At the start of Europe’s current energy crisis, Germany sought an alternative solution. The government would work with Wilhelmshaven to build a floating liquefied natural gas (LNG) shipping terminal— the nation’s first such facility. The terminal project, also known as a floating storage regasification unit (FSRU), was built at a breakneck pace. It accepted its first shipment less than nine months later.
“When we work together, we can do things at great speed,” said German Chancellor Olaf Scholz, during the FSRU’s opening ceremony. “That’s Germany’s new tempo.”

This terminal is a key component in the country’s quest to diversify its gas supplier base and lay the groundwork for some of its future sustainable energy initiatives. The project demonstrates how collaboration between governments and industry partners can deliver innovative solutions to support energy independence.
Natural gas supply under stress
Natural gas comprised 27% of Germany’s energy mix, with more than half sourced from Russian pipelines. Growing geopolitical tensions steadily reduced supplies. This meant conservation measures were unlikely to fill the gap and prevent rationing. Subsequently, gas prices quadrupled, imperiling industrial production, electricity generation, and private household heating.
Germany needed access to additional gas sources quickly. An FSRU was the answer. It offered much lower costs for construction and faster completion times. This ability to import and offload LNG from dependable nations through FSRUs was an opportunity to rapidly diversify their energy needs.
If necessary, an FSRU can be relocated or repurposed into an LNG carrier. Approvals were swiftly granted and the location chosen. It became essential for the government and the supplier industry to examine how to transform old collaboration models. Doing so helped achieve aggressive construction deadlines.
Industrial automation, a key enabler for high-performance LNG facilities
With the support of the Federal Government of Germany, Wilhelmshaven was selected due to being Germany’s only deep-water port capable of allowing large tankers to dock and transship independently of tidal conditions. The terminal facility, owned by international power provider and leading European gas supplier Uniper Energy, includes berthing facilities and a high-pressure loading platform for LNG tanker docking.
The FSRU consists of storage tanks and regasification machinery connected to an onshore transshipment jetty. (This is linked to Germany’s long-distance gas transmission network via 26 kilometers of new pipeline).
The LNG regasification process at the terminal is complex, requiring several pumps, compressors, chillers, and motor starters. An intricate network of pipes and valves further helps ensure the supercooled liquid is efficiently and precisely converted back to a gaseous form.
With the inherent risks associated with processing volatile petrochemicals, the Wilhelmshaven terminal (and the energies and chemicals industry in general) required industrial automation and process safety technology to monitor, coordinate, and optimize production processes with extraordinary precision to help ensure:
- Peak operational performance and profitability
- Personnel safety
- Environmental regulation compliance

Continuous monitoring, management, and optimization of the high-value assets used in Energies and Chemicals production processes require a state-of-the-art distributed control system (DCS) and safety instrumented system. For the Wilhelmshaven terminal project, Uniper chose:
- EcoStruxure™ Foxboro DCS technology to automate industrial monitoring and control
- EcoStruxure Triconex™ Safety Instrumented System (SIS) to help protect workers and plant assets
The Triconex SIS offers flexibility and adaptability to scale as needed. Such versatile architectures can help save on installation costs and engineering time. Triconex is also compliant with the IEC 62443 cybersecurity standard, enabling robust safety and high levels of integrity and resilience.
Collaboration addresses four key implementation challenges
Once the Wilhelmshaven terminal build decision was made, it was “all hands on deck” for every stakeholder. Close collaboration between government, suppliers, and construction teams helped keep the project on schedule. Commitments were made to explore co-innovations to uniquely resolve potential delays and difficulties, including:
- Compressed project timelines – Project management, engineering, and installation teams leveraged extensive system design and strategic planning experience to streamline system installation. Schneider and Uniper exceeded the project’s aggressive 10-month completion schedule. Engineering optimized DCS and SIS solutions and developing a logistical implementation plan helped overcome supply chain constraints and accelerate system testing, commissioning, and training.
- Harsh environmental conditions – Energies and chemicals applications, particularly marine environments, present unique challenges for electronic systems (e.g., humidity and salty air). The terminal’s temperature, vibration, particulate, humidity, and corrosive conditions were modeled into system design parameters. This helps ensure the DCS and SIS modules and components were robust and able to perform per specifications. With just one hour of lost LNG production costing as much as $1,250,000, maintaining operations and ensuring quick, safe equipment restarts was crucial.
- Third-party equipment and system integration – With multiple vendors providing equipment, it was essential for the DCS to seamlessly integrate data from sensors, smart devices, and subsystems provided by external suppliers. The EcoStruxure ecosystem also utilizes an open, standardized, flexible, object‑based architecture that enables plug‑and‑play interoperability and straightforward third-party equipment integration.
- Cybersecurity – With the increasing use of digital technologies to better manage operations and distribution networks, cyberattack threats present a greater risk to critical infrastructure than ever. Cybersecurity, regulatory compliance, and remote network access for Wilhelmshaven were all enhanced. The terminal’s unique network security needs were achieved through robust system hardening, firewalls, expert consultation, and a demilitarized zone (DMZ ) perimeter network. Implementing network-attached storage and integrating Claroty SRA met the terminal’s unique network security needs.
A greener future for Wilhelmshaven
Since its commissioning on December 21, 2022:
- The terminal has been running safely, efficiently, and virtually nonstop
- 42 LNG carriers have delivered around seven million cubic meters of LNG
- 6% of Germany’s total gas consumption was supplied by the terminal in 2023
With the floating LNG terminal in full operation, Uniper is already planning energy transformation hubs. Such hubs can diversify energy imports and examine how the Wilhelmshaven site (and its surrounding region) can further contribute to a climate-neutral energy supply. In turn, this will help generate green gases and renewable energies, with:
- A large-scale electrolysis plant on the former Wilhemshaven power plant site
- An ammonia import terminal near the current LNG facility
- Solar and wind power plants
The future of Green Wilhelmshaven looks bright.
Learn how Triconex and Foxboro DCS can help your process control, process safety, and industrial automation challenges.
About the author
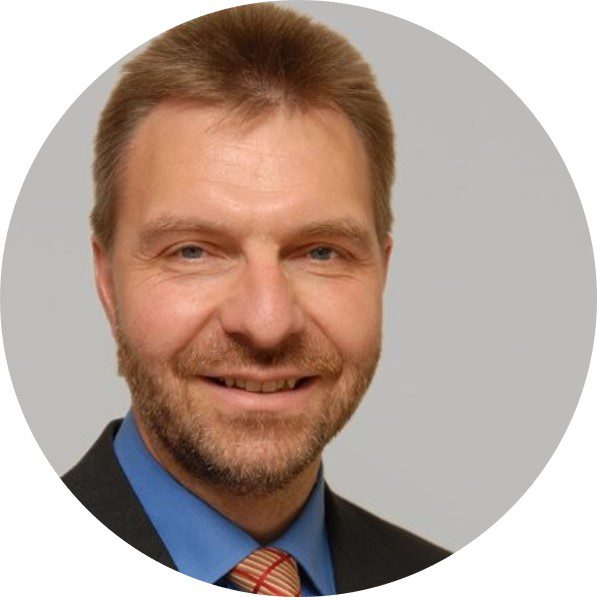
Frank Ogrissek, Customer Sales Executive
Frank is an automation and electrical sales consultant who has served in global and national roles for over 30 years. He graduated from RWTH Aachen University in 1988, and has been working with Schneider Electric since 1997.
Add a comment