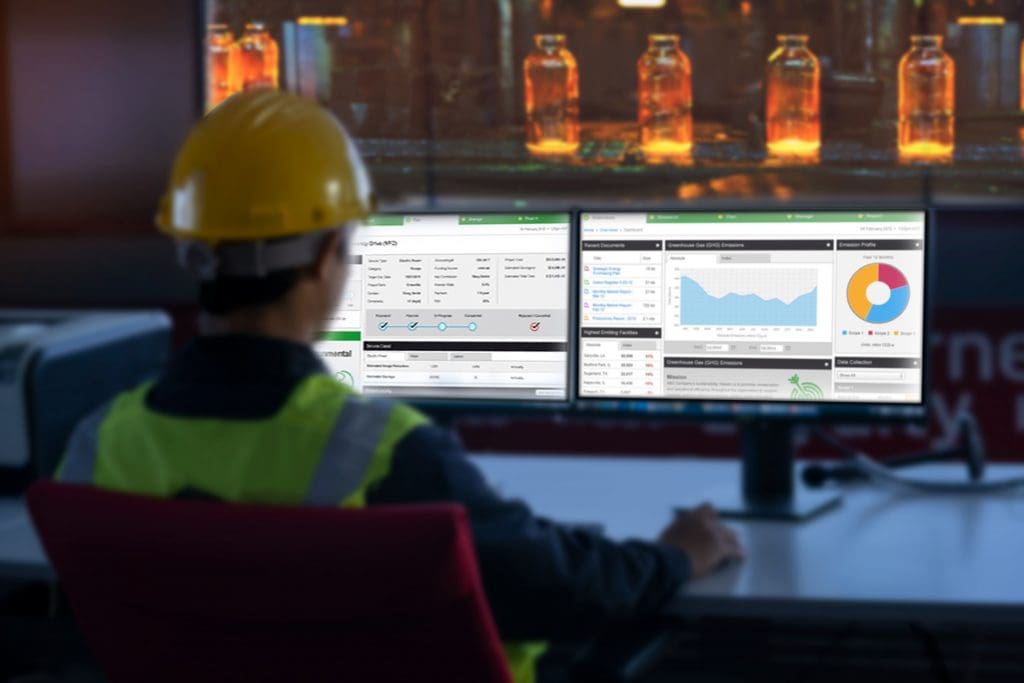
Siloed systems within mining, minerals, and metals operations often result in inefficiencies, isolation, and data transmission issues and loss, making operational efficiency a real challenge. Programmable logic controllers (PLCs) alone—industrial computers designed to control manufacturing processes—cannot create the complex, flexible, highly integrated control and automation systems that industrial operations increasingly demand, especially in a fast-paced technology landscape and growing ecosystem of partners.
A lack of system integration:
- Slows strategic decision-making for chief technology officers (CTOs), information technology (IT), and operational technology (OT) integration managers
- Hampers the ability of plant managers to respond to operational inefficiencies promptly.
- Hinders convergence of IT and OT networks, data, and processes, which misses the opportunity of valuable insights that empowers both domains and significantly improve their performance.
Achieving seamless IT/OT convergence within the mining, minerals, and metals industry is crucial for maintaining competitiveness and driving sustainability. Integrated, efficient, and sustainable industrial automation systems can predict problems and empower operators to prevent and even solve them before they occur. This convergence of IT and OT systems can improve operational efficiency by up to 25% by reducing unplanned downtime.
Let’s explore the transformative potential of advanced automation systems in revolutionizing operations, focusing on their ability to integrate IT and OT layers, improve operational efficiency, and support sustainable practices.
Breaking down barriers and the role of automation
Today’s legacy automation systems lack flexibility; changes require extensive reprogramming and reconfiguration, lengthy downtimes in some cases, and higher costs. Aging infrastructures and a retiring workforce compound these challenges. Maintaining outdated technology is more demanding and creates higher risks that can be mitigated through modernization, and as younger workers familiar with modern digital tools arrive, knowledge gaps emerge.
Improving environmental impact and sustainability measures are critical to the industry. Traditional mining practices contribute significantly to land degradation, water pollution, and carbon emissions—between 4% and 7% of worldwide GHGs. Operations are energy-intensive and environmentally impactful. The industry recognizes the need for more sustainable practices and advanced technologies to optimize energy use and reduce waste.
Addressing these challenges can be significantly accelerated by integrating IT and OT layers to generate actionable insights and unlock areas of collaboration that create more flexible, agile, and impactful automation solutions. This involves adapting to new technologies, optimizing data use, enabling predictive maintenance, and streamlining workflows for more agile and efficient operations. The result brings improved operational efficiency, reduced environmental impact, a competitive edge, and resilience.
An impactful example of the impact of utilizing new technologies is visual inspection powered by integrating artificial intelligence (AI) and machine learning (ML). AI-powered cameras inspect and flag faulty anodes for operators to avoid further processing. The OT layer feeds this back to the IT layer for production planning and scheduling adjustment. This saves time and money for metals producers. There are numerous other examples, including real-time stockpile volume calculation and conveyor belt health monitoring. One common element among these examples is the utilization of emerging technologies provided by various providers in the ecosystem, something we could only have achieved with strong integration and open standard communication.
Uniting forces: IT/OT and people
IT and OT convergence—bringing physical (OT) devices into the digital (IT) space — is not new. For example, today’s automobiles have sensors and cameras enabling situational data collection and real-time traffic data. Combined, the data allows drivers to make better decisions about vehicle maintenance or for real-time alternate routes during a journey. This streamlined access to data eliminates the need for manual data gathering from disparate systems. For instance, centralized data platforms can provide plant managers instant access to production metrics and environmental monitoring data.
People — engineers, IT specialists, and operators — are at the heart of this convergence and gain several benefits:
- Enhanced collaboration allows engineers, IT specialists, and operators to work together more effectively, breaking down traditional silos. For example, real-time data sharing between geological analysts and mining operators can optimize extraction processes.
- Innovations harness the full potential of a diverse workforce, driving continuous improvement and innovation. Integrating artificial intelligence (AI) for predictive maintenance in mining could foresee equipment failures, reducing downtime and repair costs.
- Quick decision-making usingreal-time data flow enables more efficient responses to challenges. In metals processing, immediate data on furnace temperatures and material properties can lead to swift adjustments, maintaining product quality and reducing waste.
- Reduced workload on individual employees, freeing them to focus on strategic tasks that add greater value to the company. For example, automated reporting can free engineers time to focus on system improvements and innovation.
- Enhanced safety via real-time equipment condition monitoring proactively prevents downtime and protects workers from potential hazards, creating a safer, more secure working environment. For instance, continuous monitoring of ventilation systems in underground mines ensures air quality and worker safety.
Proprietary vs. open: Automation in action
EcoStruxure™ Automation Expert is an integrated development environment based on the IEC 61499 standard. It facilitates the design, deployment, and management of industrial control systems using universal automation principles.
EcoStruxure Automation Expert’s open, software-defined automation approach redefines industry expectations by enhancing interoperability through orchestration, streamlining processes, and supporting future-proof scalability. It unifies customers’ installation base, enabling seamless management of different control systems. Acting as a middleware layer, it orchestrates process controllers, offering unified insights and visibility into previously isolated systems. Additionally, it integrates cutting-edge technologies like AI and digital twins for predictive maintenance and real-time monitoring. The flexibility of the platform reduces infrastructure needs and environmental impact, ensuring mining, mineral, and metal facilities remain competitive, efficient, and resilient to evolving operational requirements.
Take, for example, the recent Sirea project, which used advanced automation to modernize a mining installation, transforming it from outdated equipment into a state-of-the-art system. Using EcoStruxure Automation Expert, they achieved significant efficiency gains. Engineers benefited from modular, flexible systems that were easy to adapt and expand. This modularity allowed for quick reconfiguration and scalability, reducing downtime and enabling swift responses to changes in production demands without extensive reprogramming.
Hardware-independent and software-defined automation
Asset centricity in control systems like EcoStruxure Automation Expert means that every piece of equipment has its own object loaded with visual and control facets, interlocks, and communication, which can be designed and deployed on any compatible hardware. This opens possibilities for the future of mining, minerals, and metals. These operationally agile, collaborative, and open environments foster collaboration, innovation, and continuous improvement. They empower Engineers, Operators, IT/OT Specialists, and System Integrators with data and analytics to create a connected, secure, and agile infrastructure that can drive business growth and success.
Traditionally, PLC programs can run only on a specific PLC. This new era of software-defined automation enables automation professionals to run portions of the program on a PLC, a smart variable speed drive (VSD), an industrial PC, or even a Raspberry Pi. This revolutionizes edge computing and opens a new area of service-type control applications that support main or central control strategies in a seamless and efficient manner.
An example of this is in a continuous glass process that runs 24/7 and requires two variable-speed drives in hot standby. Traditionally, you would have a central PLC or DCS to do this. Now, thanks to the new control system’s asset-centric hardware-independent abilities, you can run the portion of the program that ensures both variable-speed drives are in hot standby on the drive itself rather than on the PLC.
To learn more about EcoStruxure Automation Expert, visit our forum to ask questions, grow your knowledge, and find technical experts in Industrial Automation.
Add a comment