have been unknown or unauthorized.
Shortly after installing the CMS, the plant had a problem with a PLC controlling the water treatment plant resulting in all the PLC’s code to be lost, stopping all water supplies to the production process. Production was up and running within five minutes by downloading the correct code from the CMS program repository. On another occasion, the main preparation PLC fell over. The code was reloaded immediately over the network from the CMS and the plant incurred no downtime. In both cases, the reloaded code was up-to-date due to the schedule compare capability which updates the ancestor files if discrepancies are found during the compare routines. Few discrepancies are now detected, as the on-site technicians now use the CMS for checking out programs and verifying them again when making a new revision.
In a world where mistakes and unexpected failures never happen, an Automation CMS would not be necessary. Since that world does not exist, having a CMS is an imperative.
MDT Software is a world leader in change management solutions for automated manufacturing devices. MDT’s flagship product, AutoSave, empowers users to protect, save, restore, discover, and track changes in industrial programmable devices and plant-floor documents. AutoSave is considered the corporate standard for plant automation device management in many of the most advanced manufacturing facilities in the world and is used by industry leaders such as Abbott Nutrition, Chevron, Ford, General Mills, Johnson & Johnson, Nestlé, Rio Tinto and Toyota. For more information on MDT and AutoSave, visit www.MDT-Software.com.
In order to provide an accurate solution for efficient industry, Schneider Electric needs to be connected with the best experts of the market. The Collaborative Automation Partner Program contributes to build a complete business solution by selecting and integrating technology partner’s solutions to Schneider Electric offer. Today, CAPP portfolio includes almost 50 Technology Partners spread in 3 categories: Interconnection of Architectures, Application for Solution and Complete Lifecycle Integrated. When partnering with a company, the program selects and tests targeted products from the Technology Partner that will complete Schneider Electric Industry Business Unit solution. You can find more information about the portfolio on our website.
Conversation
Zequek Estrada
8 years ago
Matt, I think you make a great point about the importance of taking safety precautions to protect your manufacturing plant. From what I’ve heard, maintaining routine maintenance is a great way of ensuring that everything has a longer lifespan. It seems like when it comes to heavy construction or industrial equipment, it’s the simple things that tend to make a difference in the long run.