This audio was created using Microsoft Azure Speech Services
The integration of artificial intelligence (AI) and machine learning (ML) into manufacturing processes represents a significant leap forward for the industry. As manufacturers continuously seek methods to enhance efficiency and reduce operational costs, the optimization of chemical additives has emerged as a promising area.
Chemical additives like biocides, antifouling agents, surfactants, and flocculants are vital in many manufacturing operations. However, these additives are often costly, and optimizing their use can yield substantial savings, particularly in continuous processes.
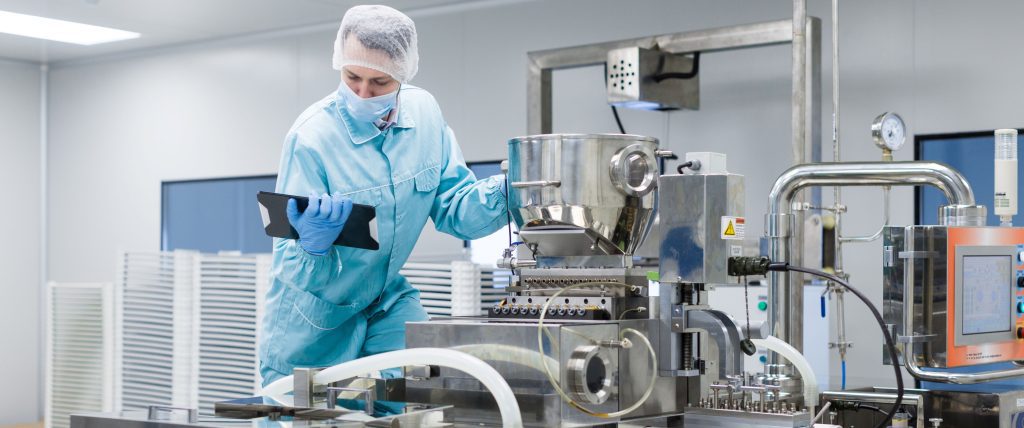
What is chemical additive optimization?
Chemical additives play a crucial role in enhancing the efficiency and performance of manufacturing processes. Despite their importance, the management and optimization of these additives have traditionally been handled manually or semi-automatically, often relying on the expertise of chemical sales representatives or support from suppliers.
This approach is rarely optimized for cost efficiency.
With the advent of AI and ML, there is now the potential to recommend optimal dosages for chemical additives based on real-time operating conditions, leading to considerable savings and improved process efficiency.
Using AI at a seawater desalination plant
A compelling proof of concept was recently demonstrated in a modern reverse osmosis (RO) desalination plant’s pretreatment unit. The pretreatment unit’s primary function is to remove large particles and debris, thereby extending the lifespan and efficiency of the RO membranes. The typical chemical additives used in this process include biocides, coagulants, and flocculants. Since biocides are dosed intermittently, the optimization focused on coagulants and flocculants.
In this case study, AI-driven models help determine the optimal dosages of coagulants and flocculants. By analyzing historical data and real-time operational conditions, the AI system could predict the most effective and efficient use of these chemicals. This resulted in cost savings while also maintaining the high quality of the desalinated water.
3 approaches for AI/ML modeling
The modeling phase involved developing a predictive model and an operational window model, then combining these through an ensembled approach.
Predictive Model
The predictive model aims to forecast key performance indicators (KPI) based on decisional variables and state variables as inputs.
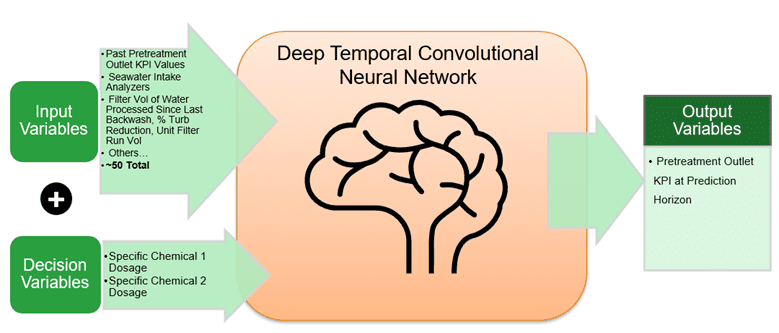
This model uses a constrained black-box optimization method to provide optimal recommendations for the decision variables. After testing several Deep Neural Network and Temporal Convolutional Network structures, the best-performing model was a modified Deep Temporal Convolutional Neural Network (DTCNN) based on the WaveNet structure, achieving an R2 score of 0.921.
The DTCNN model’s success underscores the potential of advanced neural network architectures in processing and predicting complex manufacturing processes. This model can handle the temporal dependencies and high-dimensional data typical of industrial operations, making it a robust tool for optimizing chemical additive use.
Operational Window Model
The operational window model identifies optimal operational modes through clustering methods such as Bayesian Gaussian Mixture Models. Each cluster represents a different operational mode for the plant, and uses the best historical performance within each mode to guide current recommendations. This model provides robust recommendations grounded in past performance, making it easier for plant operations to accept and implement.
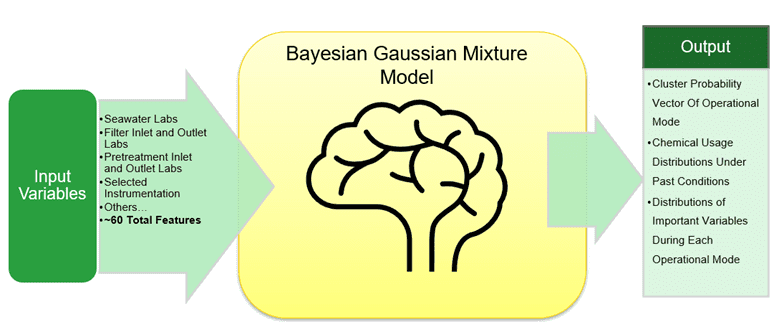
The operational window model’s strength lies in its ability to contextualize current operations within a framework of past performance. By doing so, it provides practical, data-driven recommendations that operators can trust because they are fully explainable. In turn, it thereby facilitating smoother implementation and better adherence to optimal operational practices.
Ensemble Approach
The ensemble approach combines the predictive model and the operational window model to provide a more balanced and robust recommendation.
This method leverages high-availability sensor data and laboratory values from the operational window model and high-frequency DCS data from the predictive model. Separating the inputs based on availability allows for a model that can produce an accurate recommendation. This is true even in situations where some of the more complex instrumentation is unavailable. The recommendations from both models combine together and use an affine sum. This allows for adjustable and robust outputs.
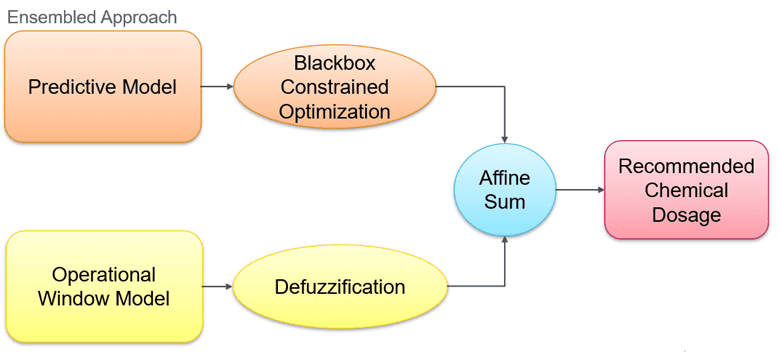
The ensemble method ensures that the recommendations are not only accurate but also resilient to changes in operating conditions. This adaptability is crucial in dynamic manufacturing environments where conditions can fluctuate rapidly.
AI-driven optimization gives companies a competitive edge
The application of AI/ML to optimize chemical additives in the manufacturing process has shown promising results. Markedly, in the case of the reverse osmosis desalination plant, the optimized dosages of coagulants and flocculants led to significant cost savings and improved operational efficiency. The ensembled approach provided a tunable and robust system. This way, it could adapt to varying operational conditions and maintain high levels of performance.
The cost savings achieved through AI-driven optimization were significant, demonstrating the economic viability of such advanced technologies. Additionally, the enhanced operational efficiency contributed to prolonged equipment lifespan and reduced maintenance costs. This further emphasized the benefits of integrating AI into manufacturing processes.
The success of this proof of concept opens the door to broader applications of AI/ML in manufacturing processes. Overall, as AI/ML models become more sophisticated and data collection techniques continue to improve, the potential for cost savings and efficiency gains across various manufacturing sectors is substantial. The integration of AI-driven optimization can lead to more sustainable and economically viable manufacturing practices, driving innovation and competitiveness in the industry.
Moreover, AI’s ability to process vast amounts of data and uncover patterns not immediately evident to human operators can lead to the discovery of new efficiencies and operational strategies. This not only improves current processes but also fosters a culture of continuous improvement and innovation within manufacturing organizations.
Optimizing your processes with AI
The use of AI and machine learning for chemical additive optimization in manufacturing processes represents a significant advancement in industrial operations. The approach not only reduces costs but also enhances the efficiency and sustainability of manufacturing processes. Likewise, these technologies will continue to evolve and their impact on manufacturing will grow. Subsequently, this will pave the way for smarter and more efficient industrial practices.
The future of manufacturing lies in harnessing the power of AI and ML to not only optimize processes but also to innovate and stay ahead in a competitive landscape. With continued advancements and broader adoption, AI-driven optimization will undoubtedly become a cornerstone of modern manufacturing. It will revolutionize how we produce goods and manage resources.
Embracing AI and ML in manufacturing is not just about keeping pace with technological advancements. It’s about leading the charge towards a more efficient, sustainable, and competitive industrial future. Talk to our experts about how AI-driven optimization can transform your manufacturing processes by contacting Josh Galloway, Chennan Li or by visiting the Schneider Electric AI Hub.
Add a comment