Imagine a world where machines never fail unexpectedly, production lines run smoothly without unscheduled stops, and maintenance is so efficient it feels almost invisible. This isn’t the distant future—it’s a reality on the brink, thanks to the shift from corrective and calendar-based maintenance to preventive and predictive condition-based maintenance (CBM).
Why maintenance matters more than ever
In today’s fast-paced industrial world, unplanned equipment downtime can wreak havoc on operational efficiency. It’s not just an inconvenience but a potential catastrophe leading to lost productivity, increased costs, and even safety hazards. Traditionally, companies have relied on two primary maintenance strategies: corrective, which deals with repairs after a failure, and calendar-based, which schedules maintenance at fixed intervals. While these methods have served industries for decades, they are far from perfect.
Corrective vs. calendar-based maintenance: Outdated approaches
Corrective maintenance, although effective in getting failed equipment back online, often results in production halts, higher repair costs, and sometimes catastrophic failures. Calendar-based maintenance, on the other hand, can feel like changing your car’s oil every month, regardless of how much you’ve driven. It’s both wasteful and inefficient.
So, what’s the solution? Enter Preventive and Predictive CBM.
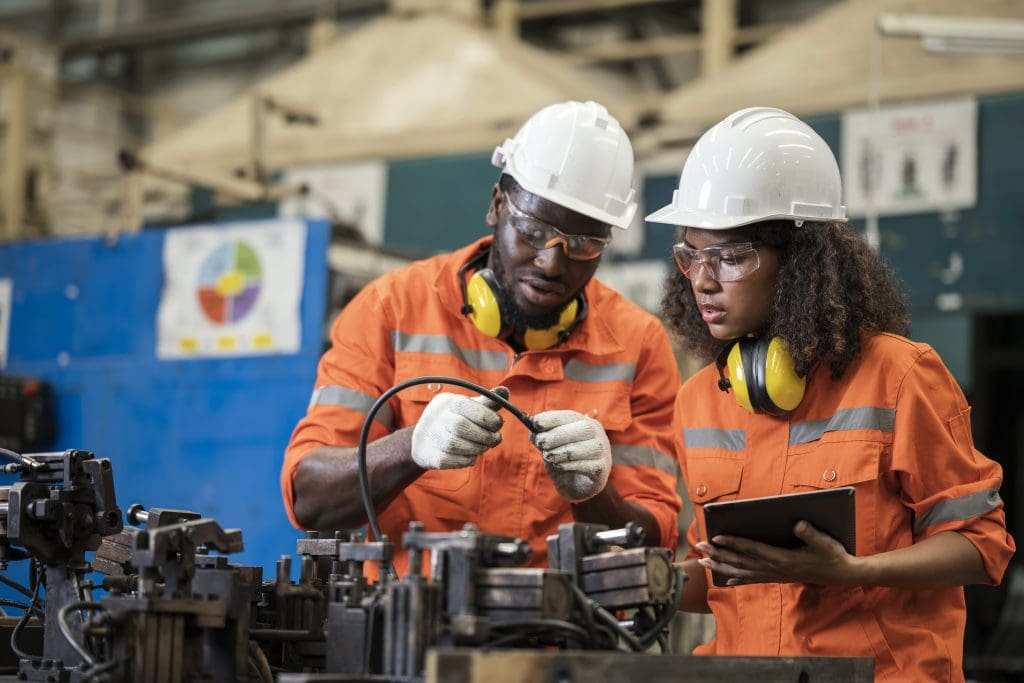
The power of Preventive and Predictive CBM
Predictive CBM focuses on regularly scheduled maintenance based on time or usage statistics. CBM takes it a step further, using real-time data and advanced analytics to foresee when a machine is likely to fail, allowing for maintenance to be performed just in time to prevent a breakdown.
Benefits of CBM
- Increased equipment longevity: By addressing issues before they lead to failures, both preventive and predictive maintenance extend the life of equipment, saving companies money in the long run.
- Enhanced efficiency: Predictive maintenance reduces downtime, ensuring that machines are only taken offline when absolutely necessary, leading to more consistent production rates.
- Cost savings: While there might be initial costs associated with implementing CBM technologies, the reduction in unexpected repairs, decreased downtime, and increased equipment lifespan translate to significant savings over time.
- Increased safety and sustainability: Proactively maintaining equipment helps prevent failures that could result in dangerous situations or environmental damage, aligning with high ethical standards and sustainability goals.
CBM success stories
Consider a leading global manufacturer that transitioned to predictive maintenance for its extensive fleet of machines. Utilizing sensors and AI algorithms, they could predict equipment failures weeks before they occurred. This not only reduced downtime by 30% but also cut maintenance costs by 40%.
Similarly, a large energy company implemented CBM to monitor its wind turbines. Predictive analytics allowed them to anticipate mechanical issues, leading to a 20% increase in energy production efficiency. Such examples underline the tangible benefits of adopting CBM strategies.
Actionable insights for transitioning to CBM
Making the shift to CBM is a journey, but here are some tips to get started:
- Leverage data analytics: Invest in data analytics tools that can process vast amounts of operational data and identify patterns indicating potential failures.
- Implement IoT sensors: Equip machinery with Internet of Things (IoT) sensors to collect real-time data on equipment health and performance.
- Invest in Staff Training: Ensure your maintenance team is trained in the new technologies and analytical methods required for CBM.
- Partner with experts: Collaborate with technology providers and experts who can help you design and implement a CBM strategy tailored to your specific needs.
Schneider Electric’s EcoCare Services membership can support this transition by providing tailored maintenance solutions and expert insights. With EcoCare, facilities gain access to advanced diagnostic tools, comprehensive training programs, and dedicated support teams. This membership ensures that the journey from calendar-based shutdowns to predictive maintenance is not just smooth but also guided by the latest innovations and highest ethical standards in the industry. EcoCare Services empower facilities to become more resilient, efficient, and sustainable, paving the way for a future where preventive and predictive maintenance is the standard.
Looking forward, more resilient and efficient operations
The evolution from corrective/repair and calendar-based maintenance to CBM is not just about technology; it’s about a future where we can enhance efficiency, ensure sustainability, and empower industries to operate at their best.
By adopting CBM, we not only prepare ourselves for a more efficient future but also pave the way for resilient and sustainable, industrial growth.
So, let’s take that proactive step forward. The future of maintenance doesn’t wait—it predicts, prevents, and preserves.
About the author
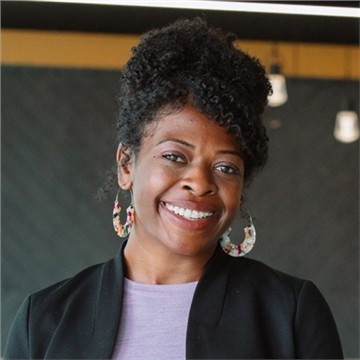
India Gibson,
Product Marketing & Management – Senior Professional
India Gibson is the EcoCare Services Launch Leader in NAM and leads with a wealth of experience gained from previous roles, including Advanced Product Owner and Scrum Master driving digital transformation for Schneider Electric.
Add a comment