Efficiency, sustainability, and safety are crucial for operations, meaning the annual maintenance shutdown of your facility should be more than just a routine check. Shutdowns give operators the chance to ensure peak performance, longevity, and a commitment to environmental responsibility. Use the following 11 steps to streamline your annual maintenance shutdown.
Step 1: Plan ahead
Preparation is the key to a successful maintenance shutdown. Start planning several months in advance. Assemble a team, define clear objectives, and establish a timeline. This will ensure that everyone is on the same page and that the shutdown is executed smoothly and efficiently.
Step 2: Take inventory
Conduct a thorough inventory of all equipment and materials necessary for the shutdown. Procure any required components in advance to avoid delays. This step helps in maintaining the continuity and financial stability of your operations.
Step 3: Communicate with stakeholders
Clear communication with all stakeholders is vital. Inform employees, suppliers, and customers about the shutdown schedule. Transparent communication ensures everyone is prepared and can plan accordingly, minimizing disruptions.
Step 4: Prioritize safety
Conduct a comprehensive safety audit and ensure all safety protocols are in place. Provide training and personal protective equipment (PPE) to your team. Remember, a safe shutdown is a successful shutdown.
Step 5: Consider energy management
Evaluate your facility’s energy consumption patterns. Utilize this shutdown period to upgrade to more energy-efficient systems. Embrace sustainability by integrating renewable energy sources and reducing your carbon footprint.
Step 6: Collaborate with experts
Engage with external experts and service providers who specialize in maintenance and energy management solutions. Their expertise can provide innovative insights and ensure that your facility operates at its best.
Step 7: Perform detailed inspections
Inspect all equipment, machinery, and infrastructure thoroughly. Look for signs of wear and tear, corrosion, and other potential issues. Use the latest diagnostic tools and technologies to ensure a comprehensive evaluation.
Step 8: Implement upgrades and repairs
Address any identified issues promptly. Implement necessary repairs, replacements, and upgrades. This proactive approach extends the life of your equipment, enhances efficiency, and reduces the risk of unexpected failures.
Step 9: Test and validate
Once all maintenance tasks are completed, conduct rigorous testing and validation. Ensure all systems are functioning optimally before resuming regular operations. This step guarantees reliability and performance.
Step 10: Document everything
Maintain detailed documentation of all maintenance activities, inspections, and repairs. This record-keeping is crucial for future reference and helps track the effectiveness of your maintenance strategy.
Step 11: Improve continuously
After the shutdown, review the entire process with your team. Identify areas for improvement and implement best practices for future shutdowns. Use this as an opportunity to embrace feedback and innovation to foster a culture of continuous improvement.
By following these 11 steps, you not only ensure the smooth and efficient operation of your facility but also empower your organization to meet future challenges with confidence. If you get stuck, reach out — Schneider Electric is here to support you every step of the way.
About the author
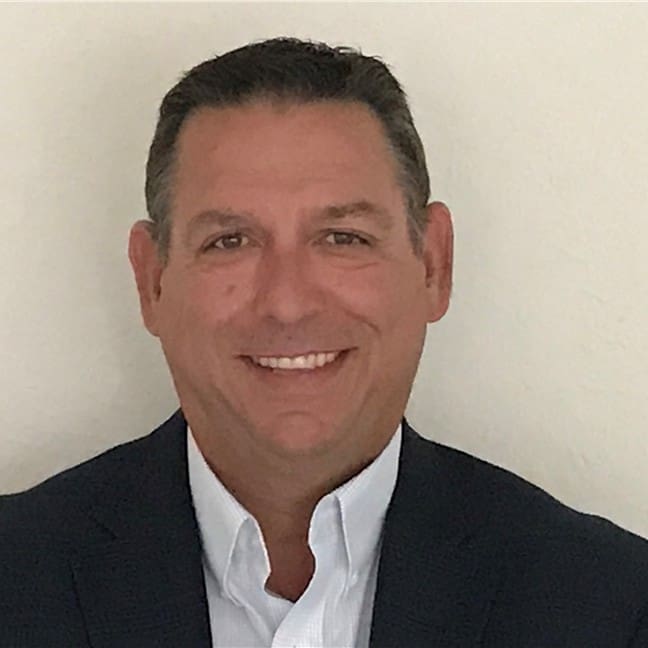
William Bentz,
Vice President of Service Execution,
Schneider Electric, NAM
Bill Bentz is the Vice President of Service Execution within the U.S. Services organization and is responsible for SE’s Secure Power, Power and ASCO Field Service Representatives and 3 Modernization (Ecofit) Facilities.
Add a comment