Have you ever wondered how some facilities achieve operational efficiency while others struggle with downtime and inefficiencies? It’s not about the number of robots on the shop floor, but how data is harnessed and utilized. Welcome to the world of industrial digital transformation where data, people, and technology converge to turn traditional operations into smart ones.
Data as the heart of smart operations
Imagine a world where every piece of equipment in your facility communicates in real-time, signaling when a motor is about to fail or when inventory levels are running low. This isn’t a futuristic dream but the crux of smart operations. Data is the defining element that differentiates smart factories from their traditional counterparts. With smart operations, workers have access to real-time data that allows them to pre-empt issues before they escalate into major problems. With the right data architecture, even advanced technologies like AI and the industrial metaverse become accessible and functional tools.
Many U.S. facilities have adopted some components of digital transformation into their operations, but there’s still significant room for growth. According to the World Economic Forum (WEF), 70% of manufacturers are stuck in what’s often called “pilot purgatory,” where they’ve initiated digital projects but haven’t been able to fully scale them. Only 5% of warehouses are using advanced automation systems to unlock valuable data.
Digital transformation streamlines operations, enhances safety, and keeps companies competitive – so what is holding the industrial sector back?
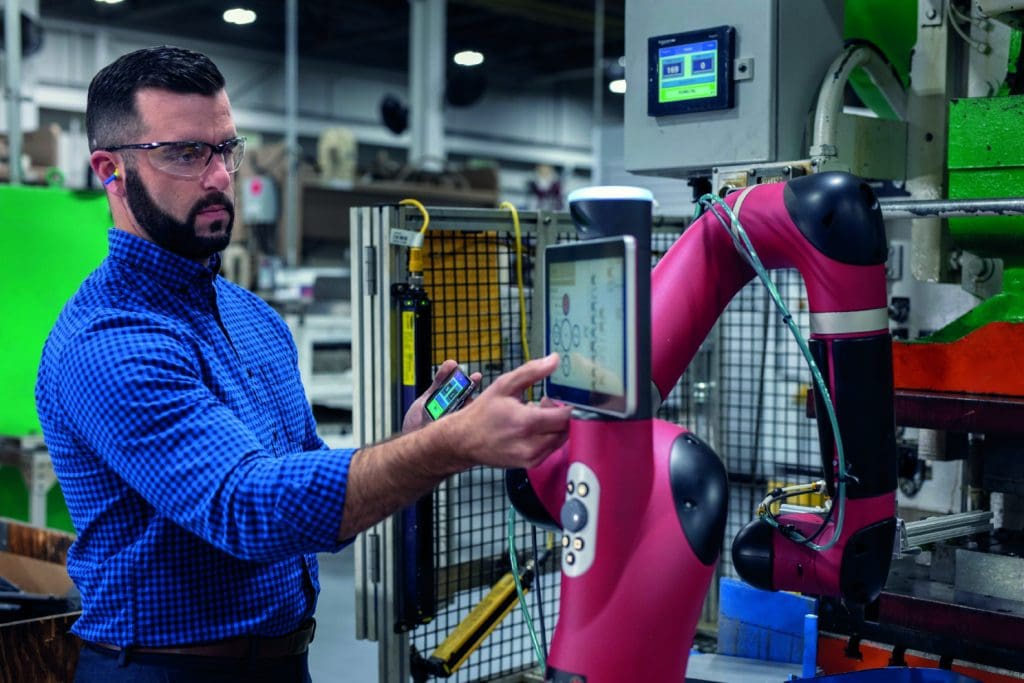
Navigating the roadblocks
Digital transformation is no small feat. It requires holistic changes in people, processes, and technology. When you transform digitally, you are completely transforming how you operate, and to do so, nothing can happen in isolation.
People
Successful digital transformation hinges on people even more than technology. This includes breaking down the traditional silos between information technology (IT) and operational technology (OT) teams. Usually, there’s a cultural barrier: OT teams worry IT will “break” their systems, and IT teams often lack operational know-how. Leadership is key to bridging this gap by clearly communicating the goals and value of transformation.
Processes
Manual workflows reliant on pen, paper, and Excel sheets can’t cope with the demands of a smart operations. Implementing changes can disrupt long-standing habits and create friction, but engaging the workforce early can ease the transition. Lean Management, which focuses on reducing waste and finding efficiencies, should be integrated into new digital workflows.
Technology
Upgrading legacy technology is non-negotiable. The Fourth Industrial Revolution has brought incredible advancements like the industrial Internet of Things (IIoT), AI, and Private 5G (P5G). But these technologies need connectivity on a modern “digital core” to function. Think of connectivity as the “concrete” foundation on which you build your digital house. This includes not just connecting machines to computers but also ensuring robust cybersecurity and data management practices.
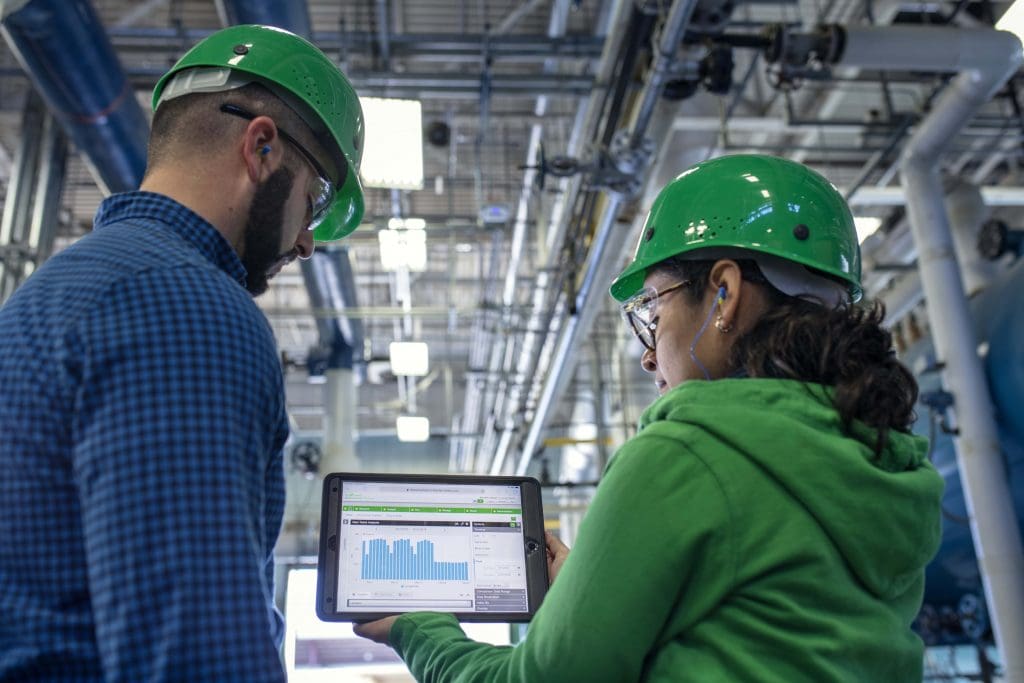
The path to digital transformation
Schneider Electric has developed a three-stage approach to digital transformation based on experience and expertise:
Stage 1: Evaluate your site
The initial phase of industrial digital transformation involves assessing and road-mapping to create the foundation for the entire journey. No two transformations share the same starting point, but all successful transformations focus on people, processes, and technology as core enablers for change. Engage your team, bridge IT and OT teams, and let leadership drive innovation.
Stage 2: Digitize the core
This stage focuses on digitizing basic operations, replacing analog methods with digital frameworks. Key steps include establishing a solid foundation of network connectivity, creating Lean management processes, and implementing robust cybersecurity measures.
Stage 3: Digitize at scale
Once the core is digitized, it’s time to scale these practices across the plant. This stage emphasizes centralizing data systems and standardizing processes across multiple sites. Successful scaling requires a coordinated approach, supported by a combination of necessary, unavoidable, and unnecessary variety management. Adopting an advanced manufacturing blueprint across multiple sites poses its own set of challenges, especially given the unique operational characteristics of each site.
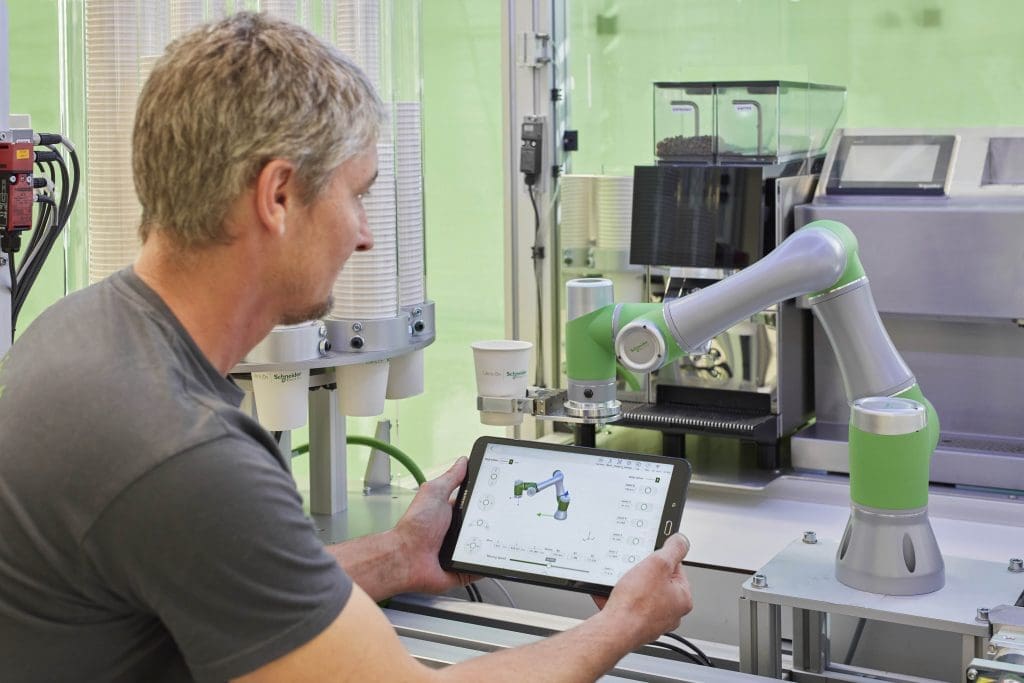
Why transformations succeed — or fail
Repeatedly, transformations fail due to organizational unpreparedness, a lack of equipped personnel, unrealistic expectations, and poor focus on operational vision. Conversely, successful transformations are driven by committed leadership, clear vision, and the right partners.
Your roadmap to success
Digital transformation is a journey, not a destination. To be successful requires a focus on people, processes, and technology, balanced against a backdrop of continuous improvement. Whether your facility is a brownfield or greenfield site, the journey to smart operations is achievable. Every manufacturer can do this, and you don’t need to do it alone. Schneider Electric can help.
Are you ready to take the first step towards transforming your operations? Connect with us for a consultation or tour one of our smart facilities to see what’s possible.
To dive deeper into the path to achieving smart operations, read our in-depth whitepaper.
About the author
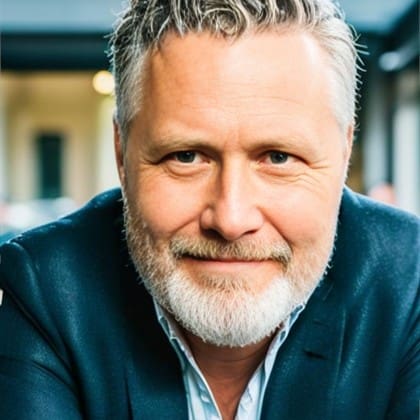
Gregory Tink,
Digital Transformation Consulting Director
Gregory Tink is an Operations Transformation and Technology specialist with over 20 years of industry and leadership experience primarily in oil and gas and mining. Over his career, Gregory has owned 4 businesses focused on operational excellence, technology enablement, and organizational transformation. In these businesses, he worked with a variety of clients to transform operations digitally. This included standing up operations and control centers, the implementation of operations, asset optimization, and maintenance platforms, the rollout of cyber security and risk strategies, the integration of OT/IT, and the integration of business functions supporting value chain alignment and the digital thread across the asset lifecycle.
Add a comment