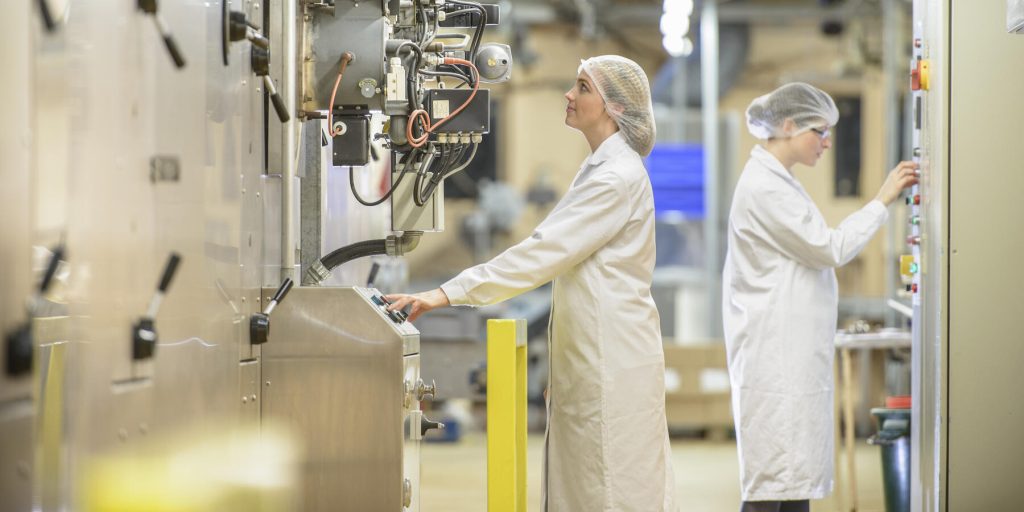
Decarbonization is essential for the food and beverage industry. Consumers everywhere are demanding more product variety, food safety, increasing regulation, and improved environmental and sustainability performance. These are not small challenges. The food and beverage segment currently uses about 30% of total global energy and is responsible for about 20% of greenhouse gas (GHG) emissions.
At the same time, base costs for food are skyrocketing, with farmland shrinking and climate change decreasing agricultural outputs. Profit margins are typically narrow, so food and beverage companies face significant financial and operational constraints as they try to adjust to the changing market, make strong inroads to reduce carbon emissions, and achieve their sustainability commitments.
The food and beverage (F&B) industry is making strong movements to reduce carbon emissions and achieve its sustainability commitments to mitigate the impact on consumers and stakeholders.
Decarbonizing food and beverage operations is crucial to achieving both long-term sustainability and financial goals. But it is complex. It requires more than simply investing in green energy through a utility supplier or on-site microgrid. The biggest potential impact is modernizing manufacturing facility processes, increasing safety, and improving overall energy, waste, and water usage efficiency.
Energy-intensive processes, like baking, pasteurization, and sterilization, are essential for safe and effective food and beverage manufacturing and are mandatory for meeting customer demands and regulatory requirements for food safety. Traditionally, these processes were more energy- and cost-efficient when powered directly by fossil fuels rather than electric energy generated from fossil fuels due to losses as the electricity is transported across the grid.
But now, with the growing availability of green or renewable energy sources from utilities, coupled with on-site solar or wind microgrid options, F&B companies have opportunities for progress and improved performance. On-site renewables also offer improved resiliency and business continuity options as they can improve power availability during periods of extreme weather or other grid-impacting incidents. Improved energy management in the facility also allows for financial benefits, such as participation in a utility’s demand management scheme or even selling energy back to the grid during peak demand periods.
Electricity 4.0: Driving processes toward sustainability
Sustainability requires more than adopting green energy sources or replacing boilers with heat pumps. To become truly sustainable, companies need a clearer understanding of their operations. They require deeper insights into their plants, process lines, and machines to more fully comprehend how their energy usage affects not only product cost and carbon emissions but also operational efficiency, product quality, operator safety, and customer satisfaction.
Just as Industry 4.0 describes the use of internet-enabled devices and cloud computing to digitize industrial operations, Electricity 4.0 is the integration of this same kind of technology into electrical systems. It provides facility owners and managers with key information to make informed, data-driven decisions about energy usage and their net-zero journey.
The value of digital data
Having a digitalized electrical system provides significant benefits to food and beverage companies to help them:
- Provide the data needed to lower utility costs for energy, water, and waste management.
- Increase operational yields and efficiency by leveraging actionable system insights, with up to 40% more flexibility to boost competitiveness.
- Maximize asset value, performance, and lifetime, with up to 30% savings on capital expenditures and the potential for higher share values.
- Improve electrical safety and availability, enhance quality, and ensure regulatory compliance. For example, it can reduce data collection time by as much as 99%, making tracking and reporting on food safety compliance easier.
- Increase traceability during incidents to reduce negative brand equity or share value impacts.
- Expand data access to empower plant workers, giving them better information for improved decision-making, which can cut incident response times in half.
- Demonstrate GHG emission reductions when energy is sourced from renewable generation for regulatory compliance.
What Electricity 4.0 delivers
A digitalized electrical distribution solution should provide functionality to deliver operational outcomes, including:
Improved electrical system management
- Electrical distribution monitoring, alarming, and event analysis
- Power quality monitoring, simulation, and compliance
- Continuous thermal monitoring and arc flash protection
Advanced software analytics and simulations
- Predictive simulations or digital twin technologies
- Energy monitoring, modeling, and usage analysis, including benchmarking
- Electrical network short circuit and breaker selectivity simulation
- Network load flow and voltage drop simulation
- Capacity management
Sustainability monitoring, reporting, and consulting
- Energy efficiency compliance monitoring and reporting
- Carbon neutrality consulting and GHG reporting
Beyond the specific features, one of the biggest benefits of a digitalized electrical system is that it combines information about power and process. This provides a unified view of the entire operation, allowing facility owners to make investment and operational decisions with a holistic, sustainable performance approach.
The value of partnership
Starting the transformation may seem daunting, but many F&B manufacturers find working with partners cost-effective to ensure peace of mind on their digitalization journey. Make sure to choose an established company with a proven track record deploying sustainability solutions within the food and beverage industry.
Schneider Electric, a leader in energy management, automation, and digitalization, collaborates with AVEVA’s industrial software and digital transformation expertise to create a powerful synergy to address complex F&B manufacturing challenges. Our collaborative approach and advisory capabilities equip companies with cutting-edge technologies, data-driven insights, and best practices to help them achieve sustainability goals, improve operational performance, and stay competitive.
For more information
To learn more about how Electricity 4.0 and electrical network digitalization can provide a clear path forward to decarbonization, please check out our new reference guide, EcoStruxure™ Power for Food & Beverage Plants.
Add a comment